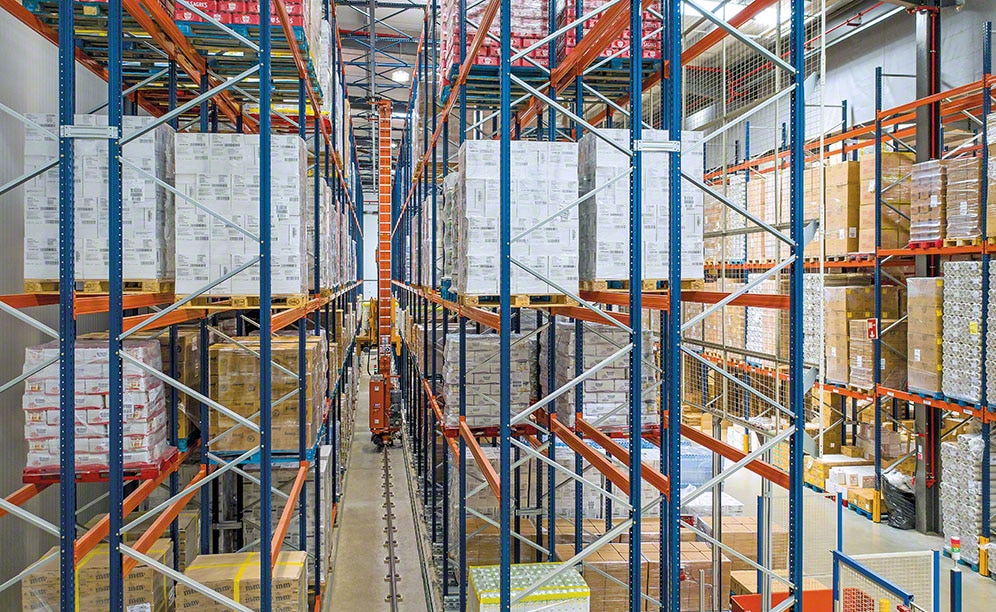
Automatisiertes Tiefkühllager für Lebensmittel für HAVI in Portugal
Technologie zur Verbesserung von Produktivität, Effizienz und Energieverbrauch
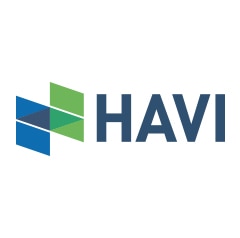
HAVI hat in Portugal ein modernes Logistikzentrum mit fortschrittlicher Technologie eingeweiht, das seine Kunden aus der dortigen Lebensmittelbranche beliefert. Das Zentrum ist in drei Bereiche mit verschiedenen Temperaturen unterteilt: Umgebungs-, Kühl- und Gefriertemperatur bei -20 °C. Alle Lagersysteme wurden von Mecalux geliefert: zwei automatisierte Lager, Palettenregale, Einfahrregale und Regale mit Pallet Shuttle. Außerdem wurde das Lagerverwaltungssystem (LVS) Easy WMS implementiert, das mit dem LVS von HAVI verbunden ist, um den Bestand zu kontrollieren und die Sequenzierung beim Warenversand zu gewährleisten.
Informationen zu HAVI
HAVI ist ein multinationales Unternehmen, das sich der Innovation und Optimierung der Lieferkette von führenden Marken verschrieben hat. Das Leistungsspektrum umfasst Analyse, Logistik, Supply Chain Management und Verpackung. HAVI wurde 1974 gegründet und ist in mehr als hundert Ländern vertreten. In Portugal gehören u. a. die beliebte Fast-Food-Kette McDonald’s und die Marke Portugalia zu seinen wichtigsten Kunden im Lebensmittelbereich.
Eine der Stärken von HAVI ist die betriebliche Effektivität und Exzellenz, sowohl in Bezug auf die Dienstleistungen als auch auf Sicherheit und Qualität. Das Unternehmen ist ein Vorreiter bei der Versorgung von Restaurants mit den erforderlichen Produkten genau zum richtigen Zeitpunkt. Um dies zu erreichen, verfügen seine Logistikzentren über agile und effiziente Abläufe, die eine umfassende Kontrolle der Waren unter Einhaltung der geeigneten Lagerbedingungen sicherstellen.
