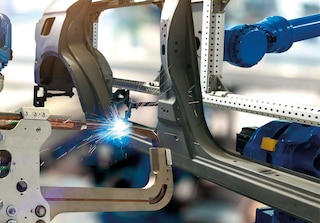
MRP: Ein Meilenstein im Produktionsprozess
Die Planung des für den Produktionsprozess erforderlichen Materials ist in jeder Anlage eine komplexe logistische Herausforderung. Wie viel Rohmaterial wird gebraucht, wann wird es benötigt oder wie viele Einheiten müssen produziert werden? Dies sind einige der Fragen, die Hersteller seit Jahrzehnten mithilfe der Materialbedarfsplanung (Material Requirements Planning, MRP) beantworten.
Dieser Beitrag behandelt Aspekte rund um die Materialbedarfsplanung: Was versteht man unter diesem Konzept, wie funktioniert es, welche Vorteile bietet sie und warum war und ist sie im Produktionsprozess so wichtig? Darüber hinaus wird der Unterschied zwischen der MRP und einem ERP-System erläutert.
Was ist die MRP?
Die Materialbedarfsplanung bzw. Material Requirements Planning ist eine Methode zur Verwaltung von Produktionsprozessen und zur vorherigen Koordinierung der Herstellung, des Einkaufs und der Lieferung des Endprodukts.
Die Materialbedarfsplanung entstand in den 1970er Jahren und verzeichnete einen rasanten Aufschwung. Laut dem 1975 von D. R. Kiran verfassten Buch Production Planning and Control: A Comprehensive Approach nutzten bereits schätzungsweise 700 Unternehmen die MRP zur Optimierung ihrer Produktionsprozesse. Diese Zahl wuchs um 174 % pro Jahr und belief sich 1981, nur sechs Jahre später, auf 8.000 Unternehmen.
Heutzutage gilt die MRP als Ursprung der modernen Softwares, die auf die Verbesserung industrieller Prozesse abzielen: MRP II (Manufacturing Resource Planning), ERP (Enterprise Resource Planning), CRM (Customer Relationship Management), SRM (Supplier Relationship Management) oder MES (Manufacturing Execution System).
Mithilfe der MRP wird die Produktion organisiert und das Bestandsmanagement gemäß den Anforderungen des Unternehmens optimiert. Dank der Materialbedarfsplanung rücken Hersteller näher an ihr Hauptziel: jederzeit über genau das Material zu verfügen, um Produkte herzustellen und sie in kürzester Zeit und zu möglichst geringen Kosten an die Kunden zu liefern.
Wie funktioniert die MRP?
Für eine erfolgreiche MRP sind einige Eingabedaten unverzichtbar:
- Master Production Schedule: Dieser Produktionsplan gibt an, wie viele Artikel in welchen Zeiträumen produziert werden.
- Stückliste: Die Stückliste (Bill of Materials, BOM) definiert, welche Rohstoffe in welcher Menge und welche Produktionsprozesse erforderlich sind, um eine Einheit des Endprodukts zu produzieren.
- Bestandsverzeichnis: Es enthält Informationen zum Bestand (verfügbarer Bestand, Auftragsbestand, stornierte Aufträge, Vorlaufzeit usw.). Ziel ist es, zu wissen, welcher Rohstoff zur sofortigen Verwendung verfügbar ist.
Anhand dieser Eingabedaten erstellt das Dispositionssystem die folgenden Ausgabedaten:
- Recommended Production Schedule: Bei diesem empfohlenen Produktionsplan wird ein Kalender mit den Terminen des Produktionsprozesses (Start und Ende), den erforderlichen Mengen für jeden Arbeitsschritt im Arbeitsplan und der Stückliste erstellt. Ziel ist es, die im Master Production Schedule festgelegte Nachfrage zu bedienen.
- Recommended Purchasing Schedule: Hier werden die Daten angezeigt, an denen die gekauften Materialien eingehen werden, sowie die Daten, an denen neue Aufträge erteilt werden müssen, damit der Produktionsplan eingehalten wird.
So stellt die MRP sicher, dass die richtigen Materialien geliefert werden, um einen Mindestbestand zur Versorgung der Produktion und gleichzeitig eine effiziente Planung von Herstellung, Einkauf und Lieferung des Materials zu gewährleisten.
Beispiel für die Materialbedarfsplanung
Nachdem der Master Production Schedule und die Stückliste erstellt wurden, wird festgelegt, dass für die Herstellung eines Endprodukts (Produkt X) 2 Einheiten von Material A und 1 Einheit von Material B erforderlich sind. Für jede Einheit von Material A sind 3 Einheiten von C erforderlich, während für jede Einheit von Material B 2 Einheiten von C und 4 Einheiten von D erforderlich sind.
