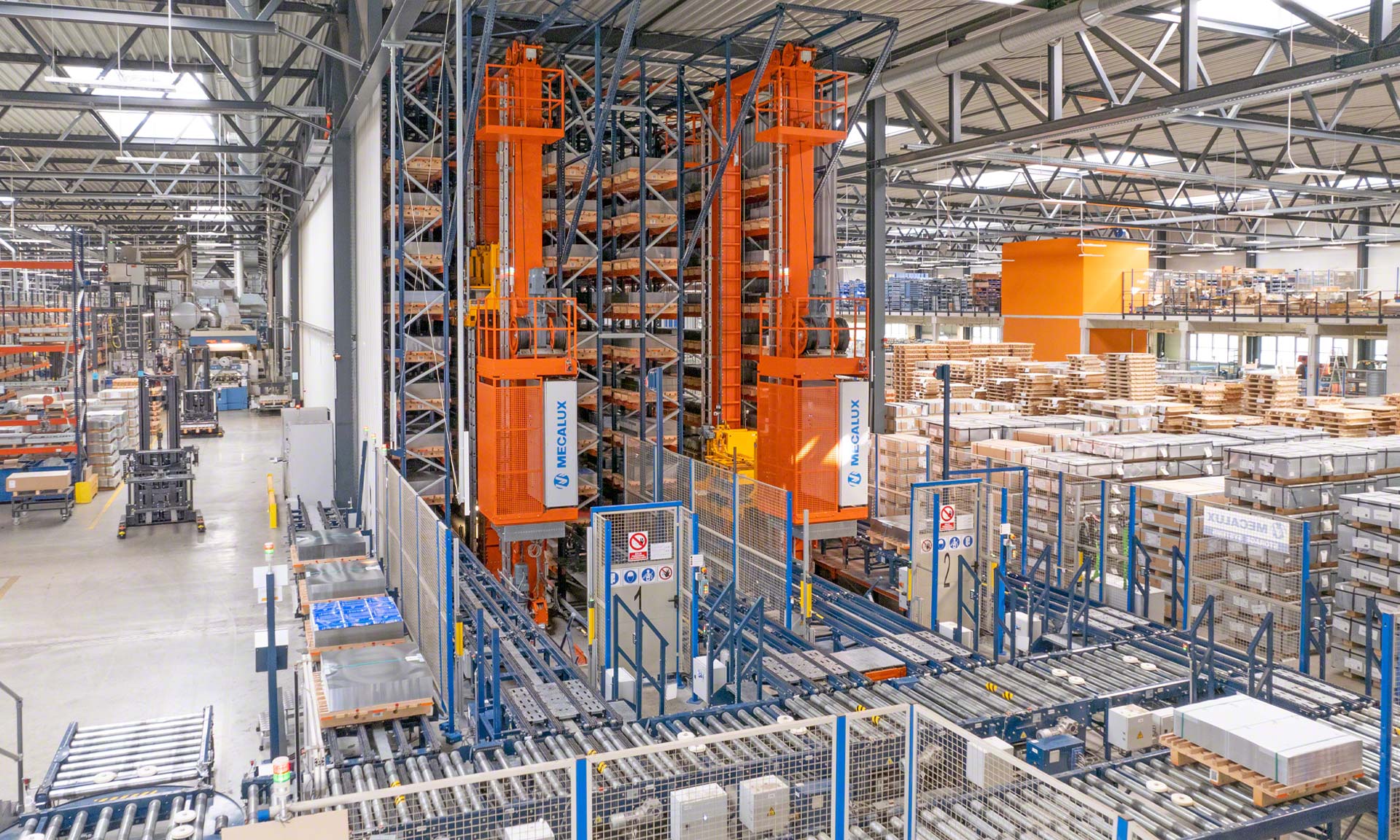
Der Blechwarenfabrik Limburg gelingt die automatisierte und gleichzeitig nachhaltige Logistik
Die Blechwarenfabrik Limburg integriert alle Produktions- und Logistikprozesse in einer neuen, vollautomatisierten und digitalisierten 63.000 m² großen Anlage.