Ein modernes, effizientes und nachhaltiges Lager
Die technische Abteilung von Mecalux hat beim Entwurf, Bau und bei der Inbetriebnahme eines modernen Logistikzentrums in Vila Nova da Rainha (Portugal) erneut mit HAVI zusammengearbeitet. Von diesem Vertriebszentrum aus werden Kunden aus der Gastronomie im gesamten Land beliefert. Die beiden multinationalen Unternehmen hatten bereits bei anderen Projekten zusammengearbeitet und bildeten dabei ein erfolgreiches Team. So hatte Mecalux beispielsweise ein automatisiertes Lager für HAVI in Moskau (Russland) montiert und das Zentrum des Unternehmens in Lodi (Italien) mit Movirack-Verschieberegalen ausgestattet.
Das neue Zentrum von HAVI in Portugal mit einer Gesamtfläche von 10.000 m² wurde in drei Bereiche unterteilt, um alle Waren bei der richtigen Temperatur zu lagern: in Tiefkühlung, Kühlung und bei Umgebungstemperatur. Jeder Bereich verfügt über eine spezifische Anordnung, die auf die logistischen Anforderungen des Unternehmens abgestimmt ist. Aus diesem Grund hat Mecalux verschiedene automatisierte und konventionelle Lager- und Kommissionierlösungen implementiert. Der gemeinsame Nenner bei allen ist die Betriebsbereitschaft und Zuverlässigkeit bei der Bestandsverwaltung sowie die Agilität, für die diese Systeme bei der Lagerung und Auftragszusammenstellung sorgen. In Bezug auf die Technologie ist dieses Zentrum ebenfalls ein Vorreiter bei der Automatisierung von Logistikprozessen bei -20 °C.
In allen drei Bereichen des Zentrums sind Palettenregale vorhanden. Sie wurden wegen ihrer Anpassungsfähigkeit an jede Art von Last, Gewicht und Volumen ausgewählt. Der direkte Zugriff erleichtert zudem die Handhabung der Waren. Auf den unteren Ebenen wird mithilfe von Handscannern direkt von den Paletten kommissioniert. Auf den oberen Ebenen der Regale lagert dagegen die Reserveware.
Beim Entwurf aller Lagerlösungen lag das Hauptaugenmerk von Mecalux stets auf der Sicherheit, sowohl der Mitarbeiter als auch der Waren. Es ist äußerst wichtig, die Kühlkette der Lebensmittel zu bewahren und zu vermeiden, dass sie unterbrochen wird. Aus diesem Grund sind die Zugänge zum Kühl- und Tiefkühllager isoliert, um plötzliche Temperaturschwankungen, Kälteverluste und die Entstehung von Kondensation zu verhindern. Die Automatisierung hat ebenfalls zu mehr Sicherheit beigetragen, da 77 % der Palettenbewegungen vollständig automatisiert sind.
Andererseits wurde auch die Ergonomie bei der Handhabung der Produkte verbessert und körperliche Belastungen wurden reduziert. Dabei ist besonders hervorzuheben, dass die Mitarbeiter weniger Zeit in kalten Umgebungen verbringen müssen. Dies verbessert nicht nur die Arbeitsqualität, sondern verringert auch den Energieverbrauch um 10 %, da die Zugangstüren zur Kammer nicht so häufig geöffnet werden.
Vertreter von HAVI
„Wir können uns nun an Veränderungen unserer Geschäftsaktivität anpassen, die Haltbarkeitsdaten der Lebensmittel besser kontrollieren und sind effizienter bei der Auftragsabwicklung“.
Tiefkühllager
Das Tiefkühllager ist mit dem modernen, automatisierten Pallet-Shuttle-System ausgestattet, das von zwei Regalbediengeräten bedient und von Easy WMS verwaltet wird. Dort werden die Artikelarten mit dem höchsten Umsatz gelagert, wie Hamburger, Pommes Frites, Produkte aus Hähnchenfleisch usw. „Ein großer Teil der an Restaurants gelieferten Aufträge wird im Tiefkühllager zusammengestellt“, bestätigt ein Verantwortlicher von HAVI. Das Lager, in dem eine Temperatur von -20 °C herrscht, verfügt über zwei Gänge mit zwei Regalblöcken, die maximal sechs Paletten in der Tiefe aufnehmen können. Insgesamt bieten sie eine Lagerkapazität von mehr als 2.247 Paletten, das heißt 75 % mehr im Vergleich zu einem nicht automatisierten Lagersystem.
