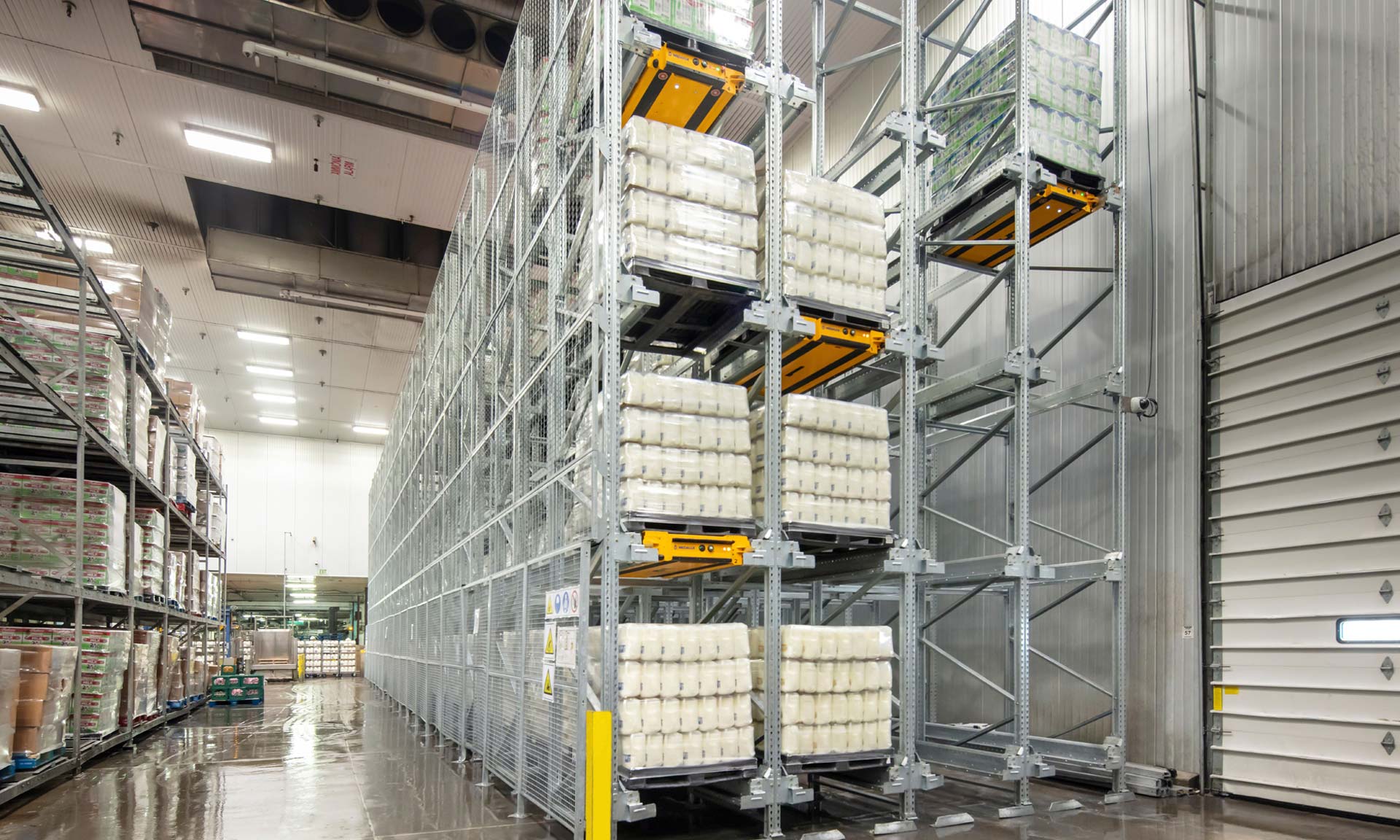
Das Pallet Shuttle verdoppelt die Lagerkapazität
Producers Dairy hat die Lagerkapazität mit dem Pallet-Shuttle-System von Interlake Mecalux verdoppelt
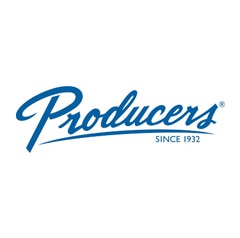
Der Lieferant und Vertreiber von Molkereiprodukten Producers Dairy hat sein 4.645 m² großes Kühllager in seiner Produktionsanlage in Fresno (Kalifornien) mit dem halbautomatischen Pallet-Shuttle-System von Interlake Mecalux ausgestattet. Die Firma hat ihre früheren Palettenregale, die veraltet waren, durch das Pallet-Shuttle-System ersetzt. Dank dieser Lösung hat das Unternehmen die Lagerkapazität verdoppelt und kann jetzt bis zu 300 Aufträge pro Tag zusammenstellen.
Leben ernähren
In den dreißiger Jahren des vorigen Jahrhunderts mussten viele Nordamerikaner aufgrund der Weltwirtschaftskrise auf der Suche nach Gelegenheiten und Arbeit nach Kalifornien ziehen. Damals gründeten vier ehrgeizige Unternehmer Producers Diary Inc. Im Frühjahr 1949 erwarb Larry Shehadey eine Mehrheitsbeteiligung an dem Unternehmen, das auch heute noch wie ein Familienunternehmen geführt wird.