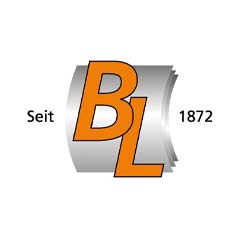
An seinem neuen Standort in Limburg-Offheim produziert das Unternehmen Blechwarenfabrik, ein Hersteller von Behältern aus Weißblech, jährlich über 100 Millionen verschiedener Behälter wie Dosen, Kanister und Eimer. Die Produktionsstätte verfügt über zwei automatische Lager. Über die Lagerverwaltungssoftware Easy WMS von Mecalux, die den Transport der Rohstoffe steuert, sind beide Lager mit der Produktion verknüpft.
Blechwarenfabrik: Tradition und Innovation
Die Blechwarenfabrik Limburg ist ein in Europa führendes Unternehmen in der Produktion von Weißblechbehältern, die in vielen Branchen (hauptsächlich im Bereich der Lagerung und Handhabung von chemischen Erzeugnissen) Verwendung finden.
- Gründungsjahr: 1872
- Anzahl Mitarbeiter: Über 500 Personen
- Produktionskapazität: Über 100 Millionen Behälter aus Weißblech pro Jahr
- Produktionsstandorte: Deutschland, Dänemark, Russland und Polen
HERAUSFORDERUNGEN
|
LÖSUNGEN
|
VORTEILE
|
---|
Die Blechwarenfabrik, ein in Europa führendes Unternehmen in der Produktion von Weißblechbehältern für chemische Erzeugnisse, hat angesichts seiner Umsatzsteigerungen die Logistik automatisiert und digitalisiert. In seiner 22.000m² großen Halle in Limburg-Offheim wurde der gesamte Materialfluss automatisiert: Fahrerlose Transportsysteme - besser bekannt unter der englischen Abkürzung AGV (deutsch: FTS) - verbinden die beiden automatischen Lager ganz autonom mit den Fertigungslinien. Früher besaß das Unternehmen zwei Produktionsstandorte in Deutschland, an denen alle Metallbehälter hergestellt wurden. Die Logistik wurde aufgrund fehlender Lagerfläche ausgelagert. „Die Lagerung der Rohstoffe erfolgte im Hauptlager. Sobald ein Fertigprodukt die Fertigungslinien verlassen hatte, wurde es in ein 5 km entferntes Lager transportiert“, erklärt Christoph Weber, technischer Leiter der Blechwarenfabrik.
Die Blechwarenfabrik fasste den Entschluss, die Produktions- und Logistikstandorte zusammenzulegen, Kosten zu sparen und alle logistischen Prozesse in einem hochdigitalisierten und besonders nachhaltigen Lager zu zentralisieren. Dafür hat das Unternehmen sein bis dahin ambitioniertestes Projekt gestartet: Den Aufbau eines neuen Standortes in Limburg-Offheim, in dem die komplette Unternehmensaktivität vereint werden sollte. In dieser modernen Anlage befinden sich Büros, 25 Fertigungslinien und ein Lagerbereich. Das Werk verarbeitet 22.000 Tonnen Stahl pro Jahr, aus denen über 100 Millionen Weißblechbehälter hergestellt werden. Die Zentralisierung der Logistik und der Produktion erfolgte schrittweise, da einige Produktionsphasen neu konfiguriert und an den neuen Standort angepasst werden mussten. Die Leitung des Unternehmens Blechwarenfabrik arbeitete eng mit dem technischen Team von Mecalux zusammen, um eine maßgeschneiderte Lösung zu finden. „Ein solches Großprojekt ist eine Herausforderung, da viele Details zu berücksichtigen sind. Mit Hilfe von Mecalux wurde die Verlagerung aller logistischen Abläufe in unser neues Werk perfekt durchgeführt“, betont Weber.
Robotik für mehr Effizienz und Nachhaltigkeit
Das Unternehmen setzte auf die Industrie 4.0 und stattete sich dafür mit der entsprechenden Technologie aus um Produktion und Logistik automatisch zu verbinden. „Früher wurden die Abläufe und der Materialfluss manuell verwaltet. Die Lagerarbeiter belieferten die Produktion mit Hilfe von Gabelstaplern. Außerdem war unsere Produktion auf verschiedenen Ebenen verteilt, was die Intralogistik erschwerte“, erklärt der technische Leiter.
