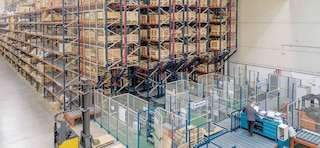
Was bedeutet Lean Logistik? Eine Strategie der Effizienz
Die Methode der Lean Logistik stammt aus dem Japanischen und beschreibt die Philosophie der Verschlankung von logistischen Prozessen. Das Ziel von Lean Logistik ist, jene Aktivitäten zu identifizieren und zu eliminieren, die keinen Mehrwert bringen, um die Geschwindigkeit und den Fluss der Produkte zu erhöhen und so die Kosten zu minimieren.
Das Lean-Konzept wurde von Taiichi Ohno bei Toyota im Bereich der industriellen Produktion entwickelt, daher auch die ursprüngliche Bezeichnung Lean Production. Es lässt sich am ehesten zusammenfassen mit: “durch weniger von allem mehr erreichen”. Damit sind beispielsweise folgende Faktoren gemeint: weniger Aufwand, weniger Zubehör, weniger Platz, weniger Kosten und weniger Zeit.
Grundlagen und Definition der Lean Logistik
Lean Logistik zielt darauf ab, die Logistikkosten zu senken, indem es den Schwerpunkt auf die Erkennung und Bewältigung von Aufgaben legt, die keinen Mehrwert für den Prozess generieren. Dadurch wird eine Verkürzung der Durchlaufzeit erreicht. Es ist im Grunde genommen eine ständige Suche nach Effizienz, die in mehrere Phasen unterteilt werden kann:
1. Identifizieren der Aktivitäten, die einen Mehrwert für den Kunden haben
Mit betriebswirtschaftlichen Methoden wie der Wertstromanalyse (engl. Value Stream Mapping, VSM) können in einem ersten Schritt nicht-wertschöpfende Aufgaben innerhalb eines bestimmten Prozesses identifiziert werden. Beispielsweise werden im Lager die Kommissioniervorgänge in mehrere Phasen unterteilt, wobei jede dieser Phasen in weitere Teilprozesse aufgegliedert werden kann.
2. Verschwendung erkennen und gleichzeitig Verbesserungsmöglichkeiten finden
In der Logistik ist Verschwendung oft mit Zeitverlust verbunden, wie wir später sehen werden. Die Standardisierung der Aufgaben und die Aufrechterhaltung von Sauberkeit und Ordnung im Lager sind unerlässlich, um diese Phase optimal durchzuführen.
3. Erstellen eines neuen optimierten Prozessablaufs (Wertstromdesgin)
Mit Hilfe dieses Werkzeugs wird der “Soll-Zustand” entworfen, der den Prozess in der Zukunft hinsichtlich Zeitaufwand und Servicequalität effizienter machen soll. Zu diesem Zweck müssen unnötige Aufgaben, die als Verschwendung identifiziert wurden, beseitigt werden. Neben organisatorischen Veränderungen kann diese Phase Investitionen in neue Technologien oder Systeme beinhalten, die dazu beitragen, diejenigen Phasen zu eliminieren, die zusätzliche Zeit in Anspruch nehmen, ohne Mehrwert zu schaffen.
4. Pull-Strategien anwenden zur Bestandsminimierung
Die Lagerhaltung bestimmt einen großen Teil der Logistikkosten. Im Gegensatz zur Push-Strategie, die auf der Produktion im Rahmen einer Verkaufsprognose basiert, konzentriert sich die Pull-Strategie strategisch auf den Konsumenten, der das Produkt kaufen soll. Sie ist also nachfrageorientiert. Alle Prozesse der Produktion werden hierbei erst durch eine eingegangene Kundenbestellung ausgelöst.
5. Neue Prozesse standardisieren und auf Veränderungen reagieren
Zu diesem Zweck müssen alle Arbeitnehmer einbezogen, motiviert und entsprechend geschult sein, damit sie den Anforderungen gerecht werden und die erforderlichen Fähigkeiten erwerben können, die das so genannte Talent 4.0 ausmachen.
