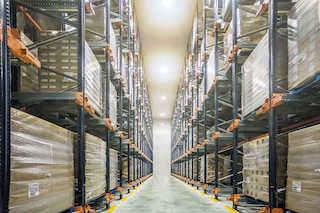
Mindestbestand: Was ist das und welche Strategien sind zu beachten?
Die Klassifizierung des Inventars eines Unternehmens in verschiedene Bestandsarten erleichtert die Kontrolle über die operativen Bestände in der Supply Chain. Die gelagerte Ware nimmt mit jeder Bestellung ab. Als Reaktion auf diese Bestandsschwankungen finden wir zwei Schlüsselkonzepte:
- Der Höchstbestand wird durch die Kapazität des Lagers und durch die Einkaufs- oder Versorgungspolitik des Unternehmens bestimmt.
- Der operative Mindestbestand definiert die Grenze an Gütern die mindestens im Lager sein müssen, kurz bevor der Sicherheitsbestand verwendet wird.
Die Mindest- und Maximalbestandsregel ist eine der am weitesten verbreiteten Methoden der Bestandskontrolle. In unserem Artikel werden wir ihren Umfang und ihre Grenzen analysieren und einige Methode auflisten, wie man den Mindestbestand im Lager optimieren kann.
Was ist der Mindestbestand? Die Mindest- und Maximalbestandsregel
Mit der Mindest- und Maximalbestandsregel wird ein Bestellpunkt festgelegt, an dem nach dem Verbrauch der Ware erneut eine Bestellung aufgegeben wird. Daher zeigt die grafische Darstellung Spitzen (beim Eingang neuer Ware) und Täler (beim Versand der Ware).
Es handelt sich um eine Methode, die leicht zu implementieren ist und mit fast jedem ERP oder LVS automatisiert werden kann. Auf diese Weise, wenn eine SKU oder Referenz eines Produkts den Mindestbestand erreicht, erstellt das System automatisch eine Benachrichtigung zum Meldebestand, sodass die Lagermanager in dieser Aufgabe entlastet werden.
Es gibt verschiedene Methoden zur Festlegung des Mindestbestands, doch die wichtigsten Variablen, die die Berechnung dieses Parameters beeinflussen, sind:
- Die Nachfrageprognosen: Wie viele Einheiten einer bestimmten SKU werden in einem vorgegebenen Zeitraum verbraucht?
- Die Lieferzeit des Lieferanten: Wie lange dauert es, bis die Bestellung bearbeitet ist und im Lager eintrifft?
- Die Kosten (und Größe) der Bestellung und die diesbezüglichen Regeln des Lieferanten.
Grafische Darstellung des Bestandsverlaufs
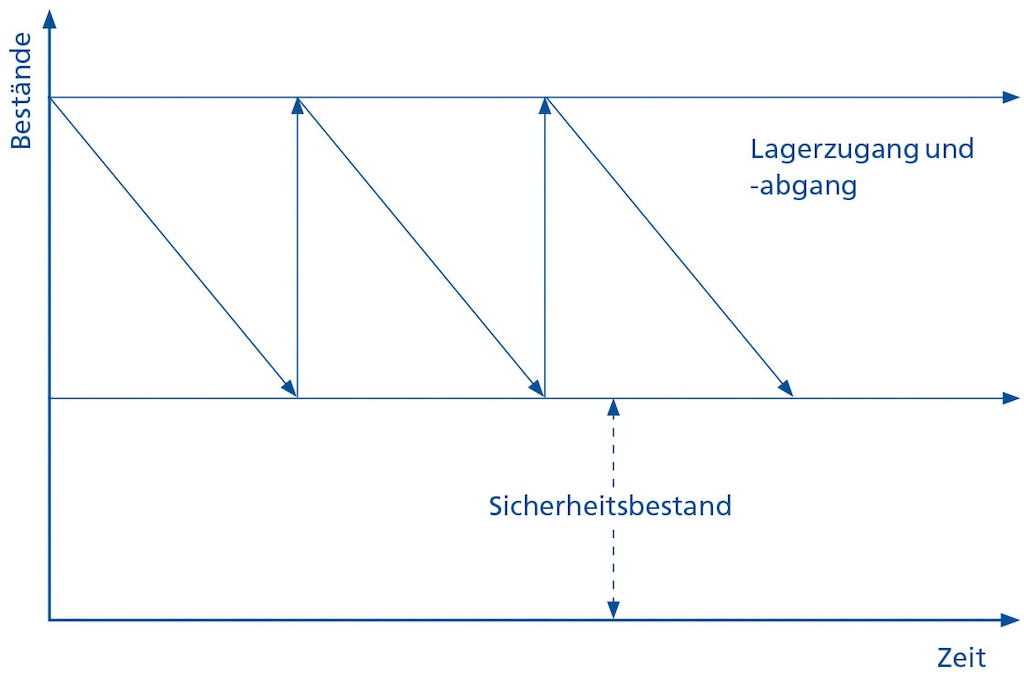
Welche Einschränkungen hat die Mindest- und Maximalbestandsregel?
