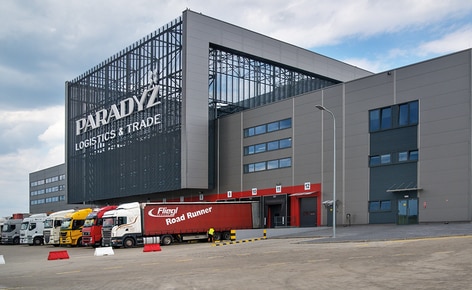
Ceramika Paradyż verstärkt seinen Einsatz in Sachen Spitzentechnologie mit einem neuen automatisierten Hochregallager (Silobauweise) in Polen
Hohe Kapazitäts- und Kommissioniergeschwindigkeiten im vollautomatischen Hochregallager von Ceramika Paradyż
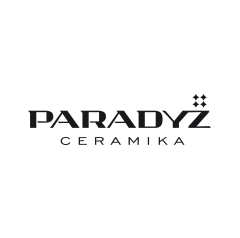
Mecalux hat für Ceramika Paradyż ein automatisches Hochregallager in Silobauweise mit einer Lagerkapazität für über 20.200 Paletten in Tomaszów Mazowiecki (Polen) entworfen. Am Regaleingang des Lagers gibt es ein zweistöckiges Gebäude, das es ermöglicht, den Warenein- und -ausgang auf effiziente Weise zu organisieren und gleichzeitig die Auftragszusammenstellung zu beschleunigen. Im Lieferumfang ist ebenfalls die Lagerverwaltungssoftware Easy WMS von Mecalux enthalten.
Bedürfnisse von Ceramika Paradyż
Ceramika Paradyż ist ein wichtiger polnischer Keramikhersteller, der seine Produkte in über 50 Länder auf der ganzen Welt exportiert. Das Unternehmen ist dafür bekannt, die neueste Technologie für alle seine Produktionsprozesse einzuführen, um innovative Produkte von höchster Qualität anbieten zu können.
Im Hinblick auf eine zukünftige Steigerung seines Wachstumstempos beauftragte es Mecalux mit dem Bau eines automatischen Lagers mit hoher Kapazität, das auch über einen Kommissionierbereich verfügt, in dem die Aufträge schnell zusammengestellt werden können.
Lösung von Mecalux
Nach gründlicher Analyse der Bedürfnisse von Ceramika Paradyż hat das technische Team von Mecalux ein automatisches Hochregallager in Silobauweise entworfen und gebaut, das den Anforderungen der Firma genau entspricht.
Das Lager ist 25 m hoch, 97 m lang und 35 m breit und besteht aus acht Gängen mit Regalanlagen einfacher Tiefe auf beiden Seiten.
Mit dieser Lösung hat das Unternehmen die notwendige Lagerkapazität erreicht, um seinen Markt beliefern zu können, der sich vor allem in Europa befindet.
Neben dem Lager wurde ein niedrigeres Gebäude mit zwei Ebenen errichtet, in dem andere Vorgänge ablaufen.
Auf der unteren Ebene erfolgen die Warenein- und -ausgänge. Es wurden Prüfstellen, ein Palettenunterleger und ein Ausgabegerät für leere Paletten sowie Kanäle zur Ladevorbereitung installiert.
Auf der oberen Ebene werden die Aufträge zusammengestellt. Dort wurde ein ganzer Bereich mit einem Kreislauf von Elektroführungen, Verfahrwagen, Kommissionierstellen, Palettenpuffer und einer Zone zur Konsolidierung und Verpackung eingerichtet.
Das Lager
Das 3290 m2 große Lager besteht aus acht Gängen mit Regalanlagen einfacher Tiefe auf beiden Seiten. In der Länge sind insgesamt 45 Module mit 14 Ebenen in der Höhe vorhanden, die jeweils zwei Paletten aufnehmen können.
Die Artikelarten werden in den entsprechenden Positionen je nach Rotation (A, B und C) gelagert, was es ermöglicht, die Bewegungen der Fördermittel zu optimieren.
Da es sich um eine selbsttragende Konstruktion handelt, muss das Regalsystem sein Eigengewicht und das Gewicht der Ware tragen, ebenso wie das Gewicht der senkrechten Verkleidungen und des Daches. Beim Entwurf wurden außerdem noch weitere Faktoren berücksichtigt, die auf die Struktur einwirken, wie die Windkraft, die Erdbebengefahr in der Region und die örtlich gültigen Bauvorschriften.
