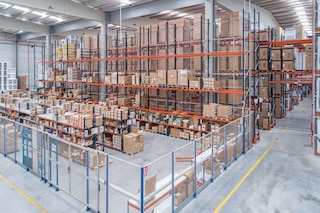
Die meist verwendeten Lagermethoden
Ziel des Standortmanagements ist es, das richtige Produkt am richtigen Ort zu platzieren, damit es zur richtigen Zeit auf effiziente Weise abgeholt werden kann.
Die Lagermethoden richten sich nach den Kriterien, nach denen die Produkte an den einzelnen Standorten organisiert werden sollen. Welche sind die am häufigsten verwendeten und welche Faktoren sollten bei der Auswahl berücksichtigt werden?
Welches sind die gängigsten Lagermethoden?
Es lassen sich zwei Arten von Regeln hervorheben:
- Feste oder spezifische Lagermethoden: Jeder gelagerten SKU wird zuvor eine bestimmte Position zugeordnet. Dies erleichtert die Lokalisierung von Produkten, ohne dass ein Computersystem diese aufzeichnen muss.
- Chaotische oder zufällige Lagermethoden: Produkte werden an den verfügbaren Positionen platziert, sobald sie im Lager eingehen. Für eine erfolgreiche Durchführung ist ein Lagerverwaltungssystem unabdingbar.
In vielen Lagereinrichtungen werden jedoch für die Warenorganisation die Lagermethoden miteinander kombiniert.
Wonach wird die Lagermethode bestimmt?
Die Verwendung der Lagermethode hängt hauptsächlich von drei Hauptthemen ab:
1. Eigenschaften der gelagerten Produkte:
- Physikalische Eigenschaften der Produkte: Volumen (Maße von Länge, Breite und Höhe) und Gewicht sind entscheidend, um den Platzbedarf der Handhabung zu ermitteln und schließlich die am besten geeigneten Lagersysteme festzulegen. So werden beispielsweise die schwersten Produkte nach Möglichkeit in Bodennähe platziert. Es wird empfohlen, eine gängige, vorzugsweise automatisierte, Methode zu verwenden, um jedes Produkt zu messen und mögliche Abweichungen zu vermeiden. Daher ist es üblich, bestimmte Standardkartongrößen zu verwenden, in die eine Referenz passt, um den Verpackungsprozess zu vereinfachen.
- Weitere Merkmale, die sich auf die Lagerung und den Standort von Produkten auswirken: Das sind beispielsweise die Berücksichtigung der Kompatibilität mit anderen Waren (die Lagerung chemischer Produkte ist gesetzlich geregelt), der Witterungsbeständigkeit (die Unterbringung im Freilager kann die Kosten senken) oder der Haltbarkeit bei verderblichen Produkten (sie müssen nach Datum, unter bestimmten Temperatur- und Feuchtigkeitsbedingungen bestellt werden, und die Charge muss als Maß für die logistische Rückverfolgbarkeit einbezogen werden).
2. Analyse der verfügbaren Lagersysteme und der Raumaufteilung
- Definieren Sie eine Gliederung, mit der alle Standorte ermittelt werden können: Sie muss mindestens die Kennzeichnung mit Zahlen oder Buchstaben der Kanäle oder Regale sowie jeder Ebene in der Höhe und Tiefe beinhalten; aber auch andere Abmessungen wie Lager, Gang, Behälter oder Zone können hinzugefügt werden.
- Berechnen Sie Lagerkapazität und Lagerbelegung: Wenn diese 90%-95% überschreitet, ist es ratsam, die Kriterien für den Lagerort zu überprüfen, um zu sehen, ob die Fläche optimal genutzt wird. Es sollten auch diverse Arten von Industrieregalen im Bereich von Kompaktsystemen oder Systemen mit Direktzugriff betrachtet werden. Generell sind erstere besser geeignet für Bestände mit vielen Paletten pro Referenz, während letztere vielseitiger sind, wenn nur wenige Paletten gehandhabt werden.