Das automatisierte Pallet-Shuttle-System optimiert den Lagerraum und reduziert das zu kühlende Volumen. Auf diese Weise maximiert es die Lagerkapazität und spart gleichzeitig Energie, die notwendig ist, um die Anlage auf Gefriertemperatur zu halten. „Unser Ziel bestand darin, die Effizienz in diesem Bereich und gleichzeitig die Arbeitsbedingungen der Mitarbeiter zu verbessern“, erläutert ein Vertreter von HAVI.
Der Betrieb des Lagers ist vollständig automatisiert: Es verfügt über zwei Zweimast-Regalbediengeräte, die die Ware zwischen den Ein- und Ausgängen des Lagers und den Lagerkanälen hin- und her befördern. Im Inneren der Kanäle führt das motorisierte Shuttle die Warenbewegungen aus. Alle Vorgänge werden von Easy WMS überwacht, das für die Kontrolle des Lagerbestands verantwortlich ist. Diese Software kommuniziert mit dem LVS von HAVI, um die vollständige Rückverfolgbarkeit der Waren, von ihrer Ankunft im Lager bis zur Auslieferung an den Kunden, zu gewährleisten.
Direkt neben dem Lager wurde ein Förderkreislauf eingerichtet, der die Ware mit einer konstanten Geschwindigkeit von 20 m/min nach dem Prinzip „Ware zum Mann“ in den Kommissionierbereich transportiert. „Mit dieser Methode der Auftragszusammenstellung konnten wir die Arbeitsbedingungen verbessern“, bemerkt einer der Verantwortlichen von HAVI. Die von Easy WMS sequenzierten Aufträge werden unabhängig voneinander oder gemeinsam an einem automatisierten und zwei manuellen Kommissionierplätzen zusammengestellt, je nach den Anforderungen des jeweiligen Auftrags. Zu diesem Zweck verbindet ein Shuttle-Car die drei Kommissionierplätze einerseits miteinander und andererseits mit dem Verpackungs- und Etikettierbereich.
Der automatisierte Kommissionierplatz verfügt über einen anthropomorphen Roboter, der komplette Schichten der Produkte mit dem höchsten Umschlag handhabt. Diese machen 40 % des gesamten Auftragsvolumens im Tiefkühllager aus. Der große Vorteil dieser Geräte liegt in der Schnelligkeit, mit der sie arbeiten, da sie mehrere Aufträge gleichzeitig zusammenstellen können. Die automatisierte Kommissionierung sorgt für Schnelligkeit und Einsparungen bei den Betriebskosten, insbesondere in Tiefkühllagern.
An den beiden manuellen Kommissionierplätzen wird die Ware automatisch angeliefert, entweder von den Fördervorrichtungen aus dem Lager oder vom Shuttle-Car, wenn sie zuvor vom antropomorphen Roboter gehandhabt wurde. In beiden Fällen ermöglicht das Prinzip „Ware zum Mann“, die Anzahl der Bewegungen zu reduzieren und die Auftragszusammenstellung zu beschleunigen. An allen Kommissionierplätzen, die mit PTL-Vorrichtungen (Put-to-Light-Vorrichtungen) ausgestattet sind, kann der Kommissionierer auf ergonomische Weise bis zu acht Aufträge gleichzeitig zusammenstellen, wodurch die Produktivität gesteigert und die Arbeitsqualität verbessert wird. Auf einem Monitor zeigt Easy WMS den Kommissionierern alle Aufgaben an, die sie durchführen müssen, um die Sequenzierung der Aufträge einzuhalten: welche Produkte zu entnehmen sind, zu welchem Auftrag sie gehören usw. Nach Abschluss der Aufgabe melden sie dies dem LVS, indem sie die PTL-Vorrichtung betätigen.
Anschließend holt das Shuttle-Car die fertigen Aufträge ab und transportiert sie zur Packmaschine und zum Etikettiergerät. Von dort werden sie mithilfe der Fördervorrichtungen in der festgelegten Reihenfolge in den Versandbereich transportiert. Dieser Bereich, in dem ebenfalls eine kontrollierte Temperatur herrscht, um die Kühlkette nicht zu unterbrechen, besteht aus acht schwerkraftgesteuerten Kanälen zur Ladevorbereitung, auf denen die Paletten klassifiziert und nach Auftrag oder Transportroute gruppiert werden. Die Einhaltung der Sequenzierung und Vorgruppierung der Aufträge in den Kanälen zur Ladevorbereitung trägt dazu bei, Zeit zu sparen und Fehler beim Verladen der Ware in die Lastwagen zu minimieren.
