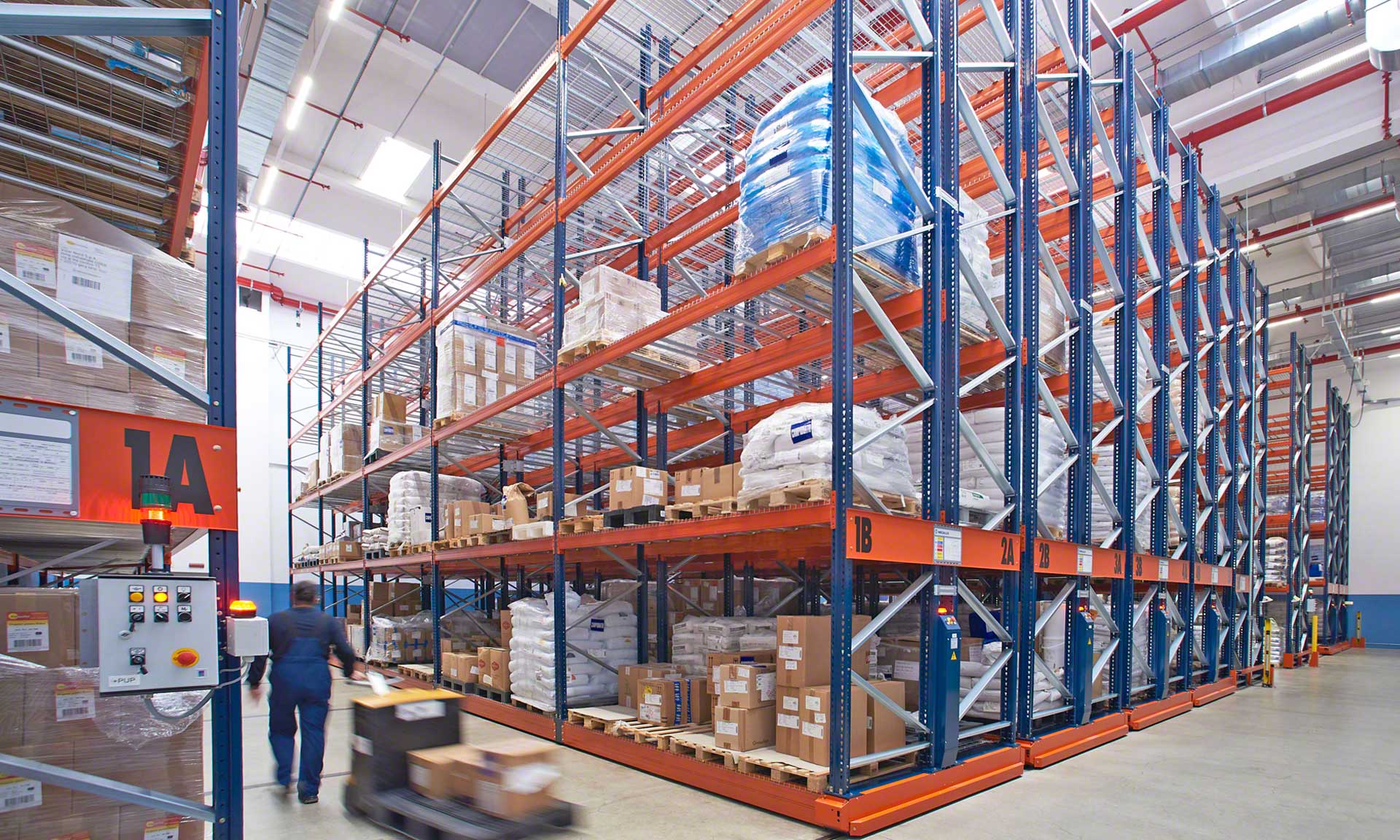
Vibar Nord: Automatisierung verbindet Produktion und Lager
Durch die Automatisierung wurde die Zeit für den Warentransport von der Produktion zum Versand reduziert

Vibar Nord, Hersteller von mehr als 5.000 Tonnen Lebensmitteln und Diätprodukten jährlich, hat sein neues Lager in Gera Lario im Norden Italiens automatisiert. Mecalux hat die Verbindung zwischen der Produktionsanlage und dem Versandbereich durch einen doppelten Förderkreislauf und ein Palettenhubsystem, die die beiden Bereiche automatisch verbinden, automatisiert. Mecalux hat ebenfalls zwei erdbebensichere Lagersysteme implementiert: Movirack-Verschieberegale und Palettenregale, durch die die Lagerkapazität um 70 % gesteigert wurde.