Jetzt befinden sich Produktion und Lagerung in einer Anlage. Bis zu fünfzehn fahrerlose Transportsysteme befördern die Produkte innerhalb des Lagers, wobei nur minimale Eingriffe der Lagerarbeiter notwendig sind. Die Lagerverwaltungssoftware gibt den Robotern die Anweisung, wohin sie die Produkte befördern sollen. „Wir haben den Materialfluss vom Eingang bis zum Versand der Produkte automatisiert. Zusammen mit Mecalux haben wir in Europa die modernste Fabrik für Blechverpackungen gebaut“, berichtet Weber.
Die Minimierung der durch Produktions- und Logistikprozesse entstandenen Umweltbelastungen gehört seit jeher zu den Hauptanliegen der Blechwarenfabrik. Mit der Zentralisierung aller Prozesse auf einer Fläche entfällt der Transport von Waren zwischen Produktionsstätten und Lagern. Dadurch kann das Unternehmen seinen Ausstoß an Treibhausgasen um 2.600 Tonnen pro Jahr verringern.
Metallabfälle, die bei den verschiedenen industriellen Prozessen anfallen, werden in der Blechwarenfabrik in einem gesonderten Bereich gesammelt, um später recycelt zu werden. Darüber hinaus versorgen 4.100 Photovoltaikmodule auf dem Dach die Produktions- und Lagerungsprozesse mit Energie.
Logistik und Produktion: Effiziente Verknüpfung mit Easy WMS
Das neue Werk der Blechwarenfabrik besteht aus zwei automatischen Lagern: ein Rohstofflager in der Halle und ein Hochregallager in Silobauweise für Fertigprodukte. Bei Hochregallagern in Silobauweise (Silos) übernehmen die Regalanlagen die tragende Funktion des Gebäudes. Die Regalanlagen tragen ihr Eigengewicht, das Gewicht der Seitenwände und des Daches sowie das Gewicht der Waren. Daneben hat Mecalux das Lagerverwaltungssystem Easy WMS implementiert, eine Software, die alle Prozesse in beiden Lagern verwaltet und optimiert.
„Die Integration von Produktion und Logistik war eine der größten Herausforderungen bei diesem Projekt. Diese Herausforderung haben wir gemeistert, indem wir die Produktionsprozesse schrittweise an die neuen Lagersysteme angepasst haben. Dadurch konnten wir auftretende Vorfälle sofort analysieren und beheben“, erklärt Uwe Wonsack, Betriebsleiter der Blechwarenfabrik. Die Lagerverwaltungssoftware Easy WMS ermöglicht eine effiziente Verknüpfung von Logistik und Produktion. Um zu wissen, welche Artikel in der Produktion benötigt werden und deren korrekte Verteilung zu steuern, verbindet sich die Mecalux-Software mit Infor, dem ERP-System der Blechwarenfabrik, sowie mit dem Manufacturing Execution System (MES). „Die Programme unterstützen sich gegenseitig. Sind Produktinformationen erforderlich, liefert Easy WMS alle Details, die verfügbare Menge und den genauen Stellplatz“, betont Wonsack. Das ERP-System wiederum ist mit weiteren Softwaresystemen verbunden, welche die Produktionsprozesse steuern; Dazu gehören eine Software, zur Steuerung der in der Produktion eingesetzten Palettierroboter, eine Software, die Daten über die Entwicklung der Arbeitsabläufe im Werk sammelt oder eine weitere, die diese Arbeitsabläufe organisiert, steuert und überwacht.
Easy WMS kommuniziert auch mit der Steuerungssoftware der fahrerlosen Transportsysteme (FTS), um den Materialfluss zwischen den Lagern und der Produktion zu steuern. „Die Fertigungslinien werden automatisch von den FTS versorgt. Wenn Easy WMS einen Auftrag aus der Produktion erhält, organisiert die Software dessen Vorbereitung im Lager. Die Produkte werden von den FTS aufgenommen und zur Fertigungslinie befördert, die sie angefordert hat. Der Prozess ist transparent, schnell und effektiv“, betont Wonsack.