Die Mindest- und Maximalbestandsregel ist einfach und leicht zu implementieren, deshalb wird sie in vielen Unternehmen verwendet. Sie hat jedoch Einschränkungen, die beachtet werden sollten:
- Sie ist auf einzelne SKU fokussiert, ohne dabei die Gesamtübersicht aller Lagerbestände oder Lieferanten zu berücksichtigen. Es gibt z. B. Lieferanten, die eine Mindestbestellung vorschreiben, die jedoch auf mehrere Produkte ihres Katalogs verteilt werden kann. Bei der Mindest- und Maximalbestandsregel wird der Auftrag dann erteilt, wenn die erforderliche Mindestanzahl einer einzigen Referenz erreicht wird, jedoch kann es wirtschaftlich sinnvoll sein die Mindestbestellung auf verschiedene SKUs zu verteilen.
- Sie berücksichtigt nicht immer die Evolution der Produkte selbst. Jede Referenz hat einen Lebenszyklus mit mehreren Phasen, die die Nachfrage beeinflussen (Einführung, Wachstum, Reife und Degeneration). Wenn die Mindest- und Maximalbestandsregel nicht ständig manuell überarbeitet wird (was bedeutet, dass die Vorteile der Automatisierung dieses Prozesses verloren gehen), kann die kontinuierliche Nachschubbeschaffung zu kostspieligen Überbeständen führen.
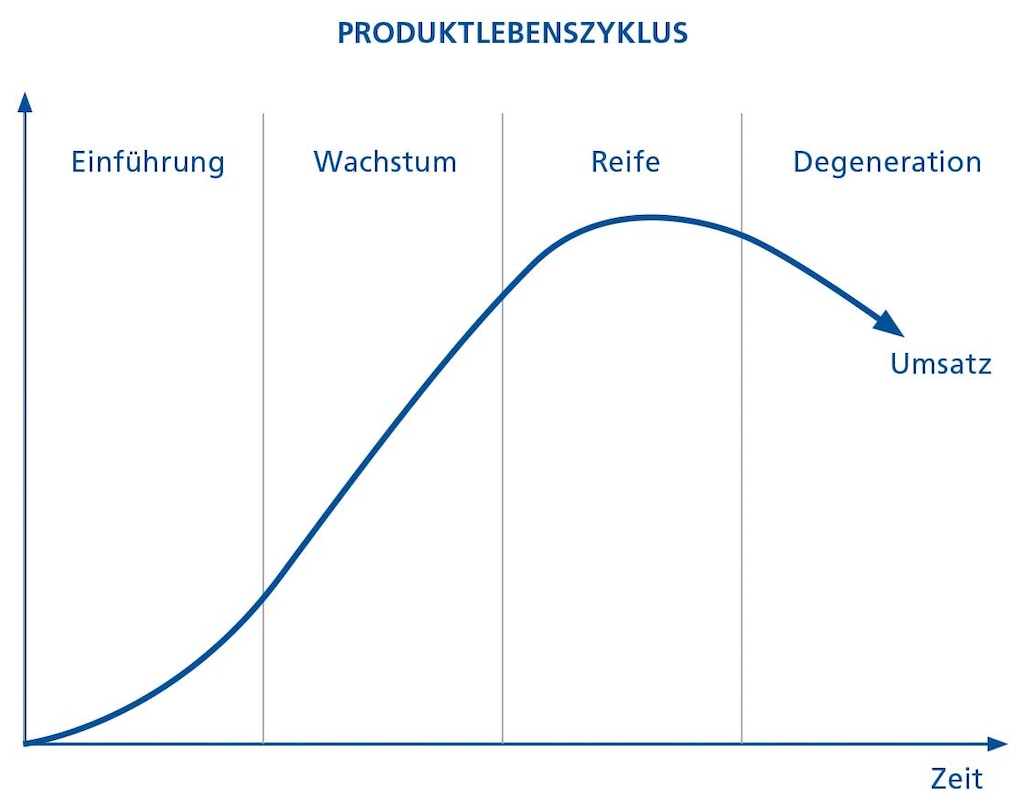
Vorteile einer verbesserten Mindestbestandsführung
Die Anwendung einer strengen Mindest- und Höchstbestandspolitik hat unter anderem zur Folge, dass mehr Bestände angesammelt werden als benötigt. Daher ist die Optimierung des Lagerbestands einer der Bausteine von Lean Logistik, deren Vorteile folgendermaßen beschrieben werden können:
- Sie verringert das stillgelegte Anlagekapital des Lagerbestandes. Welches eine Investition ist, die für andere Zwecke verwendet werden kann, um die Liquidität des Unternehmens zu gewährleisten.