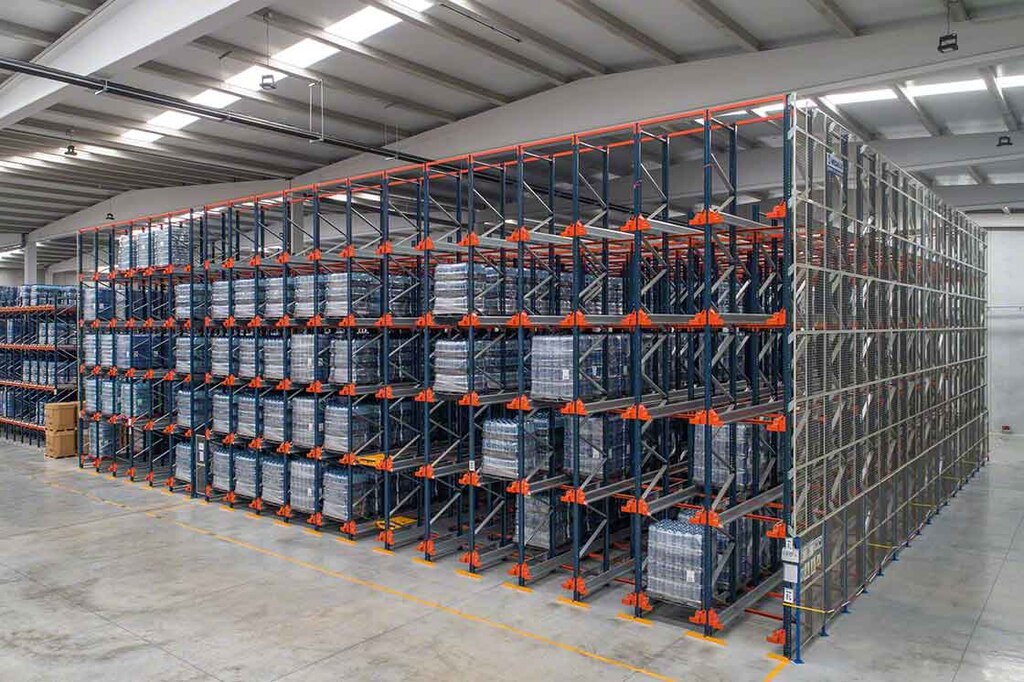
3. Analyse der Bewegungen von Waren und Mitarbeitern im Lager
- Warenbewegungen:
1. Lagerumschlag: Ermöglicht es, gelagerte Produkte nach der Entnahmehäufigkeit zu zu platzieren. Dies steht in direktem Zusammenhang mit der Nachfrage des gesamten Jahres. Nach der ABC-Methode besteht das allgemeine Kriterium der Lagermethode darin, die Waren mit dem höchsten Umschlag näher an den Docks des Warenein-und -ausgangs zu positionieren und die mit dem geringsten Umschlag am weitesten von den Docks entfernt.
2. FIFO- oder LIFO-Methode: bezeichnet die Reihenfolge der Entnahme. FIFO (First In, First Out) bedeutet, dass die zuerst eingelagerten Artikel auch als erste wieder entnommen werden. LIFO (Last In, First Out) heißt dagegen, dass die zuletzt eingelagerte Ware zuerst wieder entnommen wird.
- Bewegungen der Mitarbeiter:
Die von jedem Mitarbeiter zurückgelegte Wegstrecke hängt hauptsächlich von der angewandten Kommissioniermethode, der Zugänglichkeit der Produkte in den Regalen sowie von den Handhabungsgeräten und automatischen Systemen ab. Beispielsweise reduzieren Behälterfördersysteme oder Regalbediengeräte manuelle Tätigkeiten und die Wege der Mitarbeiter.
Das Standortmanagement zielt darauf ab, die Lagerkapazität zu maximieren, den Bewegungsaufwand zu minimieren und jeden Standort an die Eigenschaften der Produkte anzupassen.
Mit unserer Easy WMS-Software können wir die Standortbedingungen in Ihrem Lager detailliert analysieren und so den Bestand optimieren. Nehmen Sie Kontakt mit uns auf und wir helfen Ihnen, Ihre individuelle Lagermethode zu bestimmen.