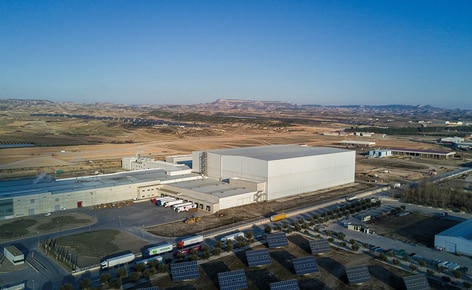
Mecalux begleitet Congelados de Navarra bei seinem stetigen Wachstum
Congelados de Navarra hat eine Kapazität für 146.000 Paletten in drei automatisierten Gefrierlagern
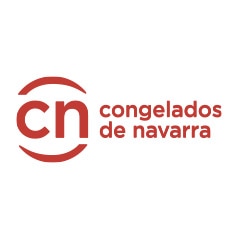
Congelados de Navarra wurde 1998 gegründet und ist eine der jüngsten Tiefkühlkostfirmen Europas. Durch ihre entschlossene Ausrichtung auf Technologie und Innovation bei allen Produktionsprozessen hat es die Firma geschafft, europaweit zu den 10 führenden Spezialisten für Tiefkühlgemüse zu gehören. Von Anfang an hat Mecalux diese Firma bei ihren Erweiterungsprojekten begleitet, wobei es die effizientesten Logistiklösungen zur Erfüllung ihrer Bedürfnisse entworfen und umgesetzt hat.
Eine Erfolgsgeschichte
Congelados de Navarra ist ein klares Beispiel für Anstrengung und Erfolg, durchdrungen von einem großen Unternehmergeist. Seine Geschichte begann 1998, als Benito Jiménez die Firma gründete und mit dem Bau des Produktionszentrums in Arguedas (Navarra) begann.
Anfangs bestand das Gebäude aus einem Tiefkühllager mit Kompakt-Palettenregalanlagen (Drive-in), seine Kapazität reichte jedoch nicht aus, um den wachsenden Umsatz zu bewältigen. Das Unternehmen sah sich gezwungen, eine strategische Investition zur Erweiterung vorzunehmen, und war sich von Anfang an der Bedeutung und Notwendigkeit der Automatisierung bewusst, um die Wirtschaftlichkeit aller seiner Prozesse zu erzielen und ihre Produktivität zu maximieren.
Derzeit verfügt der Standort in Arguedas über zwei vollautomatische Tiefkühllager , die 12.700 Paletten aufnehmen können.
Das Unternehmen hat bei der Optimierung der Leistung seines Standorts stets die Vorteile der Automatisierung genutzt.
Daher konnte es ein ständiges Wachstum verzeichnen und hat wichtige Ziele erreicht, die ihm Ansehen verliehen haben, beispielsweise war es 2004 der größte Brokkoliproduzent Europas.
Angesichts der Wachstumsaussichten weihte Congelados de Navarra 2008 sein zweites Produktionszentrum in Fustiñana ein (nur 24 km von der ersten Fabrik entfernt).
Dieses Zentrum wurde ständig erweitert und an die Erfordernisse der Firma angepasst. Derzeit verfügt es über zwei automatische Lager in selbsttragender Bauweise mit einer Gesamtkapazität von 63.000 Paletten. Ein weiteres Lager ist im Bau, welches eine Kapazität von 83.000 Paletten haben wird.
2012 eröffnete das Unternehmen sein erstes Büro in Frankreich, das den Ausgangspunkt seiner Expansion auf internationalem Niveau darstellte. Heute verfügt es ebenfalls über Niederlassungen in Großbritannien und den Vereinigten Staaten. Es exportiert 70 % seiner Produktion und hat ein dichtes Netz an Vertriebsfirmen und Importeuren geschaffen, die es beim weltweiten Vertrieb seiner Produkte unterstützen.
