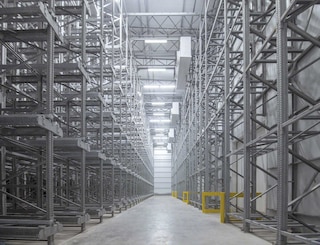
Kühllager: Aufbau und Automatisierung
Automatische Kühllager werden in der Logistik immer häufiger verwendet. Kälte zur längerfristigen Lagerung von Produkten zu nutzen ist keine neue Erfindung, da sie bereits im Mittelalter verwendet wurde. Dank der kontrollierten Temperatur behalten die Waren ihre Qualität und ihre Eigenschaften, wodurch der Lebenszyklus der Produkte im Lager verlängert wird.
Neue Verbrauchertrends haben die Branche der Kühllogistik noch mehr in Schwung gebracht. Laut einem Bericht des Beratungsunternehmens Markets&Markets wird die Industrie für Tiefkühlkost in den nächsten drei Jahren um 5,14 % pro Jahr wachsen und im Jahr 2023 einen weltweiten Umsatz von mehr als 283 Milliarden Dollar erreichen.
In diesem Artikel wird erläutert, wie ein Kühllager funktioniert, wie es aufgebaut ist und wie es sich an neue logistische Herausforderungen angepasst hat. Nicht umsonst haben sich viele Unternehmen für automatische Lösungen entschieden, um ein Lager bei einer Umgebungstemperatur von bis zu -30 ºC zu betreiben.
Was ist ein Kühllager?
Bei einem Kühllager handelt es sich um eine Anlage für die Lagerung, Beschaffung, Zubereitung und den Versand von Produkten bei niedriger Temperatur. Diese Art von Anlagen umfasst für ihren Betrieb verschiedene Lagersysteme, Handhabungsgeräte sowie andere Elemente wie Fördervorrichtungen, Reinräume, SAS-Türen (Security Airlock System) usw.
Kühllager können anhand ihrer Lagersysteme (automatisch oder manuell) oder anhand ihrer Struktur (selbsttragend oder nicht) klassifiziert werden. Die gebräuchlichste Klassifizierung hängt jedoch von der in der Anlage vorhandenen Temperaturregelung ab, bei der unterschieden wird zwischen:
- Kühllagern: Diese Lager weisen eine kontrollierte Temperatur zwischen 0 und 10 ºC auf. Sie werden im Lebensmittelbereich (Milchprodukte, Wurstwaren u. a.), in der Pharmaindustrie oder im klinischen Bereich eingesetzt.
- Gefrierlagern: In diesen Lagern wird eine kontrollierte Temperatur von -30 ºC bis 0 ºC aufrechterhalten. Sie sind besonders in der Industrie für Tiefkühlkost üblich.
Es ist zu berücksichtigen, dass diese konstante Temperaturregelung, nicht nur während der Lagerung, sondern auch während der Annahme, der Zusammenstellung und des Versands von Aufträgen einen erheblichen Anstieg des Energieaufwands für die Anlage bedeutet, wodurch die logistischen Prozesse der einzelnen Produkte teurer werden.

Erschwerend kommt die Komplexität der manuellen Vorgänge hinzu: Temperaturen von bis zu -30°C können sich schädlich auf die Gesundheit der Bediener auswirken, wenn sie lange Zeit der Kälte ausgesetzt sind.
Da normalerweise verderbliche und pharmazeutische Produkte oder Lebensmittel gelagert werden, ist es außerdem üblich, dass die Anlage über ein System verfügt, das die Rückverfolgbarkeit der Waren in Echtzeit gewährleistet.
Wie ist ein Kühllager aufgebaut?
Das Hauptmerkmal eines Kühllagers ist die Temperaturregelung, um den Lebenszyklus der Waren zu verlängern. Aus diesem Grund muss die Lieferkette über Mechanismen verfügen, um die Kälte bei sämtlichen Vorgängen aufrechtzuerhalten. Zum Beispiel ist ein Kühlhaus mit der neuesten Technologie nutzlos, wenn die Laderampen keine Temperaturregelung ermöglichen.