Vibar Nord wurde 1972 in Italien gegründet und produziert Lebensmittel und Diätprodukte in Pulver- und Granulatform für Drittfirmen. Es war das erste italienische Unternehmen, das ein Wirbelschichtverfahren zur Granulierung im Lebensmittel- und Diätbereich in industriellem Maßstab angewandt hat.
Das Unternehmen begann seine Tätigkeit in seiner historischen Produktionsanlage in Colico, in der Provinz Lecco. Auf einer Fläche von 10.000 m² ist die Einrichtung mit der neuesten Technik ausgestattet, um hohe Qualitätsstandards zu bieten. Aufgrund seines Wachstums in den letzten Jahren hat Vibar Nord eine neue Produktionsstätte 5 km entfernt in der Region Gera Lario in Betrieb genommen.
Standort in Gera Lario
Auf einer Fläche von 6.000 m² umfassen die Anlagen von Vibar Nord in Gera Lario Produktionslinien, ein Labor zur Produktqualitätskontrolle, einen F&E-Bereich und einen Lagerbereich für Rohstoffe und Fertigprodukte.
Eine der ersten Herausforderungen der neuen Anlage bestand darin, den Bewegungsfluss derart zu gestalten, dass der Produktionsbereich auf der ersten Ebene mit dem Lager- und Versandbereich auf der unteren Ebene verbunden wurde.
Die wichtigste Logistikanforderung von Vibar Nord war es, über ein intelligentes und gleichzeitig sicheres Transportsystem zu verfügen, über das die Paletten von der ersten Etage zur unteren Ebene befördert werden konnten. Hierbei musste ein Höhenunterschied von mehr als 7 Metern überwunden werden, und zwar unter Berücksichtigung des verfügbaren Raums, des erforderlichen Bewegungsflusses und der verwendeten Ladeeinheit: eine Art von Metallbehälter, der häufig in der Lebensmittelbranche verwendet wird.
Neben dieser logistischen Anforderung suchte Vibar Nord ebenfalls nach einem Lagersystem, das vielseitig und erdbebensicher sein musste und gleichzeitig die Fläche des Zentrums optimieren würde, um die im Produktionsprozess eingesetzten Rohstoffe lagern zu können. „Wir wollten die größtmögliche Lagerkapazität erzielen und die Auftragszusammenstellung beschleunigen. Außerdem mussten wir die Verbindung zwischen dem Lagerbereich auf der ersten Etage und den Laderampen auf der unteren Ebene verbessern“, erläutert Alessandro Tenzi, Betriebsleiter von Vibar Nord.
Nach Definition aller dieser Erfordernisse begann das Unternehmen mit der Suche nach einem Logistikanbieter, der die Anforderungen erfüllen konnte. „Wir entschieden uns für die Lösungen von Mecalux, nachdem wir sie mit anderen Wettbewerbern verglichen hatten”, sagt Tenzi.
Automatische Verbindung mit dem Versandbereich
Um die Bewegungen der Ware zwischen dem Produktionsbereich und dem Versandbereich zu beschleunigen, hat Mecalux einen doppelten Kreislauf mit Rollenförderern (von 28,4 m Länge) eingerichtet. Er ist mit einem Lastenaufzug verbunden, der die Ware automatisch auf die untere Ebene befördert.