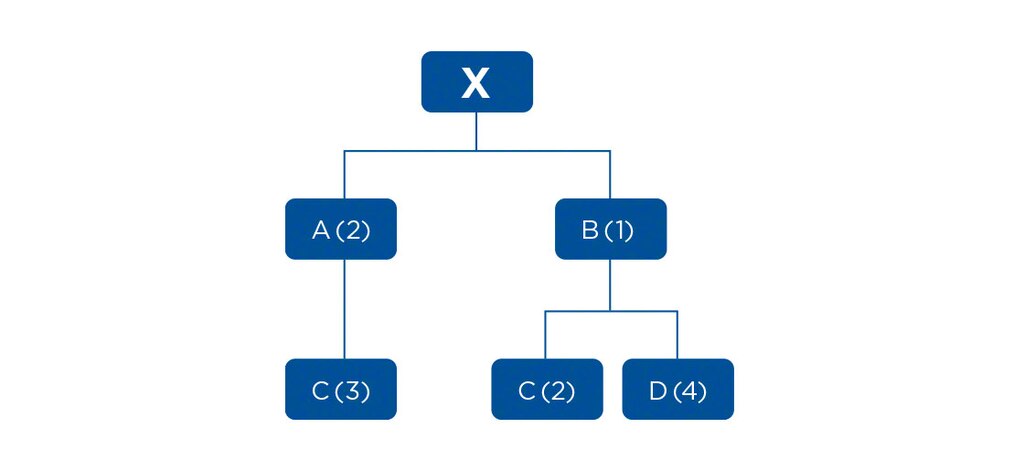
Anschließend wird das Bestandsverzeichnis (Inventory Record File, IRF) detailliert erstellt, das den verfügbaren Bestand und die Vorlaufzeit (Lead Time) bis zum Erhalt der einzelnen Produkte widerspiegelt:
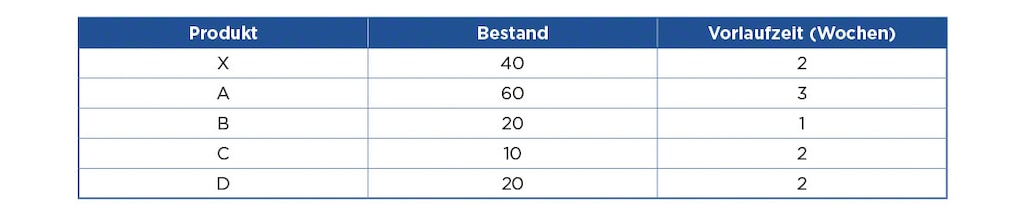
Wenn wir annehmen, dass in 10 Wochen 100 Einheiten von Produkt X produziert werden sollen, sieht die Materialbedarfsplanung wie folgt aus:
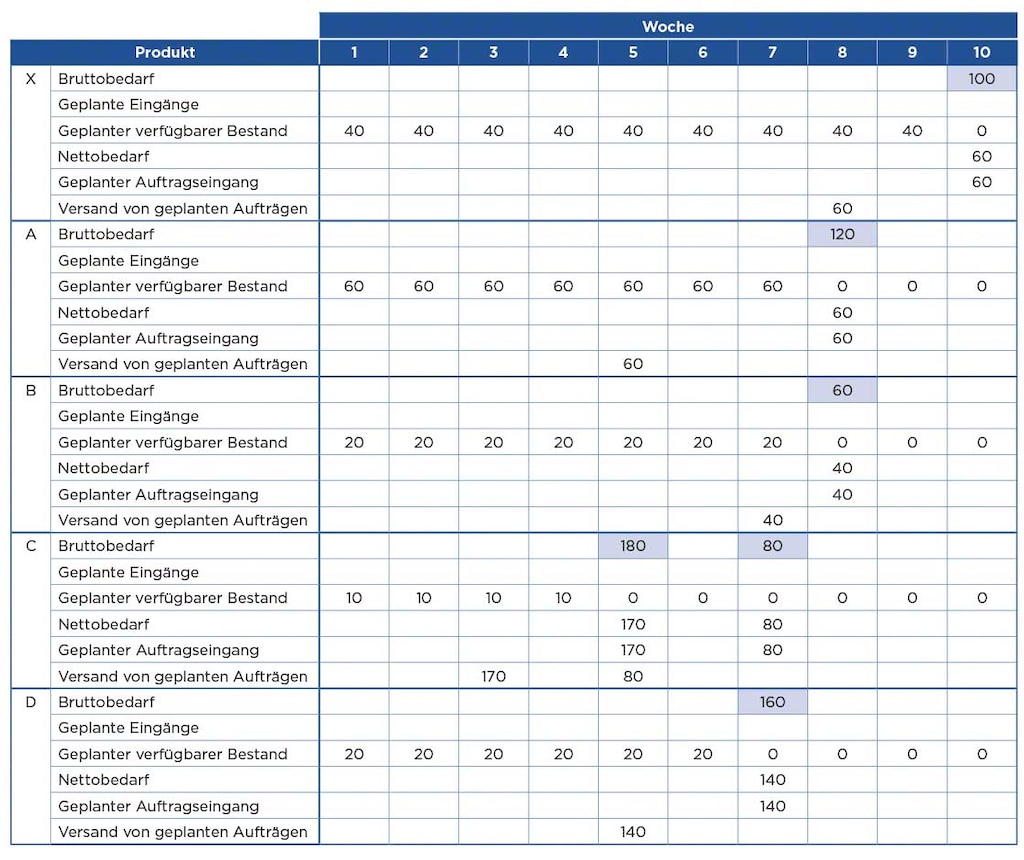
Die Tabelle verdeutlicht, dass, um 100 Einheiten des Produkts X in Woche 10 verfügbar zu haben, 60 zusätzliche Einheiten zu den bereits im Bestand vorhandenen 40 Einheiten benötigt werden. Da im Bestandsverzeichnis festgelegt ist, dass die Vorlaufzeit (Lead Time) für Produkt X 2 Wochen beträgt, muss die Bestellung in Woche 8 aufgegeben werden.
Wenn 2 Einheiten von Produkt A pro Einheit von Produkt X erforderlich sind, bedeutet dies, dass 120 Einheiten von Produkt A für Woche 8 benötigt werden. Da bereits 60 Einheiten im Bestand verfügbar sind, beträgt der Nettobedarf für Produkt A ebenfalls 60 Einheiten. Unter Berücksichtigung der Vorlaufzeit müssen diese Einheiten drei Wochen im Voraus bestellt werden.
Nach dem gleichen Muster wird ebenfalls der Nettobedarf für die Produkte B, C und D festgelegt, sowie die Woche, in der er bestellt werden muss.
Funktionsweise und Vorteile der Verwendung eines MRP
Im Produktionsprozess wird anhand der Materialbedarfsplanung das erforderliche Rohmaterial, die erforderlichen Materialkomponenten sowie die Menge des herzustellenden Endprodukts identifiziert.
Die Materialbedarfsplanung bietet die folgenden Vorteile:
