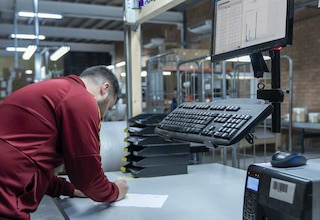
Continuous Improvement und dessen Anwendung in der Logistik
Continuous Improvement (kontinuierliche Verbesserung) zielt darauf ab, die Qualität und Leistung eines Produkts oder Prozesses durch die fortlaufende Analyse der beteiligten Elemente zu erhöhen. Diese Methode stammt ursprünglich aus Japan, wird aber auch bei westlichen Unternehmen immer beliebter. Continuous Improvement verspricht mehr Effizienz im Unternehmen dank kleiner, aber kontinuierlicher Veränderungen, die darauf abzielen, unproduktive Faktoren zu vermeiden und Regeln zu standardisieren.
In diesem Artikel wird erläutert, worin Continuous Improvement besteht, was die Hauptstrategien sind und wie es auf den Logistiksektor angewandt werden kann.
Was versteht man unter Continuous Improvement?
Unter Continuous Improvement versteht man die Umsetzung verschiedener Strategien zur Verbesserung und Optimierung von Prozessen, Produkten oder Dienstleistungen durch kleine Anpassungen aufgrund von umfassenden Kenntnissen der Abläufe und der Datenanalyse.
Es gibt mehrere Methoden des Continuous Improvement, um die Leistung einer Anlage zu verbessern. Die Kaizen- oder 5S-Methode hat sich aber aufgrund ihrer Einfachheit und Wirksamkeit zu einer der beliebtesten Methoden entwickelt.
Continuous Improvement nach Kaizen
Kaizen (Japanisch: „Veränderung zum Besseren”) ist ein System, das der japanische Ingenieur Taiichi Ohno nach dem Ende des Zweiten Weltkriegs für den Autohersteller Toyota entwickelt hat. Seine Funktion bestand darin, die Wettbewerbsfähigkeit des Unternehmens zu erhöhen und es mit amerikanischen Unternehmen auf eine Linie zu bringen. Mittlerweile ist es jedoch zu einem Standard in der Führung von Unternehmen auf der ganzen Welt geworden.
Die Kaizen-Methode basiert auf der Prämisse, dass es immer Raum für Verbesserungen gibt, auch wenn ein Prozess korrekt funktioniert. Diese Strategie, die insbesondere in den Bereichen Produktion und Logistik angewandt wird, umfasst eine Reihe von Verfahren zur Analyse der Betriebsabläufe, zur Erkennung von Ineffizienzen und zur Umsetzung von Änderungen. Im Mittelpunkt stehen fünf Prinzipien, die wegen ihrer Bezeichnungen als 5S bekannt sind:
- Seire (Sortieren): Der erste Prozess der Kaizen-Methode besteht darin, zu erfassen, welche Aufgaben einen echten Wert für das Produkt oder die Dienstleistung bringen (Gemba).
- Seiton (Systematisieren): Dem Arbeitnehmer müssen alle erforderlichen Werkzeuge zur Verfügung stehen, um schnell und produktiv arbeiten zu können. Die Anwendung von Seiton besteht in der Organisation von Arbeitsteams, um Umlagerungen oder ineffiziente Bewegungen zu vermeiden.
- Seiso (Sauberkeit): Die Erkennung von Fehlern und die Reinigung des Arbeitsplatzes sind der Schlüssel dafür, dass sich der Bediener wohl fühlt und mit Höchstleistung arbeitet.
- Seiketsu (Standardisieren): Nach der Ermittlung von Fehlern werden die erforderlichen Regeln oder Standards festgelegt, um die Effizienz der Prozesse zu erhöhen.
- Shitsuke (Selbstdisziplin): Diese letzte Phase ist von grundlegender Bedeutung für den Erfolg der vier vorherigen Prinzipien. Sie beinhaltet die Verpflichtung des gesamten Unternehmens, die neuen Regeln umzusetzen und eine Politik des Continuous Improvement zu verfolgen, um den Wert aller im Unternehmen ausgeführten Vorgänge zu steigern.
Aufgrund dieser 5S ist die Kaizen-Methode eine ideale Strategie, um die Rentabilität des Unternehmens zu steigern, alle Ineffizienzen zu ermitteln und zu beheben sowie vor allem alle Aspekte zu fördern, die zur Wertschöpfung beitragen.