Die Gestaltung eines Kühlhauses muss sich nach den jeweiligen Anforderungen des Unternehmens richten. Dazu gehören:
- Art der zu lagernden Waren.
- Kapazität bei der Warenannahme und beim Warenversand.
- Laderampen und temporäre Puffer
- Das allgemeine Layout des Lagers.
- Anzahl der täglich zu versendenden Bestellungen.
- Verwendete Lager- und Regalsysteme.
- Arten von Ladeeinheiten.
- Automatisierungsgrad des Lagers.
Alle Kühlanlagen müssen über manuelle oder automatische Lagersysteme verfügen, die speziell an die niedrigen Temperaturen angepasst sind. Neben den Regalen muss auch die Struktur des Lagers dafür geeignet sein, die Kälte in den Kammern aufrechtzuerhalten. Aus diesem Grund entscheiden sich viele Unternehmen für selbsttragende Lager (Hochregallager), bei denen die Regale das Tragwerk des Lagers bilden und eine Optimierung der Lagerkapazität ermöglichen.
Diese Lager müssen darüber hinaus mit Kühlraumtüren ausgestattet sein, die für die Betriebstemperatur der Anlage geeignet sind. In den meisten Fällen sind diese Türen Teil eines SAS (Security Airlock System), also eines Systems, das aus einer Vorkammer mit zwei Schnelllauftüren besteht, die niemals gleichzeitig geöffnet sind, wodurch plötzliche Temperaturschwankungen im Inneren des Kühllagers verhindert werden.
Lager, die bei kontrollierter Temperatur betrieben werden, benötigen außerdem ein Plenum bzw. einen Zwischenraum im oberen Teil des Lagers, Rohre für die Luftzirkulation, Verdampfer und einen isolierten Durchgang für die Wartung dieser Vorrichtungen.
Die Handhabungsgeräte können sowohl manuell als auch automatisch betrieben werden. Werden Gabelstapler eingesetzt, so müssen diese in einer geschlossenen Anlage unbedingt elektrisch betrieben werden.
Automatische Kühllager
Der Zweck eines automatischen Kühllagers besteht darin, die Prozesse zu beschleunigen und die Sicherheit sowohl der Bediener als auch der Waren zu erhöhen. Um ein Lager zu automatisieren, müssen automatische Handhabungsgeräte wie Regalbediengeräte für Paletten oder Behälter (Miniloads) installiert werden. Diese Lagersysteme werden in der Regel von Fördervorrichtungen beschickt, die den Warenfluss beschleunigen und sicherstellen, dass die Waren bei diesen ungünstigen Umgebungsbedingungen nicht von Bedienern bewegt werden müssen.
Darüber hinaus kann in Verbindung mit einem Regalbediengerät auch ein Pallet Shuttle eingesetzt werden, um die Waren in den Regalen noch weiter zu verdichten. In Lagern mit geringerem Auftragsvolumen wird jedoch empfohlen, das Pallet Shuttle in Verbindung mit Gabelstaplern zu verwenden.