Mecalux und Congelados de Navarra
Die Zusammenarbeit zwischen beiden Unternehmen begann 1998, schon mit den Anfängen von Congelados de Navarra.
Mit der Beratung von Mecalux hat das Unternehmen neue Ziele und Projekte geplant und entwickelt, die seine Logistik verbessert haben. Im Laufe der Zeit wurden unter anderem die folgenden Projekte verwirklicht:
Arguedas
2000 beauftragte Congelados de Navarra Mecalux mit der Konstruktion des ersten automatischen Tiefkühllagers in seinem Produktionszentrum in Arguedas. Dort wurde das Kompaktsystem Pallet Shuttle mit Regalbediengerät mit einer Lagerkapazität für 3800 Paletten installiert.
2004 wurde das zweite automatische Tiefkühllager, in selbsttragender Bauweise, in Betrieb genommen. Es ist 33 m hoch und besteht aus drei Gängen mit Regalanlagen doppelter Tiefe, die auf beiden Seiten angeordnet sind und eine Lagerkapazität von 8.900 Paletten bieten, das Dreifache der ursprünglichen Kapazität.
Fustiñana
Congelados de Navarra nahm 2008 ein neues Produktionszentrum in Fustiñana in Betrieb, um das erwartete Wachstumstempo aufrecht zu erhalten und seine Kunden schnell bedienen zu können.
Tatsächlich ist dieses ehrgeizige Projekt durch eine ständige Erweiterung und ein kontinuierliches Wachstum gekennzeichnet:
- Phase 1
Mecalux baute ein 36 m hohes automatisches, selbsttragendes Tiefkühllager, in dem ständig eine Temperatur von -21 ºC herrscht. Es besteht aus sechs Gängen mit Regalanlagen doppelter Tiefe, die eine Lagerkapazität für 27.000 Paletten haben.
In diesem Zentrum erfolgt der gesamte interne Transport zwischen den verschiedenen Produktionsbereichen und den Lagern vollautomatisch, mit einem Rollenförderkreislauf, Verfahrwagen, Hubsystemen und Elektroführungen. - Phase 2
Von 2010 bis 2011 wurde eine neues Lager mit ähnlichen Merkmalen wie das vorherige gebaut, welches an dieses angrenzt und mit ihm verbunden ist. Es besitzt einer Kapazität für weitere 36.000 Paletten, die auf acht Gänge verteilt sind. - Phase 3
2015 erweiterte Congelados de Navarra den Abfüll- und Mischbereich. Bei der Installation aller internen Fördermittel, die diese Bereiche mit den restlichen Produktionsbereichen, einschließlich der Lager, verbinden, vertraute man wiederum auf Mecalux. - Phase 4
Ein Jahr später bat Congelados de Navarra Mecalux um seine Mitarbeit, um eine großzügige Lösung für den möglichen Produktionszuwachs zu finden und auf diese Weise das Wachstum zu verstärken, sowohl auf Produktionsebene als auch in Bezug auf die Lagerkapazität.
Man entschied sich für den Bau eines weiteren Lagers als Ergänzung der beiden vorhandenen, das vollständig für Halbfertigprodukte bestimmt sein sollte. Nach seiner Fertigstellung wird es mit den bereits vorhandenen Transportkreisläufen verbunden sein, um die Ware in beiden Richtungen zu transportieren. Das Lager wird 43 m hoch sein und über eine Lagerkapazität für 83.000 Paletten verfügen - eine Konstruktion mit enormen Abmessungen, die sehr ungewöhnlich für ein derartiges Tiefkühllager ist. Es wird mit dem automatischen Kompaktsystem Pallet Shuttle mit Verfahrwagen ausgerüstet, wodurch eine große Zahl an Bewegungen möglich ist.
Effiziente Installation in Fustiñana
Am Standort Fustiñana wird der größte Teil der Produktion von Congelados de Navarra hergestellt. Die Nahrungsmittel müssen mehrere Prozesse durchlaufen (die meisten davon automatisch), um die maximale Qualität zu gewährleisten und sicherzustellen, dass eine gute Textur, Nährwert und Geschmack erhalten bleiben.