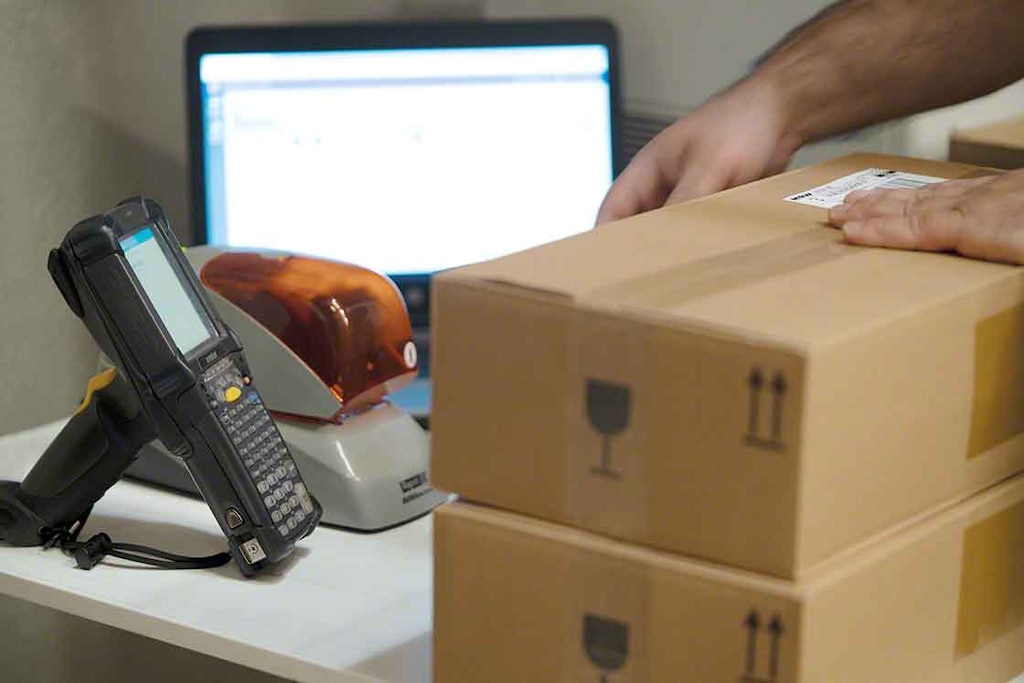
Nicht-wertschöpfende Situationen und ihre Beseitigung nach dem Konzept der Lean-Logistik
In den vier nachfolgend aufgeführten Situationen kommt es am meisten zu irgendeiner Art von Verschwendung. Welche Lösungen gibt es dafür?
- Lagerüberbestände
Die Ursachen für einen unangemessenen Anstieg der Lagerbestände liegen in der Regel in einem Produktionsüberschuss bei produzierenden Unternehmen, aber auch in einer schlechten Nachfrageprognose. Manchmal ist es auch der Sicherheitsbestand, der unter dem Vorwand der "Abdeckung" erweitert wird. Er verschleiert jedoch in Wirklichkeit ein schlechtes Lieferantenmanagement oder eine mangelhafte Organisation der Materialflüsse.
Dies führt zur Belegung ungenutzter Lagerflächen, was erhöhte Lagerkosten durch gebundenes Kapital und die Pflege von wenig umgeschlagenen, kaum erneuerten Beständen zur Folge hat.
-Wie kann man dies aus der Sicht der Lean Logistik lösen?
Um in dieser Situation den Prinzipien der Lean Logistik zu folgen, ist es notwendig, vor allem an den Faktoren zu arbeiten, die kontrolliert werden können (im Gegensatz zu anderen schwankungsanfälligen, wie z. B. der Nachfrageprognose). Einige der Maßnahmen, die im Lager durchgeführt werden können, sind:
- Die Anwendung der Cross-Docking-Konzepts, das den gelagerten Bestand auf ein Minimum beschränkt.