Die Mecalux-Software verwaltet auch das Metallabfall-Recycling der Blechwarenfabrik. Wenn bei den Produktionsprozessen Abfälle anfallen, steuert Easy WMS deren Transport zum Recycling.
Lagerverwaltungssoftware: Lückenlose Rückverfolgbarkeit
Die Lagerverwaltungssoftware Easy WMS von Mecalux gewährleistet eine vollständige Rückverfolgbarkeit der gelagerten Produkte. Das Programm kann das Material vom Eingang der Rohstoffe bis zum Versand der Fertigprodukte zurückverfolgen. Die Verknüpfung von Logistik und Produktion über Easy WMS hat der Blechwarenfabrik viele Vorteile gebracht.
- Bestandsübersicht und Bestandsverwaltung in Echtzeit: Easy WMS kennt den Status und den genauen Standort der Artikel, sowohl von Rohstoffen als auch von Fertigprodukten.
- Unterstützung der Just-in-Time-Produktion: Mit der Software werden die Rohstoffe in der richtigen Menge und zum richtigen Zeitpunkt an die Produktionsprozesse geliefert.
- Verwaltung des Artikelstamms und der Materialliste: Für jeden Produktionsauftrag werden die für die Herstellung der Produkte notwendigen Rohstoffe konfiguriert.
- Verbesserung der Produktionsprozesse: Eine gute Organisation der Arbeitsabläufe und eine genaue Kontrolle der Waren führen zu mehr Effizienz und Flexibilität.
- Papierloses Arbeiten: Über Handscanner und Tablets fordern die Bediener die Rohstoffe an, die sie für ihre Arbeit benötigen.
„Easy WMS hat als wichtigste Neuerung die Bestandskontrolle eingeführt: Jetzt wissen wir jederzeit, wo sich die Produkte befinden“, fügt Wonsack hinzu. Durch die Bestandskontrolle konnte die Blechwarenfabrik die Waren besser steuern, was zu reibungslosen Betriebsabläufen beiträgt. Geordnete Abläufe sind der Schlüssel, um eine Just-in-time-Versorgung der Produktionslinien zu gewährleisten.
Vollautomatisierte Lieferkette
Das Unternehmen Blechwarenfabrik wusste, dass die Automatisierung die Kosten senken und die Effizienz der Lieferkette steigern würde. Es hat die Lagerung, die Vorbereitung und den Versand der Artikel optimiert und beschleunigt.
Regalbediengeräte, Palettenfördersysteme und fahrerlose Transportsysteme (FTS) sorgen für einen permanenten und kontrollierten Materialfluss. Täglich werden 600 Paletten mit Rohstoffen zu den Fertigungslinien befördert. Gleichzeitig werden 1.200 Paletten mit ca. 500.000 Metallgebinden von den Fertigungslinien abgeholt, eingelagert und für den Versand an hunderte Kunden des Unternehmens in ganz Europa bereit gestellt.
➤ Rohstofflager
Das automatische Rohstofflager (11 m hoch und 100 m lang) besteht aus zwei Gängen mit Regalen einfacher Tiefe auf beiden Seiten. Es verfügt über eine Kapazität von 2.500 Paletten für Weißblechtafeln, die für die Herstellung von Behältern verwendet werden.
Von den Lieferanten der Blechwarenfabrik gehen pro Tag durchschnittlich 125.000 Weißblechtafeln im Lager ein. Easy WMS steht permanent in Verbindung mit dem MES (Manufacturing Execution System) und ist beim Wareneingang dafür zuständig, dass die Weißblechtafeln in der richtigen Position auf der richtigen Palette positioniert werden. Die Position der Weißblechtafel auf der Palette hängt davon ab, welcher Artikel in den Fertigungslinien hergestellt werden soll.
„Die Ware wird nach dem FIFO-Prinzip verwaltet, d. h., die zuerst eingelagerte Palette wird als erste entnommen. Auf diese Weise verhindern wir, dass Artikel unbrauchbar werden. Zudem können wir einen kontinuierlichen Warenfluss gewährleisten“, erklärt Wonsack.