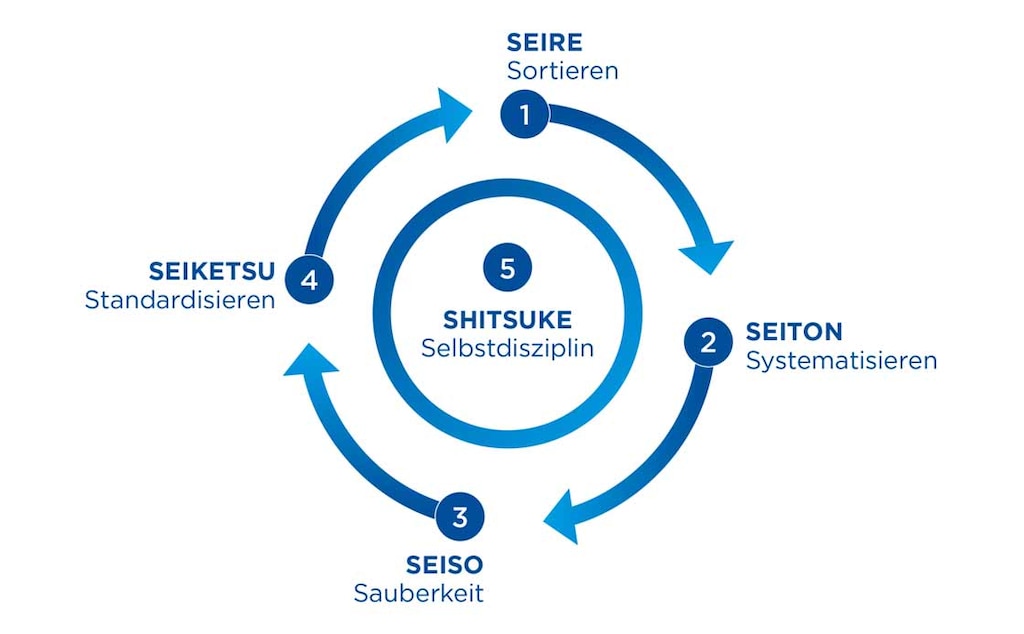
Andere Methoden des Continuous Improvement: von PDCA zu Six Sigma
Neben der 5S-Methode gibt es noch andere Strategien oder Hilfsmittel für das Continuous Improvement. Ziel dieser Strategien ist es, durch die generierten Informationen Spitzenleistungen in den Prozessen zu erzielen. Zwei weitere wichtige Methoden zur Standardisierung des Continuous Improvement sind:
- Der Demingkreis oder PDCA: PDCA ist eine Abkürzung für Plan, Do, Check, Act. Diese zyklische Strategie enthält die vier wesentlichen Schritte, um Ineffizienzen zu erkennen, Lösungen zu planen und letztendlich die Rentabilität aller Prozesse im Lager zu verbessern.
- Six Sigma: Diese Technik des Continuous Improvement besteht in der Behebung von Fehlern bei der Lieferung des Endprodukts an den Kunden. Ziel dieser Strategie ist es, maximal 3,4 Fehler pro Million Möglichkeiten zu erreichen, wobei als Fehler jede Störung gilt, die die Zufriedenheit des Kunden beeinträchtigt.
- Lean-Methode: Die Lean-Methode basiert auf der Identifizierung sämtlicher Phasen, die keinen Mehrwert für das Endprodukt bieten, um ein Produkt von höchster Qualität zu erreichen.
Um Continuous Improvement durchzuführen, muss nicht zwischen der einen oder anderen Methode gewählt werden. Keine Methode ist besser als die andere. Im Gegenteil, sie ergänzen sich gegenseitig und bieten jeweils Vorteile. Alle Strategien können und sollten gleichzeitig angewendet werden. Ziel ist immer die Verbesserung: Reduzierung von Ineffizienzen, Einführung schrittweiser Änderungen und Gewährleistung der korrekten Übernahme neuer Gewohnheiten im gesamten Unternehmen.