- Vollständige Verfügbarkeit des Rohmaterials für die Produktion.
- Einhaltung der Lieferzeiten.
- Beibehaltung eines niedrigen Bestands an Rohstoffen und Fertigprodukten.
- Planung von Produktion, Lieferaufträgen und Einkäufen.
- Kostensenkung.
Mit der MRP lassen sich viele der Probleme lösen, mit denen Hersteller täglich konfrontiert sind, insbesondere beim Einkauf von Rohstoffen. Falsche oder unzureichende Einkäufe können die Lieferzeiten verzögern und, falls mehr Material als nötig gekauft wird, zu zusätzlichen Kosten bei der Lagerung führen.
Der Unterschied zwischen MRP und MRP2
In den frühen 1980er Jahren entwickelte sich die Materialbedarfsplanung (Material Requirements Planning) zu MRP2 (Manufacturing Resource Planning), einem fortschrittlicheren Planungssystem mit einem breiteren Anwendungsbereich. Die wichtigsten Unterschiede zwischen den beiden Systemen sind:
- Neben der Planung und Verwaltung der für die Produktion erforderlichen Materialien umfasst MRP2 auch andere Unternehmensbereiche, wie den kaufmännischen und finanziellen Bereich.
- Während MRP auf Grundlage des Master Production Schedule arbeitet, basiert MRP2 auf der Nachfrage und dem Marktverhalten.
- MRP2 analysiert das Verhalten des Unternehmens, um eine effiziente Planung durchzuführen, während die MRP die Planung auf Daten der Praxis und der bisherigen Erfahrungen des Unternehmens ausrichtet.
- Im Gegensatz zu MRP ist die MRP2 ein geschlossenes System. Das bedeutet, dass MRP2 Rückmeldungen zu den von ihm erstellten Berichten geben kann, wodurch Neuplanungen besser an die tatsächlichen Gegebenheiten angepasst werden können.