Ausgang aus der Produktion
Die Installation von Mecalux beginnt, wenn die Ware den Gefriertunnel durchlaufen hat. Direkt unter den Sortierlinien wurden Kanäle mit Rollenförderern montiert. Die leeren Oktabins (große Behälter aus Pappe und Kunststoff für Schüttgut) werden zu den Trichtern transportiert und mit den Produkten befüllt.
Anschließend transportiert ein Verfahrwagen die Paletten zu den Hubsystemen, die sie in die obere Ebene bringen. Dort verschließen die automatischen Packmaschinen die Oktabins, um das Produkt zu schützen. Nachdem ihr Zustand überprüft wurde, gelangen sie in den Elektroführungskreislauf, der sie in die Tiefkühllager (oder in die restlichen Produktionsbereiche bringt).
Das Design des Elektroführungskreislaufs macht es möglich, die erforderlichen Wagen an jedem Punkt durch dynamische Zuweisung bereitzustellen. Außerdem gibt es Abkürzungen, damit die Wagen nicht den gesamten Kreislauf durchlaufen müssen.
Eingang zum Tiefkühllager
Bevor die Paletten in das Lager gelangen, durchlaufen sie ein SSS (Sicherheitsschleusensystem). Dies ist eine Vorkammer, die aus zwei Schnelltüren besteht - eine, die in das Tiefkühllager führt und eine nach außen -, die nie gleichzeitig geöffnet sind. Dieses System wird genutzt, um jähe Temperaturveränderungen, Kälteverluste und Kondensation zu vermeiden. Für den Ausgang der für den Verarbeitungsbereich bestimmten Paletten wurde ebenfalls ein SSS eingerichtet.
Die Lager besitzen zwei Verbindungsebenen und auf jeder gibt es zwei Förderkreisläufe, einer für die Eingänge und der andere für die Ausgänge.
Die obere Ebene ist für den Wareneingang aus der Produktion und den Ausgang der Paletten in den Verarbeitungsbereich (Abfüllen und Mischen) bestimmt.
Auf der unteren Ebene findet der Eingang der Produkte von außerhalb des Lagers statt. Dort befindet sich ebenfalls der Versandbereich.
Eigenschaften der Lager
Die beiden Lager sind zusammen 140 m lang, 103 m breit und 35 m hoch.
Sie bestehen aus insgesamt 14 Gängen mit Regalanlagen doppelter Tiefe auf beiden Seiten, mit denen eine Gesamt-Lagerkapazität von 63.000 Paletten erreicht wird.
Die Bauweise ist selbsttragend, d. h., die Regalanlage trägt ihr Eigengewicht, das Gewicht der Seitenwände und des Daches sowie das Gewicht der Ware. Im oberen Bereich der Regalanlage sind die Dachbinder zu sehen, auf denen sich die Kühlaggregate befinden. Auf diese Weise wird ein ständiger Luftstrom und eine gleichmäßige Verteilung der Temperatur in der gesamten Anlage erreicht.
In jedem Gang befördern die Zweimast-Regalbediengeräte die Paletten zwischen den Eingangs- und Ausgangsförderern und der Regalanlage hin und her. Die Lagerpositionen werden ihnen von der Lagerverwaltungssoftware (LVS) Easy WMS von Mecalux gemäß den vorher festgelegten Regeln zugewiesen.
Im oberen Teil des Tiefkühllagers wurden Laufgänge und Plattformen angelegt, die für Instandhaltungsarbeiten an den Kühlaggregaten und den Regalbediengeräten bestimmt sind. Der Zugang zu ihnen befindet sich außerhalb des Lagers.
