
Das Lebensmittelunternehmen Grupo Siro hat seine Kapazität und Produktivität mit einem 35,5 m hohen automatisierten Lager in Silobauweise erweitert
Durch das Lager in Silobauweise wächst Grupo Siro weiter
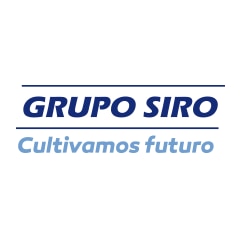
Mecalux hat ein großes vollautomatisches selbsttragendes Lager für Grupo Siro gebaut, eines der größten Lebensmittelunternehmen Spaniens. Dieses innovative Logistikzentrum ist ein Bestandteil der Ausrichtung von Grupo Siro auf wirksame Lösungen für seine Bedürfnisse und auf neue Technologien als Quelle für Effizienz und nachhaltiges Wachstum.
Informationen über Grupo Siro
Grupo Siro ist einer der wichtigsten Hersteller Spaniens von Keksen, Nudeln, Toastbrot, Gebäck und Cerealien. Die Gruppe wurde 1991 mit dem Erwerb von Galletas Siro von Danone gegründet und hat seitdem stets auf Innovation und die Nutzung der Technologie bei allen Betriebsabläufen gesetzt, mit dem Ziel, hochqualitative Produkte zu einem günstigen Preis zu liefern.
Derzeit werden über 300 verschiedene Produkte hergestellt. Die Firma verfügt über 13 Produktionszentren, ein Logistiklager, ein Zentrum für Forschung, Entwicklung und Innovation, ein Zentrum zur Verwertung von Nebenprodukten, zwei Bürozentren und den Sitz der Stiftung Grupo Siro.
Anforderungen des Kunden
In den letzten Jahren konnte die Firma ein hohes Wachstum verzeichnen, insbesondere durch die große Nachfrage ihres Hauptkunden, der Supermarktkette Mercadona. Zu einem bestimmten Zeitpunkt führten dieses Wachstum und die damit einhergehende Zunahme der Produktion zu einem vermehrten Platzbedarf in den Lagern, die im Allgemeinen in den Fabriken selbst untergebracht waren. Um das Produktionstempo aufrecht zu erhalten, entschied sich die Firma zunächst für Verträge mit externen Lagern, dies erschwerte jedoch die Koordination ihrer Logistikkette und erhöhte die Betriebskosten. Grupo Siro war entschlossen, auf wirksame Lösungen für seine Bedürfnisse zu setzen und sein Wachstum zu fördern, und beauftragte daher Mecalux mit dem Bau eines neuen Logistikzentrums an seinem Hauptsitz in Venta de Baños (Palencia). Dabei stellte sie zwei klare Vorbedingungen: die Lagerkapazität in ihren Fabriken zu erhöhen und die Effizienz und Produktivität der Firma zu fördern.
Die vorgeschlagene Lösung
Die technische Abteilung von Mecalux analysierte in Zusammenarbeit mit dem Logistikteam von Grupo Siro gründlich die Bedürfnisse, Voraussetzungen und Möglichkeiten, bis schließlich die ideale Lösung gefunden war: der Bau eines 36 m hohen selbsttragenden Lagers, das durch Regalbediengeräte und Fördervorrichtungen bedient wird, die von der Lagerverwaltungssoftware Easy WMS von Mecalux gesteuert werden. Das Logistikzentrum ist strategisch günstig gelegen, denn innerhalb eines Kreises mit einem Radius von 3 km befinden sich vier seiner wichtigsten Fabriken, drei andere sind weniger als 100 km entfernt, was den Transport der Waren zwischen den Fabriken und dem Logistikzentrum erleichtert und beschleunigt. Es findet ein sehr intensiver und kontinuierlicher Fluss an Warenbewegungen statt, daher wurden an einer Seite des Lagers zwei Wareneingangsrampen, getrennt von den neun Versandrampen, eingerichtet, damit sich die beiden Vorgänge nicht gegenseitig stören. Es wurde genügend Platz vorgesehen, um die Dynamik der Bewegungen bei Transportmanövern und beim Warten auf die Lastwagen zu erhöhen.