Im Tiefkühllager wurde ebenfalls ein Regalblock mit dem halbautomatisierten Pallet-Shuttle-System montiert, der eine Lagerkapazität von 237 Paletten aufweist. Hier wird vor allem Brot gelagert. Diese Lösung, die ebenfalls die Lagerfläche optimiert, verfügt über ein motorisiertes Shuttle, das die Paletten auf automatische Weise im Inneren der Lagerkanäle bewegt. Im Gegensatz zum automatisierten Lager setzen hier jedoch die Lagerarbeiter das Shuttle und die Ware mithilfe von Schubmaststaplern in den entsprechenden Kanal.
Kühlkammer
Neben den Palettenregalen hat Mecalux hier einen Block mit 9 m hohen Einfahrregalen mit einer Lagerkapazität von 1.996 Paletten montiert. Dies ist eine optimale Lösung für die Lagerung einheitlicher Produkte mit einer großen Anzahl von Paletten pro Artikelart, vor allem Tomaten, Fertigsalate usw.
Die Regale bestehen aus einer Reihe von Ladegassen mit vier Ebenen. Auf jeder Ebene befinden sich Stützschienen auf beiden Seiten, auf denen die Paletten platziert werden. Bei der Handhabung der Ware fahren die Lagerarbeiter mit Schubmaststaplern so in das Innere der Ladegassen hinein, dass sie die Ladung oberhalb der vorgesehenen Abstellebene transportieren.
Lager mit Umgebungstemperatur
In diesem Bereich, der für Produkte wie Ketchup, Mayonnaise, Spielzeug, Verpackungen und Flaschen mit Wasser und anderen Getränken vorgesehen ist, befindet sich ein automatisiertes Lager mit einer Lagerkapazität von 530 Paletten, das aus einem einzigen Gang mit 10,2 m hohen Regalen doppelter Tiefe auf beiden Seiten besteht. Ein Zweimast-Regalbediengerät transportiert die Produkte im Inneren des Gangs von den Eingangsförderern bis zu den vom LVS zugewiesenen Stellplätzen.
Auf der unteren Ebene der Regale wurden 36 schwerkraftgesteuerte Kanäle zur Kommissionierung eingerichtet, die mit dem Arbeitsgang verbunden sind. Jeder Kanal kann vier Paletten der gleichen Artikelart aufnehmen: eine Palette für die Kommissionierung und die anderen als Reserve. Die Kommissionierer suchen mithilfe ihrer Handscanner die Artikelarten für die einzelnen Aufträge und entnehmen sie von der ersten Palette.
Wenn die Palette eines schwerkraftgesteuerten Kanals leer ist, weist das LVS das Regalbediengerät an, diesen Kanal mit der entsprechenden Ware aufzufüllen. Der Vorteil dieses Systems besteht darin, dass die für die Kommissionierung erforderlichen Artikel jederzeit verfügbar sind, wodurch Unterbrechungen und Verzögerungen bei der Auftragszusammenstellung vermieden werden.
Easy WMS: Sequenzierung und Warenkontrolle
Die beiden automatisierten Lager von HAVI, das Tiefkühllager und das Lager mit geregelter Temperatur werden vom Lagerverwaltungssystem (LVS) Easy WMS von Mecalux gesteuert. In dem automatisierten Lager mit Pallet Shuttle identifiziert Easy WMS die Artikel zum Zeitpunkt ihrer Ankunft im Lager und weist ihnen unter Berücksichtigung ihrer Stapelbarkeit und ihres Typs einen Stellplatz zu. Das System bietet eine lückenlose Rückverfolgbarkeit, sodass der genaue Standort aller Waren in Echtzeit bekannt ist.
Außerdem organisiert das LVS die Auftragszusammenstellung. Einerseits veranlasst es den Transport der erforderlichen Artikelarten zu den Kommissionierplätzen und andererseits teilt es den Kommissionierern mit, aus welchen Produkten sich die einzelnen Aufträge zusammensetzen. Bei der Durchführung all dieser Aufgaben berücksichtigt Easy WMS stets eine der Hauptanforderungen von HAVI: die Sequenzierung der Aufträge. Die Gruppierung und Sequenzierung der Waren für den späteren Versand vermeiden Fehler, beschleunigen den Ablauf und ermöglichen es, einen effizienteren Service zu bieten.