Untere Ebene der Lager
Der Ausgang der Produkte zum Versand findet auf der unteren Ebene der Lager statt. Ein Förderkreislauf verbindet die Lagergänge mit den Ausgangstüren zu den Vorkammern, in denen die Paletten in Wartestellung verbleiben, bis sie in die Transportfahrzeuge verteilt werden.
In der Vorkammer (mit geringer Höhe und geregelter Temperatur) wird die Ware, die zur gleichen Bestellung oder Route gehört, gruppiert, um die spätere Beladung der Transportlastwagen zu beschleunigen. In diesem Raum können 500 versandbereite Paletten aufbewahrt werden.
Es gibt drei SSS, die die Vorkammer mit den Laderampen verbinden. Nachdem die Paletten diese durchlaufen haben, sind die Lagerarbeiter dafür verantwortlich, sie in den Laderaum des Transportfahrzeugs zu befördern.
Im gleichen Bereich befinden sich die Eingangsstationen für die Produkte, die von außerhalb des Herstellungsbetriebs kommen. Paletten mit unzureichender Qualität werden auf eine Trägerpalette gesetzt, die zwei verschiedene Abmessungen haben kann:800 x 1200 mm oder 1000 x 1.200 mm.
Abfüll- und Mischbereich
Die Produkte, die für den Verarbeitungsbereich bestimmt sind, verlassen das Lager über die obere Ebene und werden von den Elektroführungen abgeholt.
Der Verarbeitungsbereich liegt höher als der Förderkreislauf der Elektroführungen. Daher wurden Hubsysteme installiert, die die Ware auf die obere Ebene befördern. Dort befinden sich die Trichter für das Abfüllen und Mischen sowie ein Förderkreislauf, der die Paletten zur entsprechenden Station bringt.
Die Paletten, die diese Prozesse hinterlassen, werden mit dem Hubsystem nach unten gebracht und mit den Elektroführungen an ihr neues Ziel befördert.
Transport der Oktabins zur Produktion
Der Transport von leeren Oktabins in den Produktionsbereich ist unerlässlich für die korrekte Funktionsweise dieses Standorts und erfolgt ebenfalls automatisch.
Die Oktabins werden in einem speziellen Bereich vorbereitet:Sie werden auf Paletten gesetzt, mit einer großen Tüte ausgekleidet, die den Kontakt mit dem Tiefkühlprodukt und der Pappe verhindert, und schließlich mit einem RFID-Code versehen.
Zwei Hubsysteme bringen die Oktabins zur Förderebene und die Elektroführungen transportieren sie automatisch zum vorgesehenen Ort.
Elektroführungen
Die Elektroführungen sind die Nabelschnur dieser Installation und für die internen Bewegungen zwischen allen Bereichen des Produktionszentrums verantwortlich.
Die Schienen hängen an der Decke und von ihnen erhalten die Wagen den Strom und erkennen ihre Position innerhalb des Kreislaufs. Die Umleitungen sind sehr wichtig:Es gibt Abkürzungen, Instandhaltungsbereiche und Wagen in Wartestellung.
Die Elektroführungen sind sehr schnell und sorgen für einen ständigen Warenfluss. Sie sind ideal für Nahrungsmittelhersteller wie Congelados de Navarra, da es keine Hindernisse am Boden gibt, was die Reinigungsarbeiten erleichtert.
Easy WMS von Mecalux, das Gehirn des ganzen Systems
Optimale Logistikverwaltung
Die von Mecalux entwickelte Software verwaltet und steuert alle Prozesse, die in einer Einrichtung stattfinden, einschließlich des Eingangs der Waren aus der Produktion und von außerhalb, der Zuweisung der Lagerpositionen, der Bestandskontrolle, der Lagerung, der Entnahme, des Transports der Paletten in die Verarbeitungsbereiche, der Rückkehr in das Lager usw.
Easy WMS von Mecalux liefert ständig leere Oktabins für die fortlaufende Abfüllung der aus der Produktion eintreffenden Ware.