Das an das Lager angrenzende Gebäude besteht aus zwei verschiedenen Ebenen, um die verschiedenen Abläufe, die dort stattfinden, optimal zu organisieren:
- Die untere Ebene ist hauptsächlich für den Wareneingang und den Warenversand bestimmt und verfügt über einen großen Konsolidierungsbereich auf dem Boden.
- Auf der oberen Ebene werden die Paletten, die von den Laderampen der unteren Ebene kommen, in das Lager gebracht. Außerdem gibt es einen Bereich für die Kommissionierung.
Das Lager
Die Abmessungen des Lagers sind beträchtlich: 102 m Länge, 57 m Breite und 35,5 m Höhe, das Maximum, das die örtlichen Bauvorschriften erlauben. Es wird durch acht Gänge mit beidseitigen Regalanlagen doppelter Tiefe unterteilt, die jeweils über 14 Ladeebenen verschiedener Höhe verfügen, die an die von Grupo Siro verwendeten Paletten angepasst sind: fünf Ebenen für Europaletten mit 1400 mm Höhe, acht mit 2000 mm und eine mit 2500 mm. Die Ladeeinheiten wiegen durchschnittlich 800 kg und haben ein Höchstgewicht von 1000 kg.
In jedem Gang befindet sich ein Zweimast-Regalbediengerät mit Teleskopgabel und einer im Schlitten angebrachten Wartungskabine. Dieses Gerät ist dazu bestimmt, jede Palette an den ihr zugewiesenen Platz zu bringen, abhängig von Größe und Umschlagshäufigkeit.
Die Automatisierung des Lagers wird durch zwei Förderkreisläufe vervollständigt: einen auf der unteren Ebene, wo die für den Versand bestimmten Paletten abgesetzt werden, und einen weiteren auf der oberen Ebene, in 6,7 m Höhe, der alle Eingänge sowie die Ausgänge mit dem Kommissionierbereich verbindet.
Im oberen Teil des Lagers wurde der freie Raum zwischen den Dachbindern dazu genutzt, die Rohre der Klimaanlage, die die Temperatur der gesamten Installation regeln und die Luft ordnungsgemäß verteilen, unterzubringen.
Im hinteren Außenbereich des Lagers wurden vier Pumpanlagen für das Brandschutzsystem und ein Wassertank mit ausreichendem Fassungsvermögen für die Abmessungen des Lagers aufgestellt. Im Inneren befinden sich die Sprinkler und Brandmelder, die jede Möglichkeit eines Brandes verhindern.
Die untere Ebene
Aufteilung der unteren Ebene:
- Vollautomatische Entladerampe
- Herkömmliche Entladerampe
- Laderampen (insgesamt 9)
- Bereich für die Eingangskontrolle von Paletten sowie Lastenaufzug
- Ausgang der Paletten aus dem Lager
- Konsolidierung auf dem Boden
- Virtueller Kreislauf für LGV-Stapler
- Sammelplatz für leere Paletten
- Empfang und Aufbereitung der Eingangspaletten
Wareneingang
Der Eingang der Waren, die aus den nächstgelegenen Produktionszentren eintreffen, erfolgt an den zwei Eingangsrampen. An einer wird die Entladung aus den Lastwagen automatisch durchgeführt und an der anderen manuell mit Gabelstaplern oder Palettenhubwagen.
Im Entladebereich ist ausreichend Stauraum, um zwei komplette Lastwagen zu entladen, d. h. für insgesamt 66 Paletten, die in den Prüfbereich gebracht werden, wo ihr Zustand beurteilt wird.
Alle Paletten müssen unbedingt den Prüfbereich passieren, wo überprüft wird, ob sie sich in gutem Zustand befinden und ihr Gewicht und ihre Abmessungen den im Lager erforderlichen Qualitätsansprüchen entsprechen.
