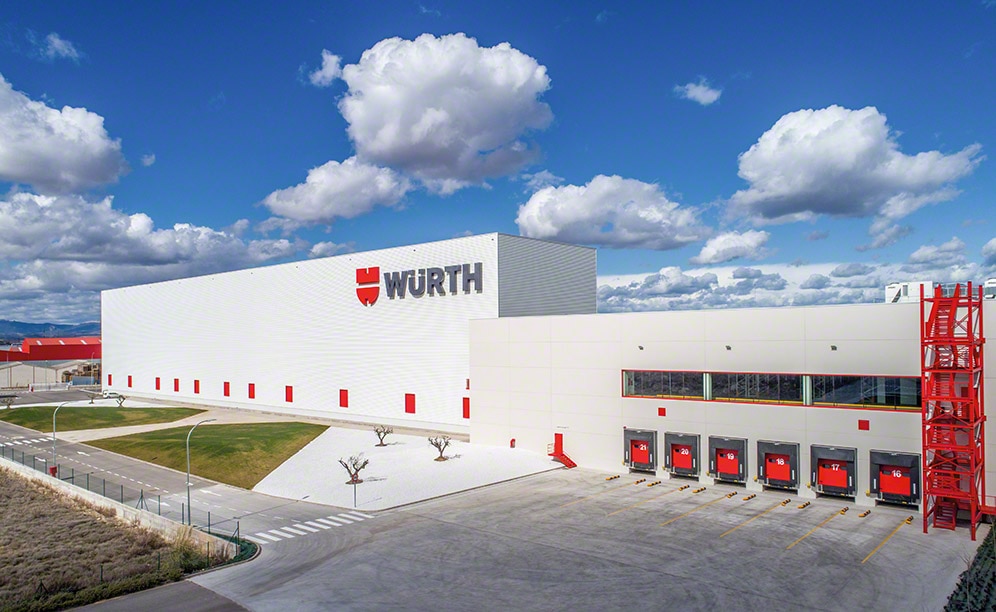
Ein vollständig automatisiertes, schlüsselfertiges Lager für Würth in La Rioja
Würth lagert das gesamte Sortiment an Werkzeugen, Schrauben, Dübeln und Bohrern an einem neuen Standort in La Rioja
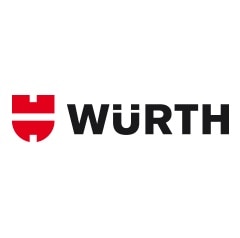
Pünktlich zur Feier des 40-jährigen Jubiläums der Niederlassung von Würth in Spanien hat der multinationale Konzern seine Anlage in Agoncillo (La Rioja) mithilfe von Lösungen erweitert, die von Mecalux entwickelt, hergestellt und installiert wurden. Vor Kurzem hat das Unternehmen ein neues Empfangs- und Versandgebäude sowie ein vollständig automatisiertes Hochregallager in Silobauweise für Paletten eingeweiht. Das automatisierte Lager, das über eine Lagerkapazität von 15.190 Paletten verfügt, kann bis zu 300 Paletten pro Stunde bewegen, was dazu beiträgt, das hohe Serviceniveau, das Würth bei der Belieferung seiner Kunden in ganz Spanien garantiert, aufrechtzuerhalten.
Würth: seit mehr als 40 Jahren in Spanien vertreten
Würth ist ein deutsches Unternehmen, das alle möglichen Arten von Befestigungs-, Verbindungs- und Montageelementen für spezialisierte Unternehmen aus verschiedenen Bereichen wie dem Bauwesen, Automobilsektor, Chemiebereich, Sanitärbereich usw. vertreibt. Sein umfangreicher Produktkatalog enthält über 125.000 Artikelarten, darunter Schrauben, Dübel, Bohr- und Schneidwerkzeuge, sonstige Werkzeuge, Arbeitskleidung usw. Das Unternehmen wurde 1945 im deutschen Künzelsau Baden-Württemberg als Schraubengroßhandel gegründet. Sein Hauptsitz befindet sich auch heute noch am selben Ort. Das Unternehmen beschäftigt ca. 74.000 Mitarbeiter in über 80 Ländern auf allen fünf Kontinenten.