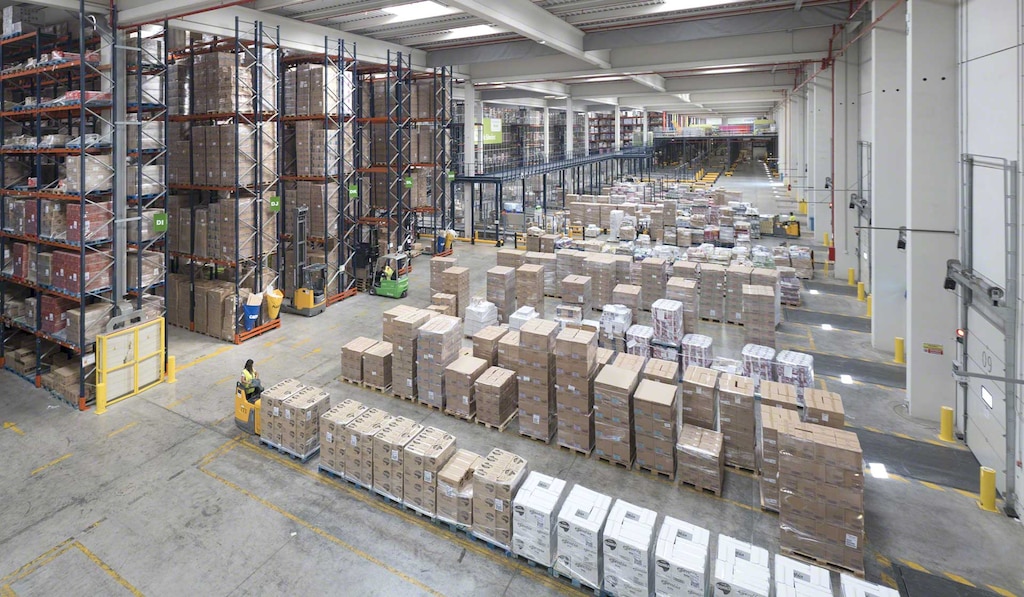
Verschwendung: Muda, Mura, Muri
Maßnahmen des Continuous Improvement beinhalten die kontinuierliche Analyse der Prozesse, um in jeder Phase eine maximale Rentabilität zu gewährleisten. So umfassen beispielsweise die Begriffe Muda, Mura und Muri eine Strategie zur Identifizierung von Fehlern und Verschwendung in der Produktion.
Dieses System, auch als die 3M des Produktionssystems von Toyota bekannt, basiert auf der Analyse von Fehlern und der Verschwendung in einem Produktionsprozess, um durch Veränderungen innerhalb des Unternehmens eine fehlerfreie Produktion zu gewährleisten und den Endkunden zufriedenzustellen. Dies sind die drei Schlüsselbegriffe sind:
- Muda (Verschwendung): Als Muda werden sämtliche Fehler bezeichnet, die Ressourcen verbrauchen und dem Endprodukt keinen Mehrwert verleihen. Ursprünglich bezog sich die Toyota-Methode auf sieben Verschwendungen, die normalerweise in einem Produktionszentrum anfallen: unnötige Bewegungen, überschüssige Bestände, sich wiederholende Vorgänge, Überproduktion, Stillstandzeiten von Produktionslinien, Überbearbeitung (Verfahren, die keinen Mehrwert schaffen) und ineffizienter Transport.
- Mura (Unausgeglichenheit): Der Produktionsleiter muss jede Unausgeglichenheit, Unterbrechung oder Veränderung der Auslastung feststellen, die zusätzliche Kosten in den Produktionslinien verursachen. Zu diesem Zweck ist es unerlässlich, eine umfassende Kontrolle der Leistung der Produktionsprozesse durchzuführen, um Mängel, Fehler oder Abweichungen zu erkennen. Durch die Implementierung von Methoden, die die Produktion an der Nachfrage ausrichten, z. B. das Kanban-System oder das Just-in-Time-Verfahren, können diese Unregelmäßigkeiten behoben werden.
- Muri (Überlastung): Eine Kombination aus Muda und Mura (Verschwendung und Fehler) verursacht Muri, nämlich Stress. Eine schlechte Planung resultiert in der Ermüdung der Arbeiter oder sogar in Engpässen in den Produktionslinien.
Durch die schrittweise Anwendung der 3M der Toyota-Methode werden also Verschwendungen in der Produktion sowie Störungen und Unausgeglichenheiten in der Arbeitsauslastung vermieden. Die Reduzierung von Muda und Mura resultiert in weniger Muri, d. h. Stress und Instabilität in den Produktionslinien.
Vorteile der Umsetzung von Continuous Improvement im Lager
Wie kann das Continuous Improvement zur Verbesserung der logistischen Aktivitäten und des täglichen Betriebs des Lagers beitragen? Die Hauptvorteile sind:
- Gewährleistung eines Qualitätsprodukts bzw. einer qualitativ hochwertigen Dienstleistung: Die Umsetzung von Continuous Improvement gewährleistet die erfolgreiche Umsetzung von Produktion oder Logistik, wodurch die Zufriedenheit des Endkunden sichergestellt wird.
- Senkung der Logistikkosten: Mit dieser Strategie ist es möglich, über die optimale Anzahl von Beständen im Lager zu verfügen, die Lead-Time der Lieferanten zu verkürzen, Priorität auf die produktivsten Vorgänge zu legen und diejenigen zu vermeiden, die keinen Mehrwert bieten.