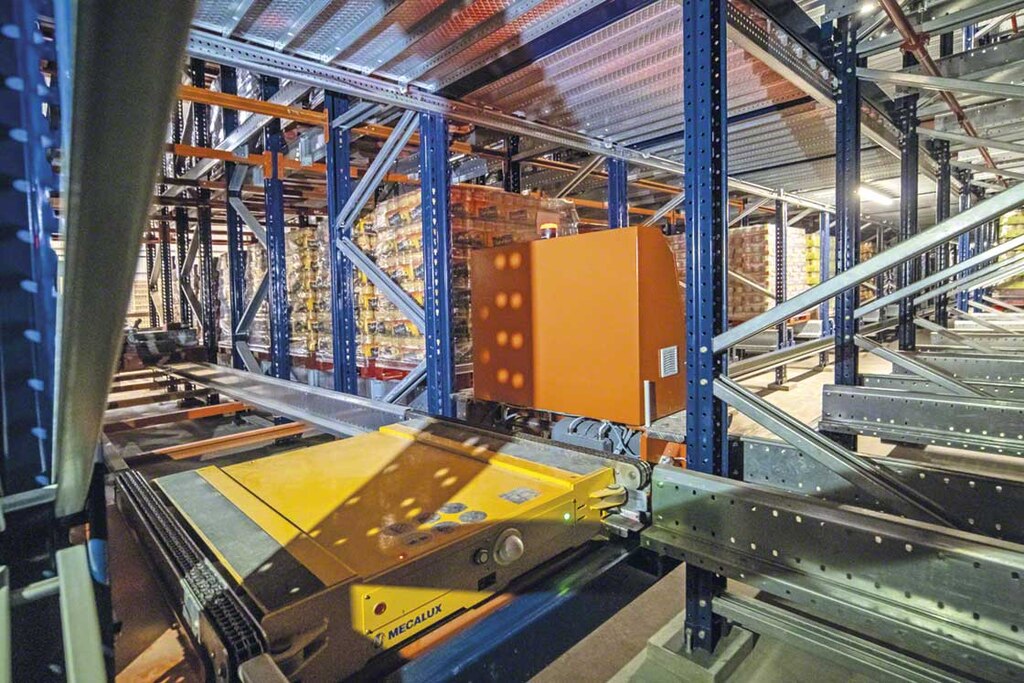
Soweit wurden Lösungen für die Lagerung der Waren beschrieben, es gibt aber auch Lösungen für die Automatisierung der Auftragszusammenstellung. Um die Bediener nicht der Kälte auszusetzen und gleichzeitig eine maximale Produktivität bei der Auftragszusammenstellung zu gewährleisten, sind Werkzeuge wie Roboterarme ideal. Dies ist beispielsweise der Fall bei der Lösung, die Mecalux im Lager des Logistikunternehmens Havi Logistics implementiert hat.
All diese automatisierten Elemente könnten ohne eine Palettenkontrollstation, die sicherstellt, dass jedes in das Lager eingehende Packstück die erforderlichen Anforderungen erfüllt, nicht sicher und effizient arbeiten. Ihre Aufgabe besteht unter anderem darin, das Gewicht der Ladung, die Umreifung und den Zustand der Palette zu überprüfen.
Vorteile der Automatisierung eines Kühllagers
Die Implementierung von automatischen Lagersystemen und Handhabungsgeräten bietet für Unternehmen mit Kühllagern folgende Vorteile:
- Höhere Produktivität: Nur die Automatisierung garantiert bei Tiefkühltemperaturen eine hohe Frequenz der Ein- und Ausgangszyklen, da diese Temperaturen bei einer zu langen Aussetzung der Gesundheit der Bediener schaden könnten.
- Effizientere Kommissionierung: Durch die Implementierung von automatischen oder halbautomatischen Kommissioniersystemen wie Voice-Picking oder Pick-to-Light-Systemen wird die Zeit, die sich die Bediener im Kühllager aufhalten, verkürzt, die Kommissionierwege werden optimiert und eine effizientere Auftragszusammenstellung ermöglicht.
- Erhöhung der Sicherheit und Hygiene: Automatische Kühllager gewährleisten die Sicherheit sowohl der Bediener, da diese nicht extremen Umweltbedingungen ausgesetzt sind, als auch der Produkte, indem sie Fehler bei der Verwaltung reduzieren. Darüber hinaus stellt die Automatisierung die Hygiene in sämtlichen Logistikprozessen sicher, was in Sektoren wie der Lebensmittel- und Pharmaindustrie ein Schlüsselfaktor ist.
- Einsparung von Logistikkosten: Energie ist das kostbarste Gut in Kühllagern. Automatisierte Lösungen optimieren die Lagerkapazität, sodass der Energieverbrauch pro Palette geringer ist.
- Optimierung der Lagerkapazität: Lösungen wie das Pallet Shuttle ermöglichen die Verdichtung des Lagerraums, da im Lager weniger Gänge vorhanden sind.
Aufgrund der oben genannten Vorteile und da die Kunden immer schnellere Lieferungen erwarten, ist eine Automatisierung unerlässlich, um die Frequenz der kombinierten Ein- und Ausgangszyklen im Lager zu erhöhen und insbesondere um den Nutzen für das Unternehmen zu maximieren.