MRP2 stellt die modernere Version der MRP dar. Es beantwortet nicht nur die Frage, wie viel und wann produziert werden soll, sondern definiert auch, welche Ressourcen in welcher Menge und zu welchem Zeitpunkt für die Produktion benötigt werden.
Der Unterschied zwischen der MRP und dem ERP
ERP-Systeme (Enterprise Resource Planning) wurden erstmals in den 1990er Jahren eingesetzt und sind im Vergleich zu ihren Vorgängern noch umfassender und vielseitiger als die MRP. Der Hauptunterschied zwischen den Systemen besteht darin, dass das ERP-System alle Unternehmensbereiche zentral verwalten kann.
Das MRP ist also eine Software, die isoliert arbeitet, während das ERP die von jeder Abteilung verwendeten Computersysteme integriert und kombiniert, um eine zentralisierte Datenbank zu erstellen. Auf diese Weise kann jeder Bereich des Unternehmens in Echtzeit auf Informationen zugreifen, Arbeitsabläufe steuern, Fehler minimieren und mit anderen Abteilungen kommunizieren.
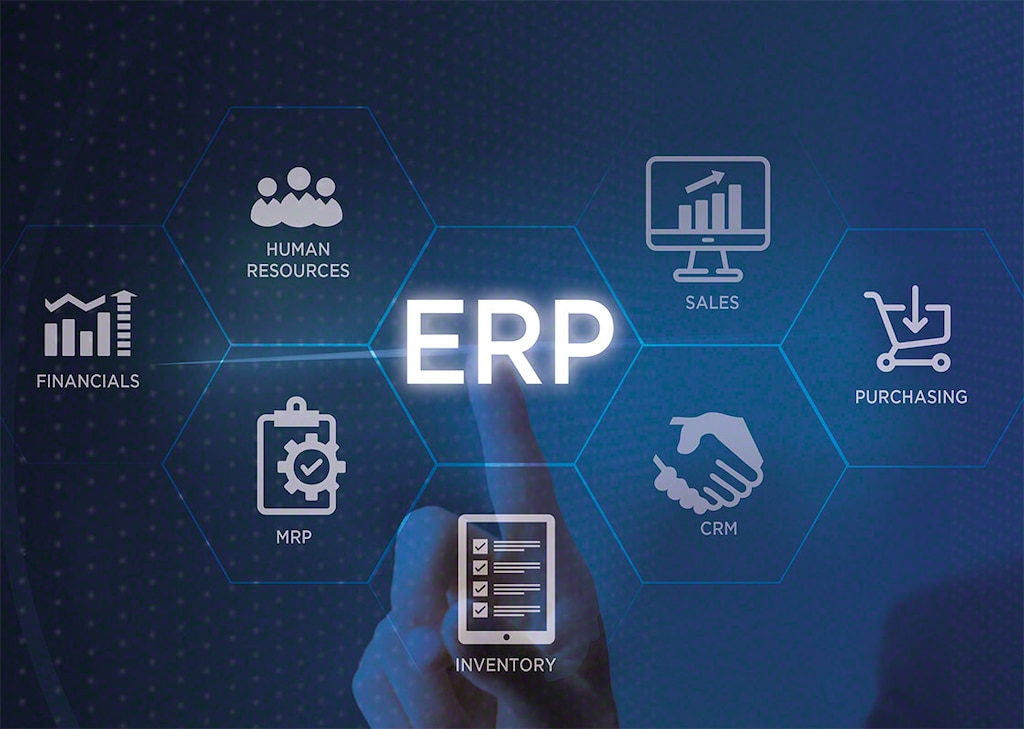
MRP: Zeichen des technologischen Fortschritts
Heute, fünfzig Jahre nach der Geburtsstunde der Materialbedarfsplanung, kann man mit Fug und Recht sagen, dass sie einen Wendepunkt im Produktionsprozess darstellte. Die grundlegende Funktionsweise der Materialbedarfsplanung, nämlich die Vorausplanung des Bedarfs, wurde an die neuen Technologien angepasst, um die Rentabilität der Lieferkette noch weiter zu erhöhen.
Bei Mecalux setzen wir uns stets für die innovativsten technologischen Lösungen auf dem Markt ein, sowohl im Bereich der Lagerhaltung als auch im Bereich der Logistik, zum Beispiel mit Easy WMS. Dieses Lagerverwaltungssystem kann mit sämtlichen ERP-Systemen integriert werden, sodass beide Systeme Daten und Informationen übertragen können, um eine höhere Produktivität im Lager zu erreichen.
Kontaktieren Sie uns, wenn unser Expertenteam Ihnen helfen soll, mehr aus Ihrer Lieferkette herauszuholen.