Im Lager mit Umgebungstemperatur wiederum steuert Easy WMS die Bewegungen des Regalbediengeräts. Dieses hat die Aufgabe, die schwerkraftgesteuerten Kommissionierkanäle mit Waren zu versorgen, wenn sie sich leeren. Easy WMS kommuniziert mit dem LVS von HAVI, um den Bestand zu kontrollieren, die Nachverfolgbarkeit zu sichern und alle Prozesse im Vertriebszentrum zu sequenzieren.
Technologie im Dienste der Kunden
HAVI verfügt über ein mit modernster Technologie ausgestattetes Vertriebszentrum mit effizienten Abläufen, das in der Lage ist, die Restaurants seiner Kunden entsprechend ihrem Bedarf unverzüglich zu beliefern. Die Automatisierung hat nicht nur die Abläufe im Lager beschleunigt, sondern auch die Logistikkosten gesenkt und die Arbeitsbedingungen des Lagerpersonals verbessert. Dabei ist zu betonen, dass diese Anlage es den Lagerarbeitern von HAVI ermöglicht hat, neue Fertigkeiten zu erlernen.
Vorteile für HAVI
- Klassifizierung der Waren: Das Lager wurde in drei Bereiche unterteilt, in denen verschiedene Lagerlösungen implementiert wurden, um die Waren abhängig von ihren Eigenschaften zu lagern und zu verwalten.
- Sequenzierung der Aufträge: Easy WMS übernimmt die Sequenzierung der zusammengestellten Aufträge und ihren Transport in den Bereich zur Ladevorbereitung, wo sie nach Auftrag oder Route klassifiziert werden.
- Technologie und Sicherheit: Die Automatisierung sorgt dafür, dass im Lager alle nötigen Sicherheitsanforderungen sowohl zum Schutz der Waren als auch der Lagerarbeiter eingehalten werden.
- Angenehmer Arbeitsplatz: HAVI hat sein Arbeitsumfeld modernisiert und dadurch einerseits die Arbeit für die Mitarbeiter attraktiver gemacht und andererseits dafür gesorgt, dass sie durch den Einsatz neuer Technologien neue Fertigkeiten erlernen können.
Portugal Vertriebszentrum: Palettenregale | |
---|---|
Lagerkapazität: | 6.341 Paletten |
Abmessungen der Paletten: | 800 x 1.200 mm |
Höchstgewicht der Paletten: | 1.000 kg |
Regalhöhe: | 8,5 m |
Galerie
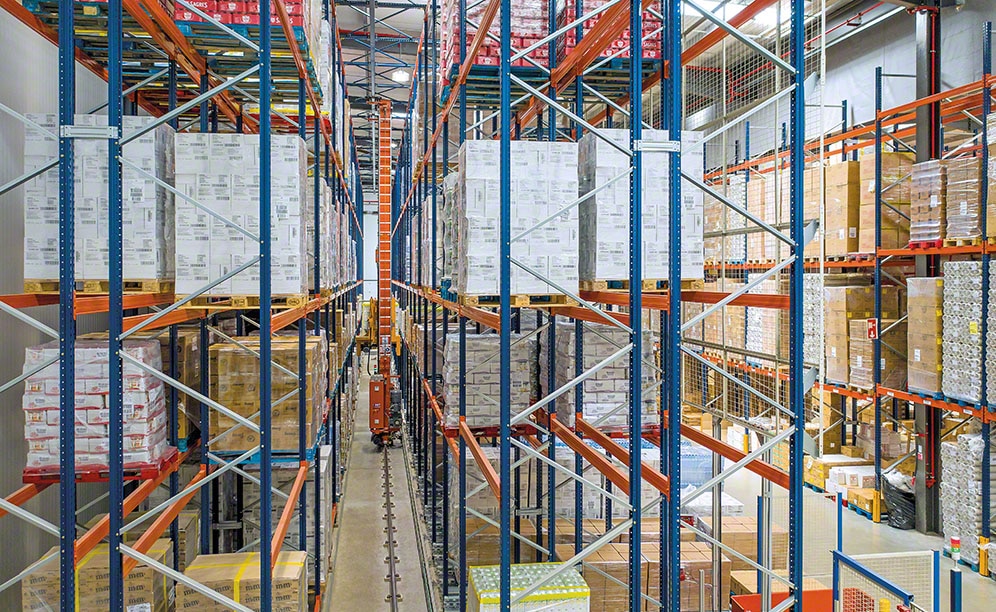
Pallet-Shuttle-System mit Regalbediengerät von HAVI in Portugal
Fragen Sie einen Experten