1977 gründete Würth eine Niederlassung in Spanien, um die Bedürfnisse der 250.000 Kunden in diesem Land zu erfüllen. In Palau-solità i Plegamans (Barcelona) wurden der Hauptsitz und ein Logistikzentrum eingerichtet, und in Agoncillo (La Rioja) entstand ein weiteres Logistikzentrum. Der spanische Geschäftsbereich hat sich zu einem der größten Unternehmen innerhalb der Würth-Gruppe (nach der Zentrale in Deutschland) entwickelt. Um dieses Wachstum zu verstärken, hat das Unternehmen das Logistikzentrum in La Rioja in den letzten Jahren erweitert und modernisiert. Neben dem ursprünglichen Lager wurden ein automatisiertes Hochregallager in Silobauweise, ein Gebäude für die Laderampen und zusätzliche Parkplätze für Mitarbeiter und Besucher geplant.
Bei der Planung dieser Erweiterung forderte Würth, dass der Betrieb des Logistikzentrums während der Umsetzung nicht beeinträchtigt werden durfte. Pedro Montenegro, Logistikleiter von Würth España, erklärt: „Wir haben Hand in Hand mit den Ingenieuren und Projektleitern von Mecalux gearbeitet, damit sich die Bauarbeiten zu keinem Zeitpunkt auf unsere Kunden auswirkten.“
Dieses Lager erfüllt die Anforderungen der Firma bei Weitem und berücksichtigt auch die zukünftigen Wachstumsaussichten. Zu diesem Zweck wurde Platz für eine zukünftige Erweiterung reserviert. Die Technologie war einer der Wachstumstreiber von Würth. Aus diesem Grund verfügt das Logistikzentrum ebenfalls über die modernste Ausrüstung, um die Lagerarbeiten und den Transport der Waren in die übrigen Bereiche automatisch und mit nur minimalen menschlichen Eingriffen durchführen zu können.
Mecalux hat die Fördervorrichtungen, Regalbediengeräte, Hubsysteme und schienengeführten Fördersysteme entwickelt, die die Aufgabe haben, den vom Unternehmen gewünschten Warenfluss zu gewährleisten, um die Kunden in kürzester Zeit beliefern zu können. Darüber hinaus wurde auf sämtliche Details geachtet. Beispielsweise wurden die gelieferten Elemente an die Unternehmensfarben von Würth angepasst: Die Regale, Regalbediengeräte, schienengeführten Fördersysteme, Hubsysteme und Fördervorrichtungen sind in den Farben rot und weiß gehalten.
Pedro Montenegro – Logistikleiter von Würth España
„Für uns war ein Partner unerlässlich. Wir mussten eine Firma finden, mit der wir uns identifizieren konnten und von der wir glauben konnten, langfristig große Projekte mit ihr durchzuführen. Mecalux erfüllte alle notwendigen Anforderungen, die wir an diesen idealen ‚Partner‘ bei allen Logistikerweiterungen stellten.“
Hochregallager in Silobauweise: Die Regalanlage trägt das Gebäude
Das automatisierte Hochregallager in Silobauweise überragt wegen seiner beachtlichen Abmessungen die restlichen Gebäude: Es ist 26 m hoch, 115 m lang und 23 m breit. Die Arbeit mit Zehntausenden von Artikelarten stellte eine große Herausforderung für das Unternehmen dar, weshalb es unerlässlich war, die gesamte verfügbare Fläche auszunutzen, um die größtmögliche Lagerkapazität zu erreichen. Pedro Montenegro erläutert: „Einer der großen Vorteile der Lösung von Mecalux besteht darin, dass wir auf nur 3500 m2 bis zu 15.000 Paletten lagern können. Mit einem konventionellen Lager wie den bereits vorhandenen wäre dies einfach unmöglich gewesen.“
Das Lager besteht aus fünf Gängen mit Regalanlagen einfacher Tiefe auf beiden Seiten und den entsprechenden Regalbediengeräten für die Ein- und Auslagerung der Ware. Diese Geräte arbeiten mit einer Verfahrgeschwindigkeit von 220 m/min und einer Hubgeschwindigkeit von 54 m/min und sind in der Lage, bis zu 300 Paletten pro Stunde in kombinierten Zyklen zu bewegen, d. h. Ein- und Auslagerungen gleichzeitig vorzunehmen.