Easy WMS prüft, wie viele Weißblechtafeln in welcher Position für einen Auftrag benötigt werden. So kann sichergestellt werden, dass die Produktionslinien über die benötigte Ware verfügen. Sollte die angeforderte Menge nicht zur Verfügung stehen, werden andere Weißblechtafeln aus dem Lager entnommen und zum Palettenwender befördert, wo die Bediener die Anweisung über deren richtige Position erhalten.
Nach den Anweisungen von Easy WMS nehmen die FTS die Bleche an einem der beiden Ausgänge des automatischen Lagers auf und befördern sie automatisch zu den Palettenregalen, in der Nähe der Fertigungslinien.
Die Regale dienen als Puffer zur Zwischenlagerung der Rohstoffe, bis diese von den Fertigungslinien angefordert werden. Wurde der Stellplatz geleert, kann er mit einem anderen Artikel für den nächsten Produktionsauftrag wieder belegt werden.
➤ Fertigungslinien
Beginnen die Produktionsprozesse, weist Easy WMS die FTS an, die Rohstoffe und Halbfertigprodukte zu den entsprechenden Fertigungslinien zu transportieren. Zu den für die Produktionsaufträge benötigten Halbfertigprodukten gehören die Dosenrümpfe (sogenannte „bodies“). Diese Artikel kommen nicht ins automatische Lager, sie werden direkt in Palettenregalen neben den Produktionslinien platziert. Auch diese Produkte werden von Easy WMS zurückverfolgt. Die Lagerverwaltungssoftware gibt zum entsprechenden Zeitpunkt eine Anweisung, damit die Produkte an die Produktion weitergeleitet werden können. In der Produktion können die Bediener mit Easy WMS kommunizieren, um z. B. leere Paletten zu bestellen, defekte Ware zu melden oder überschüssige Rohstoffe an das Lager zurückzugeben.
„Für uns ist es sehr wichtig, dass die Bediener an den Produktionslinien keine Nebenaufgaben erledigen müssen und sich auf ihre Hauptaufgabe konzentrieren können. Über einen Handscanner können die Bediener die Produkte von Easy WMS anfordern“, fügt Wonsack hinzu.
Auf Anweisung von Easy WMS werden auch die Abfälle von den FTS zum Recycling befördert.
➤ Lager für Fertigprodukte
Das automatische Hochregallager in Silobauweise mit einer Kapazität von 18.000 Paletten ist 31 m hoch und besteht aus vier Gängen mit Regalen doppelter Tiefe auf beiden Seiten.
Jede Stunde kommen etwa 80 Paletten von den Fertigungslinien. Vor dem Einfahren in das Lager durchlaufen die Produkte eine Kontrollstation, in der geprüft wird, ob sie den Anforderungen für ihren Stellplatz in den Regalen entsprechen. Daraufhin weist Easy WMS jedem Produkt einen Stellplatz zu. Die Software enthält Regeln und Algorithmen, um den besten Standort für jede Palette zu bestimmen. Dies geschieht unter Berücksichtigung der jeweiligen Artikelart und deren Warenumschlag. Für den Versand informiert das ERP-System Easy WMS darüber, welche Paletten ausgeliefert werden müssen. Anschließend weist die LVS jedem Ausgabeauftrag ein LKW-Tor zu. Jede Stunde verlassen 100 Paletten das Lager und gelangen entweder zur Auftragszusammenstellung oder direkt zu den LKW-Toren. „Die Versandprozesse verlaufen reibungslos“, bestätigt Wonsack.
Im vorderen Teil des Lagers wurde ein Kommissionierplatz eingerichtet. Dort werden die Aufträge nach dem Prinzip „Ware zum Mann“ vorbereitet, d. h. die Mitarbeiter warten auf die Artikel, die sie zur Vorbereitung jedes Auftrags benötigen. Die Mitarbeiter nehmen die Behälter von den Paletten, die aus dem Lager kommen, und stellen sie auf eine andere Palette zu den Artikeln des jeweiligen Auftrags. Die Bediener verfügen über einen Bildschirm und einen Handscanner, um die Anweisungen von Easy WMS Schritt für Schritt durchführen zu können. So werden sie jederzeit darüber informiert, welche Produkte sie von den Paletten entnehmen und in welche Aufträge sie diese einordnen müssen. Damit hat das Unternehmen Blechwarenfabrik das Fehlerrisiko deutlich reduziert.