Die Platzierung der Ware in den Lagerpositionen erfolgt nach Regeln und Algorithmen, die die Eigenschaften der Produkte, ihren Verbrauch und ihre Rotation berücksichtigen. Die Regeln sind in Easy WMS von Mecalux konfiguriert, um die Bestände in den 14 Gängen des Lagers zu klassifizieren. Beispielsweise wird die lose Ware in Oktabins so nah wie möglich am Abfüll- und Mischbereich gelagert, verarbeitete Produkte werden hingegen in der Nähe des Versandbereichs gelagert.
Das ERP des Unternehmens, JD Edwards von Oracle, fordert die lose Ware für den Abfüllbereich an. Die LVS von Mecalux berechnet die notwendige Anzahl an Oktabins und schickt sie unter Beachtung einer festgelegten Reihenfolge an ihr Ziel. Die Bestellungen für den Mischbereich werden von der LVS genauso behandelt wie die des Abfüllbereichs.
Der Versand erfolgt mithilfe von LKW. Die LVS erstellt Aufträge, um die Bestellungen aus ihren Lagerpositionen zu entnehmen, und sorgt für ihre Lagerung in den Vorkammern, wo sie auf ihren Transport zu den Laderampen warten. Sobald der LKW an der Laderampe andockt, um beladen zu werden, werden die Paletten automatisch zu den Ausgangsstationen bewegt und Easy WMS zeigt dem Lagerarbeiter auf einem Bildschirm an, zu welcher Rampe er jede Ladung bringen muss.
Kommunikationsdreieck
Für den ordnungsgemäßen Ablauf in diesem Lager steht Easy WMS von Mecalux in ständiger Verbindung mit den beiden anderen Verwaltungssystemen, die an diesem Projekt beteiligt sind: dem Unternehmensverwaltungssystem ERP von Congelados de Navarra und gleichzeitig mit dem Produktionsleitsystem (Manufacturing Execution System; MES).
Das MES gibt Easy WMS in Echtzeit die Wareneingänge an jeder Produktionslinie an. Daneben fordert es die losen Produkte an, die an diesen Bereich geschickt werden müssen.
Das ERP kündigt den Eingang von Paletten aus anderen Logistikzentren von Congelados de Navarra an, die für das Lager bestimmt sind, und gibt Bestellungen für lose Ware zur Abfüllung oder Mischung auf.
Galileo, das Herzstück der Installation
Ein automatisches Lager mit der Komplexität wie bei Congelados de Navarra benötigt Lösungen, die seine Verwaltung vereinfachen und optimieren. In dieser Hinsicht funktioniert die Steuerungssoftware Galileo von Mecalux als allgemeines Instrument zur Koordinierung der Einrichtung, das die Bewegungen der elektromechanischen Anlagen für Transport und Lagerung der Ware ausführt.
Galileo ist für die Handhabung der Maschinen (Fördervorrichtungen, Regalbediengeräte, Elektroführungen, Hubsysteme usw.) verantwortlich, steuert die Hardwarekomponenten (Scanner, RFID-Lesegeräte, Umrichter usw.) und erfasst mögliche Probleme oder Zwischenfälle sowie die gesamte Kommunikation mit der Lagerverwaltungssoftware (LVS). Kurz gesagt, es empfängt die Befehle von der LVS, sendet die entsprechenden Signale an die Maschinen und sorgt für die automatische Bewegung der Oktabins.
Daneben liefert das SCADA-System in Echtzeit alle Informationen über jede Maschine, Störungen, Transportbewegungen usw. im Lager, ohne dass eine spezielle Hardware zur Visualisierung notwendig ist.
Auf die Zukunft vorbereitet
Das Produktionszentrum in Fustiñana ist auf Wachstum vorbereitet und berücksichtigt die Möglichkeit, in Zukunft weitere Tiefkühllager zu errichten, abhängig von den Anforderungen des Marktes und den Zielen des Unternehmens.