- Die Kosten für die Aufrechterhaltung dieses Bestands werden reduziert, was zu einem wichtigen Teil der Lagerhaltungskosten gehört. Zudem verringert sich das Risiko, dass die Ware mit einem niedrigen Lagerumschlag veraltet und Verluste für das Unternehmen mit sich bringt.
- Die freigesetzte Lagerfläche kann z. B. für die Erweiterung des Katalogs, einen vergrößerten Kommissionierbereich oder für bestehende Bestände, die mehr Platz benötigen, verwendet werden.
Wie kann man also den Lagerbestand optimieren, um ihn auf ein Minimum zu beschränken?
Wir geben Ihnen folgende Empfehlungen:
- Klassifizieren Sie den Bestand Ihres Lagers und setzen Sie Prioritäten.
Für den Lagerumschlag werden die gelagerten Bestände überprüft und klassifiziert. Hier wird unbewegte Ware entdeckt, die ein Problem für das Bestandsmanagement darstellt. Mit einem Lagerverwaltungssystem ist es nicht nur möglich zyklische Zählungen durchzuführen, um die Genauigkeit der Inventur zu überprüfen, sondern auch um wertvolle historische Daten zu bewahren, die die Aufgabe der Bestandsoptimierung erheblich erleichtern.
Außerdem hilft diese Information bei der Prioritätensetzung der Mindestbestände derjenigen Referenzen, die unter Berücksichtigung verschiedener logistischer Parameter am interessantesten erscheinen: unter anderen Rotation, Rentabilitätsmargen und Lieferkosten. Auf diese Weise werden die Mindestbestände aller Referenzen aus einer globalen und nicht individuellen Sicht festgelegt, da sie alle um die gleiche Investition für Lagerbestände konkurrieren.
- Planen Sie mehr als nur die vom Mindestbestand markierten Zahlen.
Gelegentlich reflektiert die Mindest- und Maximalbestandsregel die Realität des Bedarfs des Unternehmens nicht. Dies ist vor allem dann der Fall, wenn sie genau eingehalten wird und so automatisiert wurde, dass Bestellungen nur dann aufgegeben werden, wenn der Warenbestand den Mindestbestand erreicht. Es ist jedoch ratsam, den Warennachschub nicht nur unter Berücksichtigung des Warenbestands zu planen, sondern auch unter Berücksichtigung aller anderen logistischen Faktoren.
Andernfalls kann das Lager bei der Warenannahme überlastet werden oder, wenn Waren automatisch beim Lieferanten bestellt werden, kann das Unternehmen gewisse Versandvorteile nicht nutzen, wie z. B. die Möglichkeit der Konsolidierung von Waren. In jedem Fall sollte das Lager auf unvorhergesehene Ereignisse dieser Art vorbereitet sein. Der Einsatz eines LVS ermöglicht es unvorhergesehene Wareneingänge durchzuführen und die anschließende Lagerplatzverwaltung dieser Waren zu organisieren.