Das gesamte Lager wird mithilfe der Lagerverwaltungssoftware Easy WMS von Mecalux gesteuert, die mit dem Computersystem von Würth zusammenarbeitet, um die Nachverfolgung der gesamten Ware während des Eingangs, der Lagerung und des Ausgangs zu gewährleisten.
Ein an das Lager angrenzendes Gebäude
Zwischen dem neuen automatisierten Lager und dem bereits vorhandenen Lager wurde ein 15 Meter hohes Gebäude mit zwei Ebenen errichtet, von denen jede einem anderem Zweck dient.
Untere Ebene
Auf der unteren Ebene werden die Ein- und Ausgänge der Produkte an zwölf Be- und Entladerampen abgewickelt. Dazu wurde ein Förderkreislauf mit drei Eingangsstationen und zwei Ausgangsstationen installiert. Die Paletten durchlaufen vor der Einlagerung eine Palettenkontrollstation (PIE), an der das Gewicht, die Abmessungen der Ladung und der Zustand der Paletten (Zwischenräume, Klötze und Kufen) überprüft werden und das Produkt durch Ablesen des Barcode-Etiketts identifiziert wird.
Auf dieser Ebene werden die eingegangenen Paletten, die nur eine einzige Artikelart enthalten, überprüft. Paletten, die mehr als eine Artikelart enthalten, werden vorübergehend in der Regalanlage abgesetzt und später auf der oberen Ebene überprüft. Eine der Eingangsförderstrecken verfügt über ein automatisches System, das Trägerpaletten für solche Paletten liefert, die sich nicht in einem einwandfreien Zustand befinden. Nachdem die Ware die Kontrolle erfolgreich durchlaufen hat, transportiert ein Lastenaufzug sie auf die obere Ebene, wo sie in das automatisierte Lager gelangt. Dieser Lastenaufzug transportiert ebenfalls die aus dem automatisierten Lager kommenden Paletten in den Versandbereich.
Am Ende der Ausgangslinie werden die Trägerpaletten entnommen und gestapelt, sodass sie wieder für Einlagerungen verwendet werden können. Die für den Versand bestimmten Paletten werden im Bereich zur Ladevorbereitung auf dem Boden direkt vor den Laderampen in Gruppen angeordnet, die einer gleichen Bestellung oder Transportroute entsprechen.
Zur Anlage gehören zwei Lastenaufzüge. Einer hebt die Paletten vom Eingangsbereich auf die obere Ebene (Eingänge) und transportiert sie von der oberen Ebene hinunter in den Versandbereich (Ausgänge). Der andere Lastenaufzug transportiert die aus dem automatisierten Lager kommenden Paletten auf die untere Ebene des alten Lagers.
Obere Ebene
Auf der oberen Ebene transportiert ein Kreislauf mit schienengeführten Fördersystemen die für das automatisierte Lager bestimmten Paletten bis zu dem Gang, den ihnen Easy WMS von Mecalux zugewiesen hat. Gleichzeitig holt er die für den Versand bestimmten Paletten ab und transportiert sie zum Lastenaufzug, der sie auf die untere Ebene befördert.
Auf dieser Ebene werden ebenfalls die Paletten überprüft, die aus mehreren Artikelarten bestehen und vorher zwischengelagert wurden. Hier werden die Artikelarten getrennt und sortiert, die Mengen überprüft, die Produkte identifiziert und in das automatisierte Lager zurückgeschickt. Vor dem Kreislauf mit schienengeführten Fördersystemen wurden zwei Kommissionierstationen eingerichtet. Dort werden die Aufträge, die vollständige Behälter mit Produkten aus dem automatisierten Lager enthalten, zusammengestellt. Würth legte besonderen Wert darauf, diesen Vorgang so weit wie möglich zu beschleunigen, weshalb die Anlage so konzipiert wurde, dass pro Stunde bis zu 60 Paletten an jede Kommissionierstation geliefert werden können.
Die Kommissionierstationen verfügen über die notwendigen Geräte, um die verschiedenen Aufgaben ausführen zu können, wie Computer, Etikettendrucker und pneumatisch betätigte Arme, die die Handhabung der Produkte erleichtern (da diese sperrig und sehr schwer sein können). Mithilfe der schwerelosen Hubgeräte entnehmen die Lagerarbeiter die Artikel direkt von den Paletten, die die schienengeführten Fördersysteme zu den Kommissionierstationen transportiert haben, und setzen sie auf eine andere Palette. Auf dieser Palette werden die Produkte für die einzelnen Aufträge zusammengestellt. An den beiden Stationen können maximal acht Aufträge gleichzeitig zusammengestellt werden.