Der Betriebsleiter von Vibar Nord bestätigt: „Die Fördervorrichtungen haben die Geschwindigkeit beim Transport der Ware gesteigert. Außerdem benötigen wir jetzt nur noch einen Lagerarbeiter, um die Ware auf der Fördervorrichtung zu platzieren. Früher nutzten wir einen langsameren Lastenaufzug, bei dem zwei Lagerarbeiter – einer pro Ebene – die Paletten jeweils in den Lastenaufzug platzieren bzw. aus diesem entnehmen mussten. Mit dem neuen System konnten wir die Zeit für die Palettenhandhabung um ein Drittel reduzieren.“
Sowohl der Förderkreislauf als auch der Lastenaufzug mussten personalisiert und an die Anforderungen von Vibar Nord angepasst werden. Das Unternehmen arbeitet mit zwei Arten von Paletten (800 / 1.000 x 1.200 mm) und mit einer Art von Metallbehälter mit nur zwei Kufen. Aufgrund dieser Problematik war eine detaillierte Studie erforderlich, um sicherzustellen, dass beide automatischen Handhabungsgeräte sowohl die horizontale als auch die vertikale Bewegung effizient durchführen konnten. Wenn das Produkt die Produktionslinien verlässt, platziert der Lagerarbeiter die Ladeeinheit mithilfe eines Staplers in einen der Förderkreisläufe, um diese automatisch zum Lastenaufzug zu befördern. Anschließend befördert der Lastenaufzug die Ware zur unteren Ebene, wo ein Förderkreislauf die Ladeeinheit zu einer der fünf Ausgangsstationen leitet.
In diesem Teil des Prozesses entnehmen die Lagerarbeiter die Ware aus dem Kreislauf und platzieren sie in einem regalfreien Bereich vor den Laderampen. Dort wird die Ware vorübergehend auf dem Boden gelagert und die Lagerarbeiter organisieren die Paletten nach Auftrag oder Transportroute, woraufhin sie auf die Lastwagen geladen werden. Neben dem Lastenaufzug verfügt das Lager ebenfalls über interne Fördertechnik, die hauptsächlich dazu dient, die gelagerten Rohstoffe von der ersten Ebene zu den Produktionslinien auf der oberen Ebene zu heben.
Erdbebensichere Regale
Für den Lagerbereich schlug Mecalux die Installation von zwei unterschiedlichen Lagersystemen zur Handhabung der Rohstoffe vor: Palettenregale und einen Block mit Movirack-Verschieberegalen. „Wir haben uns für die Movirack-Regale entschieden, da uns bewusst wurde, dass wir den verfügbaren Raum maximal nutzen konnten. Uns überzeugte die Fähigkeit dieses Lagersystems bei der Handhabung der Ware und die ausgezeichnete Fertigung der Struktur“, betont der Betriebsleiter von Vibar Nord.
Bei den Movirack-Regalen handelt es sich um ein Kompaktlagersystem, das die Lagerkapazität erhöhen kann und gleichzeitig direkten Zugriff auf die Ware gewährleistet. Die Zahlen sprechen für sich: „Mit den Regalen, die wir früher verwendeten, konnten wir 1.000 Paletten lagern. Die Movirack-Regale bieten Platz für 1.700, das heißt, es werden 70 % mehr Artikel in demselben Raum gelagert“, erklärt Tenzi.
Die Movirack-Regale sind 8,5 m hoch und bestehen aus vier Verschieberegalen und zwei festen Regalen an beiden Enden. Tenzi sagt: „Diese Lösung hilft uns dabei, den Raum in unserem Lager zu optimieren, und sorgt dafür, dass die Lagerarbeiter genügend Platz für den Zugang zur Ware und zum Rangieren haben.“
In den Movirack-Regalen kann die gesamte Ware von Vibar Nord – etwa 280 Artikelarten – sicher und kontrolliert gelagert werden, wofür nur eine Funkfernbedienung benötigt wird. Die Regale sind auf mobilen Verfahrwagen platziert, die sich selbstständig seitlich verschieben. Um den gewünschten Gang zu öffnen und die Ware zu entnehmen bzw. einzulagern, muss der Lagerarbeiter lediglich den entsprechenden Befehl mit einer Funkfernbedienung geben.