Zurzeit besitzt die Firma zwei Produktionsstätten in Kalifornien, eine in Nevada und eine in Oregon. Die größere Produktionsstätte in Fresno, Kalifornien ist 12.541 m² groß. Dort werden alle Arten von Milchprodukten, wie Milch und Speiseeis sowie auch Orangen- oder Apfelsäfte abgefüllt.
Neues Palettenlagersystem
Aufgrund des Alters der bestehenden Regale erkannte das Unternehmen, dass es ein neues Lagersystem für sein 4.645 m² großes Kühllager in seiner Anlage in Fresno anschaffen musste. „Die Betriebstauglichkeit der Regale verringerte sich zunehmend, daher suchten wir ein effizienteres Lagersystem als Ersatz“, sagt Mike Ramirez, Leiter der Produktionsanlage von Producers Dairy.
Die Situation war so kritisch, dass das Unternehmen zusehends an Lagerkapazität verlor: „Es war sogar soweit gekommen, dass wir die beiden oberen Ebenen der Regale nicht mehr nutzten. Infolgedessen blieben uns nur 180 Lagerpositionen zur Lagerung der Paletten“, fügt Ramirez hinzu.
Daraufhin griffen Interlake Mecalux und sein Partner PacVS ein. „Sie schlugen uns das Pallet-Shuttle-System von Interlake Mecalux vor, ein System, das sich vollständig an unseren Ablauf anpasste“, erläutert Ramirez. Dieses Kompaktlagersystem nutzt ein Shuttle mit Elektromotor, das sich durch das Innere der Lagerkanäle bewegt.
Mithilfe des Shuttles hat das Unternehmen die Zeiten für die Wareneingänge und -ausgänge erheblich verkürzt. Außerdem können die Lagerarbeiter die 150 Artikelarten mit diesem Lagersystem korrekt gruppieren (jeder Kanal entspricht einem anderen Artikel). Das Pallet-Shuttle-System löste ebenfalls die Probleme hinsichtlich der Lagerkapazität von Producers Dairy, da es Platz für 370 Paletten bietet (mehr als doppelt so viele wie die zuvor gelagerten 180 Paletten). Die Regale sind 7 m hoch, haben vier Ebenen und verfügen über fünf motorisierte Shuttles zur Lagerung der amerikanischen Paletten (1.000 x 1.200 mm), mit denen das Unternehmen arbeitet. Die motorisierten Shuttle befolgen die Anweisungen, die sie von den Lagerarbeitern über ein Tablet mit WLAN-Verbindung erhalten, das speziell für die Arbeit in niedrigen Temperaturen konzipiert ist (das Kühllager von Producers Dairy arbeitet bei einer Temperatur von 4 ºC). Das Pallet-Shuttle-System ist die perfekte Lösung zur Handhabung von Produkten, die bei niedrigen Temperaturen gelagert werden müssen, da es die Lagerfläche nutzt und die für die Handhabung der Ware erforderliche Zeit verringert. Da jetzt keine Gabelstapler mehr im Inneren der Lagergassen fahren müssen, werden die Lagerkapazität erhöht (die Regale können tiefer sein) und das Risiko möglicher Unfälle verringert.
Der Lagerarbeiter platziert das motorisierte Shuttle mit einem Gabelstapler in den Kanal, in dem die Palette gelagert werden soll. Anschließend setzt er die Palette am Eingang dieses Kanals auf den Schienen ab (lediglich die Gabeln des Gabelstaplers fahren in die Regalstruktur ein, um die Ware zu platzieren und zu entnehmen). Daraufhin hebt das motorisierte Shuttle die Palette etwas an und bewegt diese dann horizontal bis zur tiefsten freien Lagerposition. Dann fährt das motorisierte Shuttle zum Kanaleingang zurück, um die gleiche Bewegung mit der folgenden Palette zu wiederholen. Diese Folge wiederholt sich so viele Male, bis der Kanal vollständig beladen ist. Bevor die letzte Position des Kanals befüllt wird, holt der Lagerarbeiter das elektrische Shuttle zurück und wiederholt die Sequenz im folgenden Kanal, in dem gearbeitet werden soll.
Das Pallet-Shuttle-System ist eine ideale Lösung für Unternehmen mit einer großen Anzahl von Paletten pro Artikelart und einem hohen Warenumschlag (mit zahlreichen Ein- und Ausgängen desselben Produkts). Producers Dairy nutzt dieses Lagersystem in seinem Kühllager zur Lagerung der Produkte für eine sehr kurze Zeit. „In unserer Anlage füllen wir verarbeitete Milchprodukte ab. Sie werden auf einer Palette gruppiert und mit dem Pallet Shuttle für etwa 24 Stunden gelagert“, erklärt Ramirez. „Anschließend werden sie in einen Lastwagen geladen und an die Kunden geliefert.“ Das Unternehmen lädt täglich zwischen 50 und 70 Lastwagen mit jeweils etwa drei oder vier Aufträgen (insgesamt werden pro Tag etwa 300 Aufträge verteilt).