- Die Implementierung des Just-in-Time-Verfahrens im Lieferantenmanagement und in der Organisation des Lagers.
- Verkürzung der Durchlaufzeiten sowohl für Lieferanten als auch für intralogistische Prozesse. Das erleichtert die Berechnung von Nachfrageprognosen: Sie sind umso genauer, je zeitnaher sie sind. Überbestände werden vermieden.
- Wartezeiten und Engpässe
Lean Logistik basiert auf der Reduzierung der Differenz zwischen der Ausführungszeit (Arbeitszeit, die Sie Ihren Mitarbeitern zahlen) und der Standardzeit (Zeit, die Sie dem Kunden in Rechnung stellen). Das Ergebnis dieser Maßnahme wird sich in Kosten niederschlagen, die durch die Aufdeckung von Ineffizienzen eingespart werden können.
Die Ursachen können sehr unterschiedlich sein und hängen in der Regel mit einer ungünstig gestalteten Arbeitsweise, ignorierten Problemen oder Ungleichgewichten in der Arbeitsbelastung der Mitarbeiter zusammen.
-Wie kann man dies aus der Sicht der Lean Logistik lösen?
- Um Aufgaben im Lager zu organisieren und Engpässe und Ausfallzeiten zu vermeiden, gibt es kein besseres Werkzeug als ein Lagerverwaltungssystem. Diese Software unterstützt das Lager dabei, große Mengen an Informationen zu verarbeiten und zu organisieren, wobei sie die Prozessoptimierung in den Vordergrund stellt.
- Messen und kontrollieren Sie die Arbeitsbelastung jedes einzelnen Mitarbeiters, um zu verhindern, dass einige unterbeschäftigt und andere überlastet sind. Das Modul Software für das Labor Management System für Easy WMS ist speziell für die Steuerung dieses Bereichs vorgesehen.
- Um zu verhindern, dass Anlagenausfälle die Lagertätigkeit verlangsamen, sollte es als vorbeugende Maßnahme einen Wartungsplan für Arbeitsgeräte und automatische Systeme geben. Darüber hinaus muss technische Unterstützung gewährleistet sein, um das Problem so schnell wie möglich zu beheben.
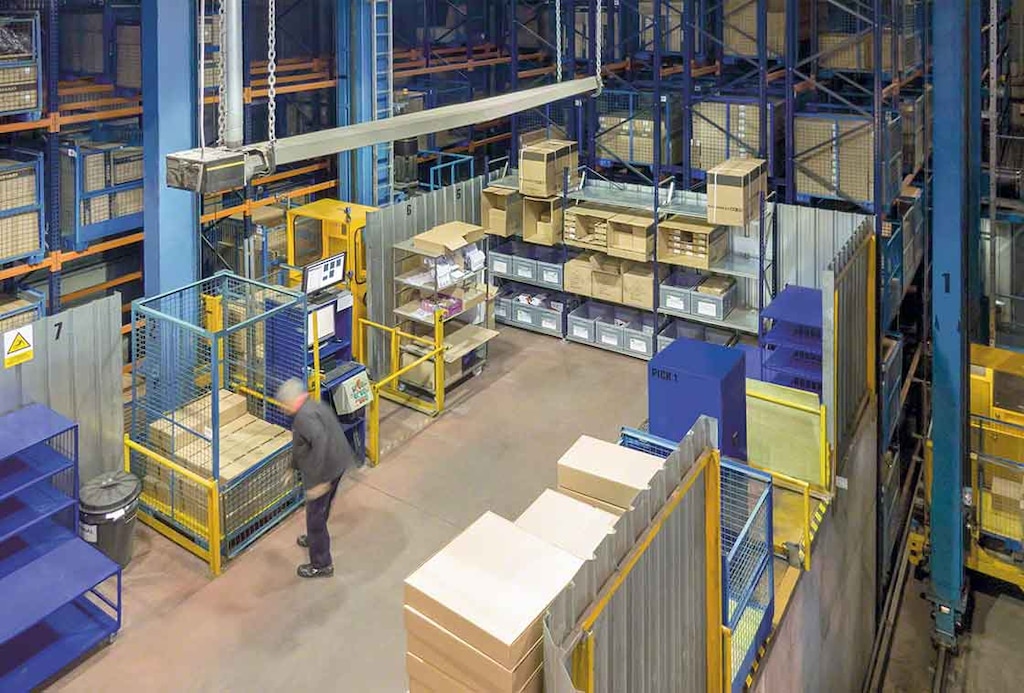
- Unnötige Fahrten und Wege
Kommissionierprozesse sind die zeitaufwendigsten Aufgaben im täglichen Betrieb. Eine schlechte Planung der Kommissionierlinien kann der Produktivität schaden, beispielsweise durch Leerfahrten oder überflüssige Bewegungen.