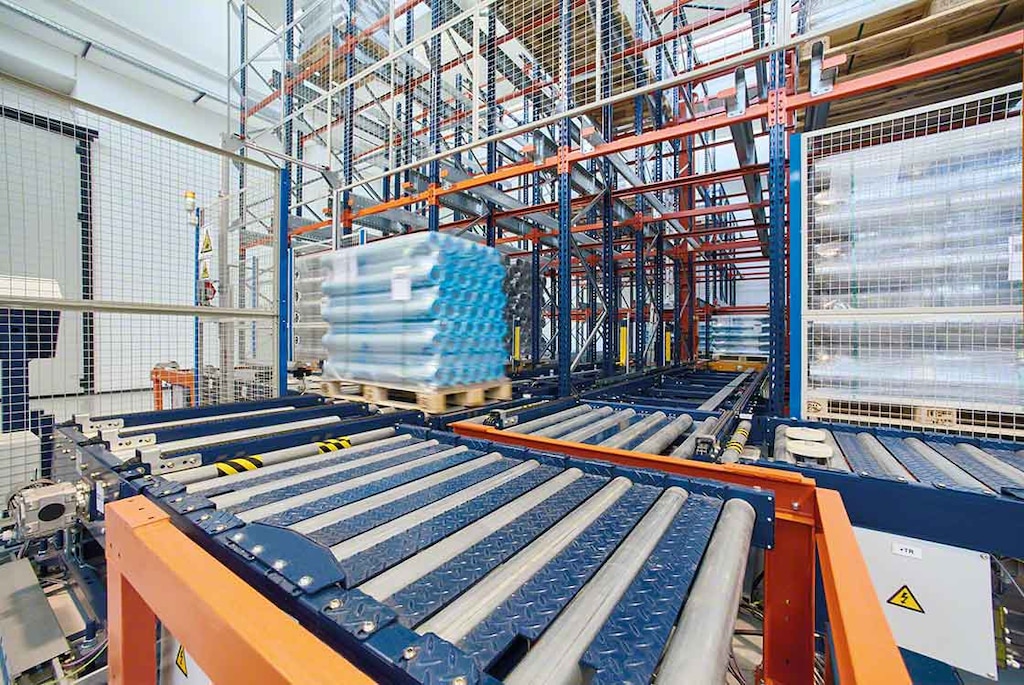
- Setzen Sie auf ein effizienteres Lager und senken Sie die Betriebskosten
Die Hauptfunktion des Inventars besteht darin, dem Unternehmen die Fähigkeit zu geben zeitgerecht und formgerecht auf Nachfrage zu reagieren. Trotz Strategien, wie dem Just-in-Time-Verfahren, das versucht, sich dem Zero Inventory-Konzept anzunähern, ist die Lagerhaltung von Beständen für eine funktionierende Lieferkette notwendig. Und wird immer notwendig bleiben.
Ausgehend davon, dass das Lager einen Mindestbestand haben sollte, sollte die Zeit der gelagerten Waren weitestgehend reduziert werden, um die Betriebskosten so niedrig wie möglich zu halten. Um dies zu erreichen ist es sinnvoll, an der Leistungsfähigkeit des Lagers zu arbeiten, indem Sie die Durchlaufzeit oder Lead Time verbessern. Diese kann je nach Art in zwei Gruppen eingeteilt werden.
- Manufacturing Lead Time: Diese bezieht sich auf die Zeit, die für den Transport der Waren von einem Ort zum anderen benötigt wird. Die Automatisierung von Prozessen, wie die Warenbewegungen im Lagerbereich, entlastet die Mitarbeiter und diese können sich so wertvolleren Aufgaben widmen.
- Information Lead Time: Diese bezieht sich auf die Zeit, die für die Bearbeitung von Aufträgen, die Erstellung von Kommissionierlisten und die Organisation aufgewendet wird. Das LVS ist in diesem Zusammenhang ein wertvolles Hilfsmittel, das nicht nur die Zykluszeiten reduziert, sondern auch die Ausführung von Operationen perfektioniert, bis Fehler praktisch beseitigt sind.
Außerdem ist die Kontrolle der Dynamik zwischen den verschiedenen Lagerbeständen unerlässlich, um einerseits die befürchtete Out-of-Stock Situation zu verhindern und andererseits die Überdimensionierung der Sicherheitsbestände zu begrenzen. Auch hier spielt das LVS eine wichtige Rolle, da es alle wichtigen KPIs berücksichtigt, um richtige Entscheidungen zu treffen. Die Softwarelösung Easy WMS Supply Chain Analytics zeichnet sich in dieser Hinsicht aus.
Die Herausforderung der Festlegung von Mindestbeständen
Die finanziellen Auswirkungen des Lageraufbaus und die zunehmenden Schwankungen der Nachfrage haben viele Unternehmen gezwungen, die Richtung ihrer Logistikstrategie zu ändern und zu versuchen ihre Lagerbestände so weit wie möglich zu reduzieren. Dies hat die Grenzen der klassischen Mindest- und Maximalbestandsregel aufgezeigt. Um sie an eine immer komplexere Realität anzupassen, müssen spezialisierte Arten von Logistikmanagementsoftware integriert und Entscheidungen auf der Grundlage messbarer Daten getroffen werden.
Wenn Sie Ihr Lager in eine agil und präzise gestalten möchten, setzen Sie auf ein hochwertiges LVS. Kontaktieren Sie uns für eine personalisierte Demo des Easy WMS mit allen seinen Lagerverwaltungsfunktionen.