Die Software von Mecalux wird das Unternehmen jederzeit begleiten, da sie sich an Veränderungen und die jeweilige Zunahme der Produktion anpasst. Das System ist skalierbar, d. h., es ist in der Lage, den Umfang der Ressourcen je nach den Anforderungen des Standorts zu erhöhen oder zu verringern. Daher wird Easy WMS ein Modul für den Einsatz des automatischen Pallet-Shuttle-Systems mit Verfahrwagen enthalten, um die ordnungsgemäße Funktion der neuen Gefrierkammer zu gewährleisten.
Zukunftsaussichten
Benito Jiménez, Unternehmer und Gründer von Congelados de Navarra, entschloss sich dazu, in allen automatischen Prozessen automatische Systeme einzubeziehen, von der Produktion bis zur Lagerung, einschließlich des internen Transports. Dies dient letztendlich dazu, die Leistung seiner Standorte zu maximieren und das Wachstumstempo des Unternehmens zu stärken.
Die Automatisierung aller Lagerbereiche der Standorte Arguedas und Fustiñana war ein großer Fortschritt für Congelados de Navarra, da die Lagerkapazität optimiert und der Umfang menschlicher Eingriffe möglichst gering gehalten wird.
Schon von Anfang an hat Mecalux Congelados de Navarra bei der Umsetzung seiner Erweiterungsprojekte beraten. Mecalux hat all sein Wissen und seine Erfahrungen eingesetzt, um individuelle Lösungen zu finden, die auf effiziente Weise die vorhandenen logistischen Anforderungen erfüllen können. Das Ergebnis dieser engen Beziehungen, das automatische Produktionszentrum in Fustiñana, ist eines der modernsten und technisch fortschrittlichsten Zentren auf dem europäischen Markt und gilt als Referenz auf Weltniveau.
Galerie
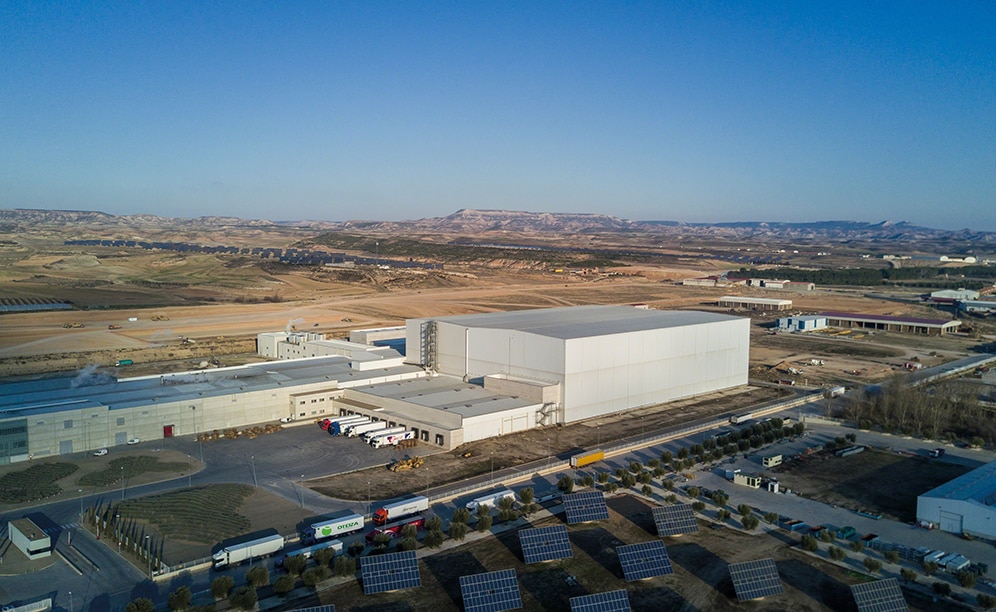
Die beiden in den Phasen 1 und 2 errichteten Lager haben eine Kapazität von insgesamt 63.000 Paletten
Fragen Sie einen Experten