Zusätzliche Probleme gelöst
Das Pallet-Shuttle-System von Interlake Mecalux hat nicht nur den Kapazitätsmangel im Kühlhaus von Producers Dairy behoben, sondern auch weitere Vorteile gebracht. Einerseits hat es die Dienstleistungskosten des Unternehmens gesenkt, da erhebliche Einsparungen beim Energieverbrauch zur Kälteerzeugung erzielt werden konnten (die Kälte wird über eine größeren Anzahl von gelagerten Paletten verteilt). Andererseits ist das motorisierte Shuttle mit Lithiumbatterien ausgestattet, die in einem breiten Temperaturbereich funktionieren, ohne dass der Akku beschädigt oder die Nutzungsdauer verkürzt wird. Das Pallet-Shuttle-System kann auch eine große Menge von Waren sammeln, damit das Unternehmen über Produkte zur Versorgung seiner Kunden verfügt für den Fall, dass der Betrieb einer Produktionslinie zur Durchführung von Wartungsarbeiten unterbrochen werden muss. „Wenn ein unerwarteter Zwischenfall unsere Produktion unterbricht, verfügen wir über die notwendige, ordnungsgemäß organisierte Ware, um unseren Betrieb aufrechtzuerhalten“, sagt Ramirez. „Dies war früher nicht möglich und ist vermutlich eine der positivsten Verbesserungen für unser Geschäft.“
Erweiterungspläne
Das Projekt war derart erfolgreich, dass Producers Dairy plant die Regale mit dem Pallet Shuttle in Zukunft zu erweitern. „Unser Raum ist sehr begrenzt, daher mussten wir die neuen Regale auf der Grundlage der Abmessungen der alten Regale installieren“, erklärt Ramirez. „Wir würden auch gerne die Kühlkammer erweitern. Dazu müssen wir die an die Regale angrenzende Wand abreißen und Raum gewinnen, den wir zur Erweiterung der Lagerkapazität nutzen werden.“
Wenn ein unerwarteter Zwischenfall unsere Produktion unterbricht, verfügen wir über die notwendige, ordnungsgemäß organisierte Ware, um unseren Betrieb fortzusetzen.“ Dies war früher nicht möglich und ist vermutlich einer der positivsten Verbesserungen für unser Geschäft.
Vorteile für Producers Dairy
- Doppelte Lagerkapazität: Durch Ersetzen der herkömmlichen Palettenregale durch das halbautomatische Pallet-Shuttle-System kann Producers Dairy statt 180 Paletten jetzt 360 Paletten in demselben Raum unterbringen.
- Energieersparnis: Die mit dem Pallet Shuttle ausgestatteten Regale sorgen für eine erhebliche Reduzierung des Energieverbrauchs zur Kälteerzeugung.
- Größere Flexibilität: Producers Dairy verfügt über gelagerte Ware für eine ununterbrochene Lieferung an seine Kunden, selbst im Falle, dass eine der Produktionslinien für Wartungsarbeiten angehalten werden muss.
Galerie
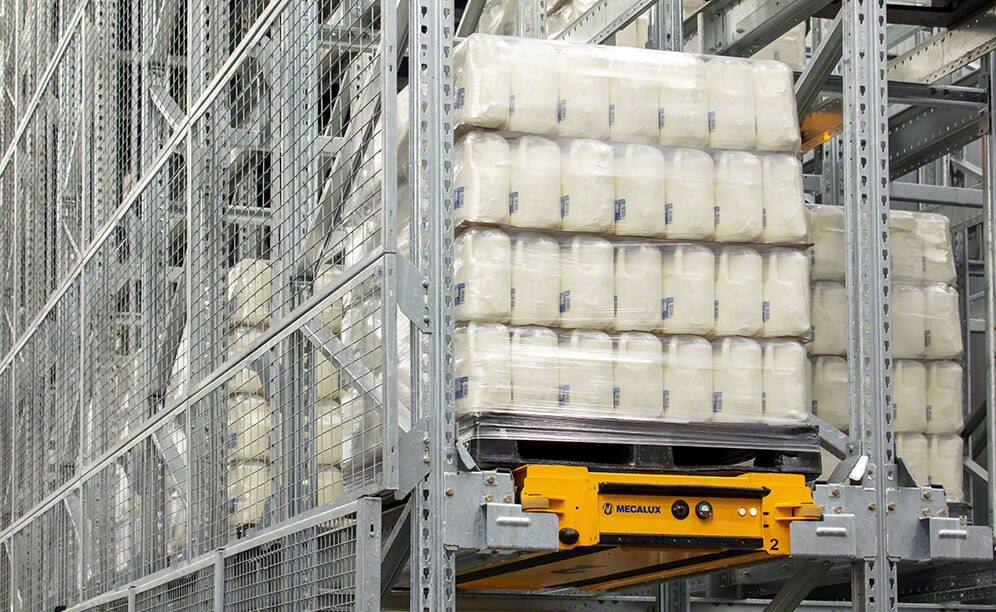
Producers Dairy hat sein Lager mit dem Pallet-Shuttle-System erneuert
Fragen Sie einen Experten