Wenn die Palette in ordnungsgemäßem Zustand ist, erteilt das Steuerungssystem die Anweisung, sie bis zum Lastenaufzug zu transportieren, der sie zur oberen Ebene befördert, wo sie in das automatische Lager gelangt.
Wenn die Palette die Prüfung nicht besteht, wird sie je nach erkanntem Fehler in verschiedene Bereiche gebracht:
- Aufbereitungsbereich
- Verdichtungsbereich, in dem die Überstände korrigiert werden, die die vorgeschriebenen Grenzwerte überschreiten
- Umsetzbereich:Wenn sich die Ladeeinheiten auf einem ungeeigneten Unterbau befinden, setzt ein Palettenunterleger sie auf eine andere Palette, die in gutem Zustand ist. Diese Paletten kehren anschließend wieder in den Prüfbereich zurück und werden erneut überprüft, bevor sie in die obere Ebene gebracht werden.
Fehlerhafte Paletten, die nicht in Ordnung gebracht werden können, werden zum Ausgangsbereich transportiert und dort aus dem Kreislauf genommen.
Die aufbereiteten Paletten passieren erneut die Prüfstelle, wo nochmals überprüft wird, ob sie die Anforderungen des Lagers erfüllen.
Es muss gewährleistet sein, dass die in das automatische Lager eingebrachte Ware geeignet ist und nicht mehr als vorgesehen übersteht.
Ausgänge aus dem Lager/Versand
Die lasergesteuerten Gabelstapler (LGV) befördern die aus dem Lager kommenden Paletten. Sie holen sie an den Ausgangspunkten jedes Lagergangs ab und bringen sie in den zugewiesenen Wartebereich (eine der neun Laderampen). Dabei bewegen sie sich in einem vorprogrammierten virtuellen Kreislauf.
Der Gabelstapler legt seine Bahn fest, indem er ein Lasersignal aussendet, das von Deflektoren zurückgesandt wird, die sich an Punkten in der Nähe des Streckenverlaufs befinden. Das Verwaltungssystem erfährt so genau seine Position und gibt ihm die Anweisung, zu einer Ladestation zu fahren, wenn die Batterieladung einen festgelegten Wert erreicht hat. Da es sich um eine vollautomatische Verbindung handelt, ist bei diesem Vorgang kein menschlicher Eingriff erforderlich.
Nur die Beladung der Lastwagen wird von Lagerarbeitern durchgeführt, die die Ware mithilfe von Palettenhubwagen in den von der Lagerverwaltungssoftware je nach Auftragsnummer, Versandroute, Kunden usw. zugewiesenen Lastwagen bringen.
Die Mitarbeiter bestätigen jeden Vorgang und die Ausführung der Anweisungen über ein Funkterminals.
Die obere Ebene
Lagereingang
Die von den Eingangsrampen kommende Ware wird nach dem Passieren des Prüfbereichs von einem Lastenaufzug zur oberen Ebene befördert.
Dort verteilt ein Hauptförderer die Artikelarten über die Eingangsförderer in die verschiedenen Lagergänge. Über diesen Kreislauf, der nur in einer Richtung läuft, werden auch die Paletten befördert, die aus den Gängen kommen und in die Kommissionierbereiche gebracht werden.
Aufteilung der oberen Ebene:
- Lastenaufzug
- Innerer Kreislauf des Lagers
- Eingangs- bzw.Ausgangsförderer jedes Gangs
- Verfahrwagen des Kommissionierbereichs
- Kommissionierstellen
- Verpackungs- und Aufbereitungsbereich
- Hauptförderer für den Lagereingang
Kommissionierbereich
Außerdem wurden zwei nebeneinanderliegende Kommissionierstellen eingerichtet, an denen jeder Kommissionierer zwei Aufträge gleichzeitig zusammenstellen kann. Der Bereich ist auf eine zukünftige Erweiterung vorbereitet, falls die Bedürfnisse von Grupo Siro dies erforderlich machen. Die Kommissionierstellen befinden sich über den Fördervorrichtungen. Auf beiden Seiten neben dem Kommissionierer befinden sich hydraulische Hubtische, die sich auf eine ergonomische Höhe zur Handhabung der Ware einstellen lassen. So wird die Auftragszusammenstellung erheblich beschleunigt. Zu jeder Kommissionierstelle gehört ein Kreislauf mit Staufunktion. Es sind ebenfalls Stapelgeräte und Dosiergeräte für Paletten vorhanden, die den Bereich versorgen, sowie Warteplätze für Paletten, die das Lager verlassen haben und für die noch kein freier Platz im Kreislauf der ihnen zugewiesenen Stelle vorhanden ist.