Das Unternehmen entschied sich für die Palettenregale aufgrund von deren Vielseitigkeit bei der Lagerung von Produkten aller Art: auf den fünf Ebenen werden 340 Paletten unterschiedlicher Höhe gelagert. Dieses System ist sehr widerstandsfähig und modular aufgebaut und beschleunigt zudem die Lade- und Entladevorgänge der Ware.
Movirack-Regale: Sicherheit in Bewegung
Die Bewegung der Movirack-Verschieberegale ist vollständig sicher, da diese mit verschiedenen Sicherheitsvorrichtungen ausgestattet sind:
- Äußere Lichtschranken. Sie halten die Bewegung der Regale an, wenn ein Lagerarbeiter das Ganginnere betritt.
- Innere Lichtschranken. Sie erkennen das Vorhandensein von Objekten im Gang, die die korrekte Funktionsweise des Systems verhindern würden.
- Not-Aus-Schalter. Sie unterbrechen bei jeglichem Vorfall unverzüglich die Bewegung der Regale.
- Näherungsschalter. Sie sorgen für einen sanften und sicheren Halt.
Logistik im Wachstum
Vibar Nord hat eine Herausforderung für die Zukunft. Das Unternehmen hat sich vorgenommen, alle seine Prozesse zu verbessern, um sein Wachstum fortzusetzen. „Wir möchten alle Artikelarten unseres alten Lagers an den neuen Standort in Gera Lario verlegen“, erklärt der Betriebsleiter der Firma. „Bisher haben wir eine Wachstumsrate von 5 % verzeichnet und wir erwarten, in Zukunft noch weiter zu wachsen“, fügt Tenzi hinzu.
Mithilfe des Palettenförderers mit Hubvorrichtung kann Vibar Nord mehrere Aufträge gleichzeitig und weitaus schneller verwalten. Außerdem gewährleistet die Struktur der Movirack-Palettenregale auf mobilen Verfahrwagen einen größeren Lagerraum zur Unterbringung der in der Produktion benötigten Rohstoffe. Jedes Lagersystem ist für ein bestimmtes Produkt vorgesehen, abhängig von seinen Eigenschaften und seiner Nachfrage. Die Kombination der beiden Lagersysteme hat dem Unternehmen dabei geholfen, die Fläche zu optimieren und eine effiziente Verwaltung der Produkte zu erreichen.
Mit den Lager- und Transportsystemen von Mecalux sparen wir bei der Handhabung der Ware Zeit. Wir sind mit den Movirack-Regalen sehr zufrieden, da die Lagerkapazität um 70 % gesteigert wurde. Durch die Fördervorrichtungen habaen wir die Zeit für den Warentransport von der Produktion zum Versandbereich um ein Drittel reduziert.
Vorteile für Vibar Nord
- 70 % mehr Artikel: Die Movirack-Regale nutzen den gesamten verfügbaren Raum, sodass eine Lagerkapazität von 1700 Paletten erreicht wird.
- Direkter Zugriff auf die Ware: Sowohl die Palettenregale als auch die Movirack-Regale bieten direkten Zugriff auf die Ware und beschleunigen somit die Lagerung und Entnahme der Paletten.
- Mit dem Produktionszentrum verbundenes Lager: Durch die Fördervorrichtungen wurde eine höhere Geschwindigkeit erzielt, wodurch die Zeit für den Warentransport von der Produktion zum Versandbereich um ein Drittel reduziert werden konnte.
Movirack-Regale | |
---|---|
Lagerkapazität: | 1.700 Paletten |
Abmessungen der Paletten: | 800 / 1.000 x 1.200 mm |
Höchstgewicht der Paletten: | 1.000 kg |
Regalhöhe: | 8,5 m |
Regallänge: | 18,8 m |
Galerie

Das neue Lager von Vibar Nord in Gera Lario mit Diätprodukten
Fragen Sie einen Experten