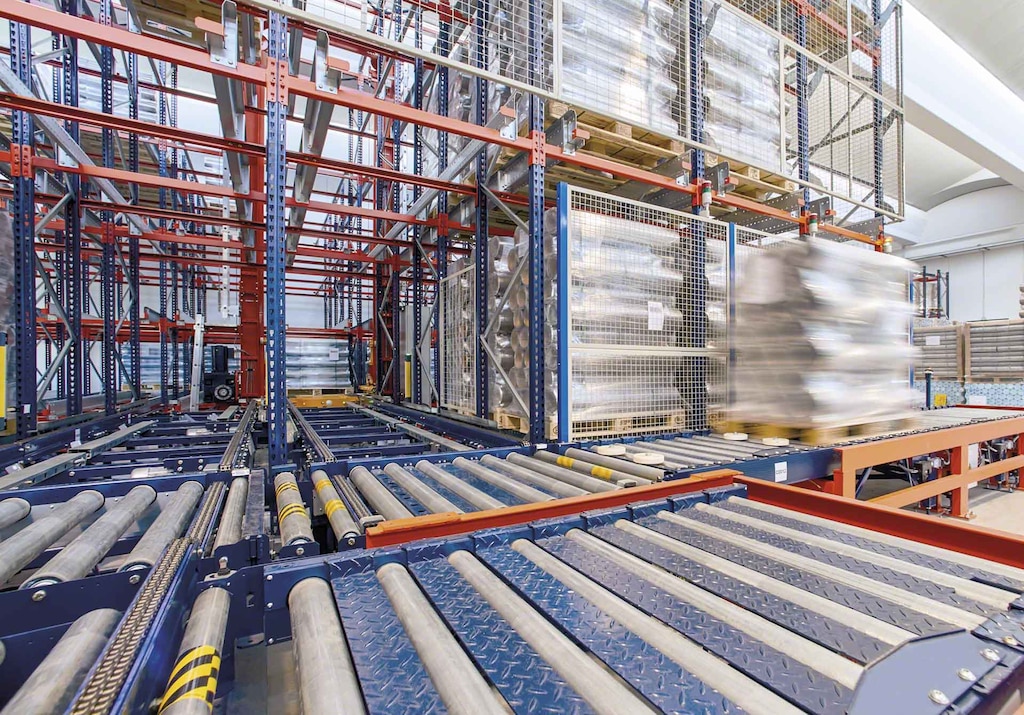
Zwei Beispiele für Unternehmen, die sich für die Automatisierung ihrer Kühllager entschieden haben, sind:
- Congelados Navarra: Für Congelados Navarra, einem der europäischen Marktführer in der Herstellung und dem Verkauf von Tiefkühlgemüse, hat Mecalux ein Logistikzentrum errichtet. Mit dieser Anlage, die mit der neuesten Technologie im Bereich der Kühllagerung ausgestattet ist, verfügt das Unternehmen nun über eine Kapazität von fast 150.000 Paletten.
- La Piamontesa: Das selbsttragende Kühllager dieses Unternehmens hat sich zu einer Referenz für automatische Kühllagersysteme in Argentinien entwickelt. Der Wursthersteller setzt das automatische Pallet-Shuttle-System ein, um die Produktivität seiner Kühlkammern zu erhöhen und den Energieverbrauch zu senken.
Effizienz und Optimierung für Kühllager
Neue Verbrauchertrends und der immer häufigere Verzehr von Tiefkühlkost haben das Interesse an Kühllagern gefördert. Es ist jedoch zu berücksichtigen, dass die Kühllagerung eine umfassende Kontrolle der Produktsicherheit in allen Prozessen voraussetzt, um die Rückverfolgbarkeit in Echtzeit bei sämtlichen Abläufen im Lager zu gewährleisten.
Hinzu kommen die hohen Logistikkosten, die mit dem Betrieb eines Kühllagers verbunden sind. Unternehmen, die diese Logistikzentren betreiben, müssen Lösungen finden, die die Effizienz und Optimierung der Lagerfläche gewährleisten.
Wir bei Mecalux verfügen über mehr als 50 Jahre Erfahrung in der Beratung und Implementierung von manuellen und automatischen Lösungen in Kühllagern. Kontaktieren Sie uns, und wir beraten Sie über die beste Lösung zur Erhöhung der Produktivität Ihrer Anlage.