-Wie kann man dies aus der Sicht der Lean Logistik lösen?
- Die Automatisierung der Handhabung von Lasten ist eine hervorragende Maßnahme, um die Zeit für den intralogistischen Transport zu reduzieren und gleichzeitig die Sicherheit im gesamten Betrieb zu erhöhen. Bei diesen sich wiederholenden Prozessen erzielt die Automatisierung optimale Ergebnisse. Ebenso sind beispielsweise Regalbediengeräte in der Lage, in kombinierten Zyklen zu arbeiten, so dass alle lasttragenden Bewegungen genutzt werden.
- Die Kommissioniermethode hat auch Auswirkungen auf die Verschwendung durch zu viele Bewegungsabläufe. Ein LVS erleichtert die Organisation von Kommissionierwegen, konsolidiert oder gruppiert Waren und passt die Zeiten an die Disposition an.
- Fehler, die zu Retouren und Wiederholungen von Prozessen führen
Normalerweise ist ein höheres Qualitätsniveau auch oft mit höheren Kosten verbunden. Das ist aber nicht immer der Fall. Tatsächlich zeichnen sich die besten Unternehmen der Logistikbranche (und viele wenden Lean Logistik Methoden an) dadurch aus, dass sie einen erstklassigen Service zum besten Preis anbieten. Warum? Hauptsächlich aus zwei Gründen: weil sie es fast immer gleich beim ersten Mal richtig machen (und dadurch nicht doppelt arbeiten müssen) und weil sie auf diese Weise mehr verdienen können: Ein außergewöhnlich effizienter Service wirkt damit unterstützend.
-Wie kann man dies aus der Sicht der Lean Logistik lösen?
- Wenn die Retourenverwaltung den Lagerbetrieb erschwert, ist es an der Zeit, den Ursachen auf den Grund zu gehen. Wenn Fehler innerhalb der Auftragsvorbereitung der Grund sind, kann der Einsatz eines LVS als Kommissioniersoftware diese Fehler enorm reduzieren und die Qualität des Service erhöhen.
- Durch eine rechtzeitige Problemerkennung kann Doppelarbeit oder die Wiederholung von Aufgaben vermieden werden.
Lean Logistik: Der Fokus liegt auf dem “Weniger”
Das Konzept der Lean Logistik basiert auf der Annahme, dass der Kunde beim Kauf eines Produkts nicht für Aktivitäten bezahlt, die keinen Mehrwert für die Lieferkette darstellen. Die Anwendung der Lean Methoden in der Logistik konzentriert sich also auf das Beseitigen von Verschwendungen, die die Rentabilität der Logistik im Unternehmen beeinträchtigen.
Bei Mecalux richten wir uns nach unseren Kunden und arbeiten Seite an Seite mit ihnen. Dank unserer Automatisierungs- und Softwarelösungen zur Lageroptimierung können wir gemeinsam die gewünschten Ziele erreichen. Kontaktieren Sie uns und unsere Berater begleiten Sie mit ihrem Know-How auf dem Weg zu einer “schlanken” Logistik!