Paletten, die direkt zum Versand gehen sollen, werden etikettiert und zum entsprechenden LKW-Tor gefahren. Außerdem wurde eine Pufferfläche eingerichtet. Dort werden die Paletten gruppiert und entsprechend ihrer Auftragszugehörigkeit oder der Transportroute klassifiziert, um ihre Verladung auf den LKW zu beschleunigen.
Industrie 4.0 für mehr Effizienz und Nachhaltigkeit
Das Unternehmen Blechwarenfabrik Limburg hat durch den Einsatz von Technologie sein Wachstum gesichert und gesteigert. Die Blechwarenfabrik setzt auf die Industrie 4.0. und verfolgt damit das Ziel einer umfassenderen Prozesssteuerung und eines effizienteren Kundenservices. Mit der Automatisierung konnte das Unternehmen nicht nur seine Produktion auf über 100 Millionen Behälter pro Jahr steigern, es profitiert auch von einer nachhaltigeren Lieferkette. Mit den automatisierten Lösungen von Mecalux und der Lagerverwaltungssoftware Easy WMS verfügt das Unternehmen über eine vernetzte Lieferkette. Alle Prozesse werden von der Software für einen Zweck koordiniert: Die Produktionslinien zum richtigen Zeitpunkt zu versorgen. Digitalisierung und Automatisierung sind für die Blechwarenfabrik eine erfolgsversprechende Kombination und werden zweifellos zum zukünftigen Wachstum des Unternehmens beitragen.
Als wir unsere neue Zentrale in Limburg-Offheim planten, war uns klar, dass wir in die Automatisierung investieren müssen. Mit der Technologie unseres Partners Mecalux hat unsere Lieferkette einen großen Fortschritt erzielt.
Galerie
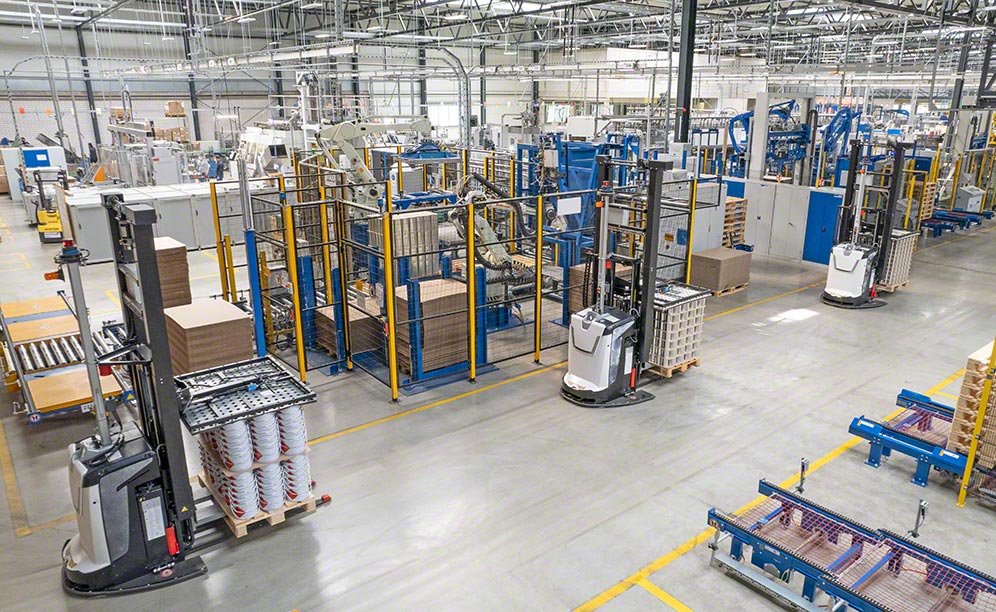
Automatisches Rohstofflager der Blechwarenfabrik Limburg
Fragen Sie einen Experten