Nach Zusammenstellung des Auftrags wird die Palette in den Förderkreislauf gebracht, der sie nach Passieren der Packmaschine wieder ins Lager zurückbringt, bis das Verwaltungssystem ihren Versand anordnet.
Die Software
Das Lager wird durch die Software Easy WMS von Mecalux verwaltet und kommuniziert ständig mit dem Ressourcenplanungssystem der Grupo Siro, mit dem Ziel, alle logistischen Prozesse und die im Lager durchgeführten Abläufe zu steuern, zu koordinieren und darüber zu informieren.
Die Software ist so konzipiert, dass sie praktisch und einsatzfähig ist und daneben die folgenden Funktionen durchführt:
- Absolute Kontrolle der Lagerverwaltung.
- Verwaltung der Warenein- und -ausgänge an den Ent- und Beladerampen.
- Strategische Einlagerung der Ladeeinheiten in das Lager mit Kontrolle der Gänge und der Lagerpositionen.
- Registrierung und Anpassung der Lagerbestände in Echtzeit.
- Festlegung der Reihenfolge der Entnahme der Ware und anschließende Beladung des Lastwagens mithilfe eines Funkterminals.
- Optimierung der Aufgaben abhängig vom Kommissionierungsweg.
- Direkte Kommunikation mit dem Logistikanbieter von Grupo Siro.
- Koordination aller Stammdaten (Artikel, Eigentümer, Lieferanten, Kunden usw.).
Vorteile für Grupo Siro
- Ersparnis bei den Betriebskosten: Die Abschaffung der externen Lager und die Zentralisierung der Abläufe im selben Logistikzentrum führt zu einer Zunahme der Produktivität und einer schnellen Kapitalrendite.
- Maximale Lagerkapazität: Durch die große Höhe des Lagers und den Einsatz von Regalbediengeräten war es möglich, die Lagerkapazität von Grupo Siro zu vervielfachen und sich so an das Wachstum der Produktion anzupassen.
- Vollautomatische Verwaltung: Grupo Siro hat die Abläufe von Eingang, Einlagerung, Kommissionierung und Versand der Ware an einer einzigen Stelle integriert und koordiniert, verwaltet und gesteuert von Easy WMS, und so die Leistung seiner gesamten Logistikkette optimiert.
- Verbesserung der Sicherheit: Automatische Lager bieten einen maximalen Schutz für die Lagerarbeiter und die Ware und tragen so zum Ziel des Unternehmens bei, effiziente Vorgänge zu fördern, die jederzeit die Sicherheit der Mitarbeiter gewährleisten.
Automatische Logistikzentrum von Grupo Siro | |
---|---|
Gesamtkapazität: | 40.320 Paletten |
Palettenabmessungen: | 800 x 1200 x 1400 / 2000 / 2500 mm |
Maximalgewicht der Palette: | 1000 kg |
Anzahl Regale: | 16, mit doppelter Tiefe |
Anzahl Gänge: | 8 |
Anzahl der Regalbediengeräte: | 8 |
Anzahl Ladeebenen: | 14 |
Länge des Lagers: | 101 m |
Breite des Lagers: | 57 m |
Höhe des Lagers: | 33,5 m |
Galerie

Mecalux hat ein großes vollautomatisches selbsttragendes Lager für Grupo Siro gebaut
Fragen Sie einen Experten