Auf der oberen Ebene befindet sich ebenfalls ein Förderkreislauf, der das neue automatisierte Lager mit dem bereits vorhandenen Lager von Würth verbindet. Dieses Lager hat eine Lagerkapazität von ca. 10.000 Paletten und ist für Produkte bestimmt, die aufgrund ihrer Abmessungen und der Produktart (Chemikalien) nicht im automatisierten Lager gelagert werden können. Hier wird zudem die Kommissionierung von Einheiten aller Artikelarten durchgeführt. Die Fördervorrichtungen versorgen das Lager mit den für die Kommissionierung notwendigen Produkten.
Vorteile für Würth
- Maßgeschneiderte Lösung: Die gesamte Fläche wurde ausgenutzt, um eine Lagerkapazität von 15.190 Paletten zu erreichen. Daneben wurde auch noch Platz für eine zukünftige Erweiterung reserviert.
- High-Tech-Lager: Die Abläufe im neuen Lager erfolgen vollautomatisch, was zu höheren und schnelleren Bewegungsflüssen und einer verringerten Fehleranzahl führt.
- Priorität bei der Auftragszusammenstellung: Das automatisierte Lager verfügt über einen speziellen Bereich, in dem vollständige Behälter kommissioniert werden, und ein Förderkreislauf versorgt das bereits vorhandene Lager mit der notwendigen Ware für die Kommissionierung geringer Mengen.
Hochregallager in Silobauweise von Würth España | |
---|---|
Lagerkapazität: | 15.190 Paletten |
Abmessungen der Paletten: | 800 x 1200 mm |
Höchstgewicht der Paletten: | 1000 kg |
Höhe des Lagers: | 26 m |
Länge des Lagers: | 115 m |
Breite des Lagers: | 23 m |
Galerie
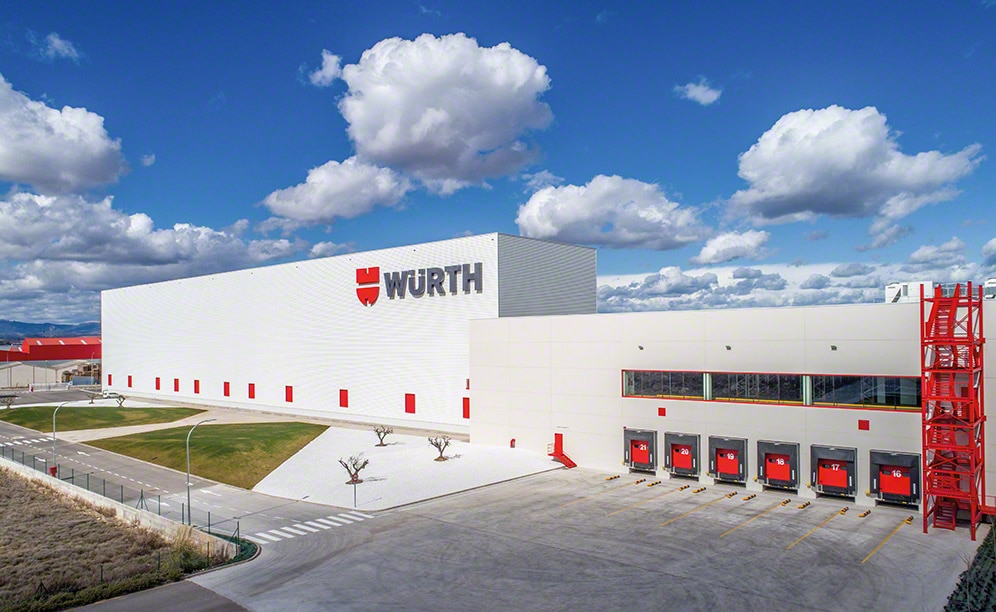
Die Firma aus Deutschland hat ein neues Lager in La Rioja (Spanien) eröffnet
Fragen Sie einen Experten