- Effiziente Bewegungen: Methoden wie die Kaizen- oder PDCA-Methode vermeiden unnötige Bewegungen und schlagen effizientere Kommissionierrouten vor, wodurch eine höhere Produktivität der Bediener gewährleistet wird.
Diese Verbesserungen erleichtern ebenfalls die Einführung eines Pull-Flow-Systems in der Anlage. Dies bedeutet, dass die Abläufe im Lager nach dem JIT-Verfahren (Just-in-Time) durchgeführt werden, d. h. dass die Aufgaben dann ausgeführt werden, wenn eine Nachfrage seitens des Endkunden besteht, wodurch ineffiziente Abläufe und Risiken wie Überbestand oder Veralterung der Waren vermieden werden.
Mecalux verfügt hierfür über vielfältige Lösungen, um die Umsetzung des Continuous Improvement, z. B. nach Kaizen oder PDCA, zu unterstützen. Die Software Supply Chain Analytics, eine erweiterte Funktionalität von Easy WMS, ermöglicht es dem Logistikleiter, sämtliche Daten über das Lager zu sammeln und diese Informationen zu strukturieren, um die relevanten logistischen KPIs zu bestimmen und die Auswirkungen des Continuous Improvement zu messen.
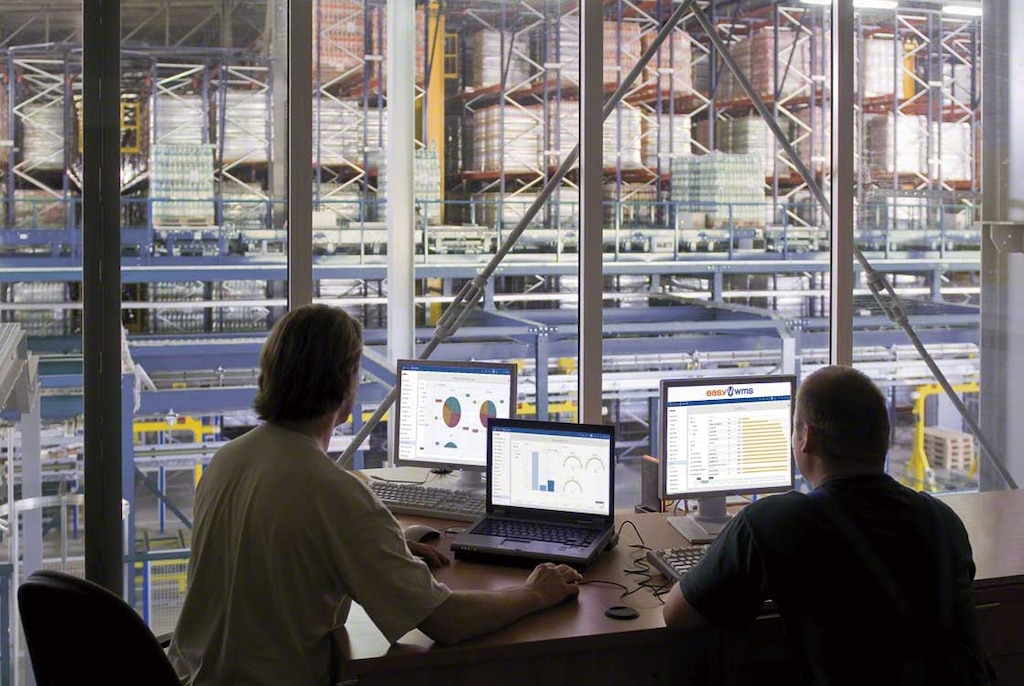
Continuous Improvement als Garantie für Wettbewerbsfähigkeit
Vor dem Hintergrund einer sich ständig wandelnden Logistik mit Technologien, die in nicht allzu ferner Zukunft das Tagesgeschäft von Unternehmen revolutionieren werden, müssen Unternehmen Maßnahmen zum Continuous Improvement umsetzen, um wettbewerbsfähig zu bleiben.
Der erste Schritt zu mehr Effizienz in der Lieferkette ist die Überwachung und Analyse der KPIs im Lager mit dem Ziel, Schwachstellen zu erkennen und auf jene Prozesse zu verzichten, die keinen Mehrwert bieten. Die Umsetzung von Continuous Improvement im Unternehmen ist die einzige Möglichkeit, die Logistikkosten zu senken und die jedem Unternehmen zur Verfügung stehenden Ressourcen zu optimieren.
Wenn auch Sie die Leistung Ihres Lagers optimieren möchten, dann kontaktieren Sie uns. Einer unserer Experten wird Ihnen helfen, den maximalen Nutzen aus der Logistik Ihres Unternehmens zu ziehen.