Lagerein- und -ausgangDas Lager verfügt über zwei Ebenen für den Eingang und Ausgang der Ware. Die untere liegt auf der gleichen Höhe wie das Erdgeschoss des angrenzenden Gebäudes. Sie ist für den Wareneingang aus dem Produktionszentrum sowie den Ausgang kompletter Paletten und fertig zusammengestellter Aufträge in den Versandbereich bestimmt.
Auf der oberen Ebene, die auch mit der oberen Ebene des angrenzenden Gebäudes übereinstimmt, erfolgt der Ausgang der für die Kommissionierung benötigten Paletten und der Eingang der fertiggestellten Aufträge.
In jedem Gang bewegen die Regalbediengeräte die Ware von den Eingangs- und Ausgangsstellen auf beiden Ebenen zu den Positionen in der Regalanlage, die von der Lagerverwaltungssoftware Easy WMS zugewiesen wurde.
Bei diesen Geräten handelt es sich um Einmast-Geräte des Modells MT3, die mit einer Seitwärtsgeschwindigkeit von 220 m/Min und einer Hubgeschwindigkeit von 54–66 m/Min. arbeiten.
Obere Ebene: KommissionierbereichDie gesamte obere Ebene des an das Lager angrenzenden Gebäudes dient zur Auftragszusammenstellung. Dieser weiträumige Bereich besteht aus sechs Kommissionierstellen und könnte in der Zukunft noch vier weitere aufnehmen, abhängig von der Nachfrage und den Logistikanforderungen von Ceramika Paradyż.
Um die Arbeit der Kommissionierer zu erleichtern, verfügen diese über Hilfsmittel, wie Hubtische, die sich auf eine ergonomisch korrekte Höhe anheben lassen, und Saugheber für Behälter, um schwere Lasten zu bewegen.
Die korrekte Organisation und die Einbeziehung der automatischen Geräte sind unerlässlich, um die erforderliche Zykluszahl und die optimale Durchführung der Kommissionierung zu gewährleisten. Die Elektroführungen holen die aus dem Lager kommenden Paletten direkt an den Ausgangsstellen ab und setzen sie auf einen der vier Eingangsförderer dieses Bereichs.
Zwei doppelte Verfahrwagen organisieren diesen Bereich und verteilen die Paletten zwischen den Eingangsförderern, den Wartestationen und den Kommissionierstellen. Die Ursprungspaletten, die bereits zur Kommissionierung verwendet wurden, gelangen auf dem selben Weg, aber in umgekehrter Richtung, wieder ins Lager zurück.
Um unnötige Bewegungen der Regalbediengeräte und den ständigen Warenein- und -ausgang auf dieser Ebene zu vermeiden, wurde ein Pufferbereich mit 120 Positionen für Paletten mit hoher Rotation eingerichtet, die in Wartestellung verbleiben und ebenfalls von zwei Verfahrwagen bedient werden.
Zwei weitere Verfahrwagen dienen dazu, die Kommissionierstellen mit leeren Paletten zu versorgen und die fertigen Bestellungen abzuholen. Anschließend setzen sie diese auf die Fördervorrichtungen, die mit den Elektroführungen verbunden sind. Mit ihnen werden sie in den an einer Seitenwand gelegenen Konsolidierungsbereich gebracht.
Neben dem Konsolidierungsbereich wurde eine Regalanlage für die manuelle Kommissionierung installiert, wo die Bestellungen ggf. durch erforderliche Zubehörteile ergänzt werden.
Nach der Fertigstellung der Aufträge werden die Paletten zur Packmaschine transportiert. Anschließend wartet die Ware darauf, zum gegebenen Zeitpunkt zur Ladevorbereitung gebracht zu werden.
Automatische KommunikationDie verschiedenen Bereiche der Kommissionierebene sind auf automatische Weise mithilfe des Elektroführungskreislaufs und der Verfahrwagen miteinander verbunden.
Die Verfahrwagen, deren Aufgabe darin besteht, die verschiedenen Stationen und die Stationen zur Auftragszusammenstellung in gerader Linie miteinander zu verbinden, sind in den Kommissionierbereich integriert.
Ihr großer Vorteil besteht darin, dass sie sich in beiden Richtungen bewegen und verschiedene Stationen miteinander verbinden können. Sie bewegen sich auf Schienen mit einer Geschwindigkeit von 120 m/min. und besitzen Ketten- und Rollenförderer sowie Teleskopgabeln, um die Paletten zu bewegen.
Die Elektroführungen bewegen sich in einem geschlossenen Kreislauf innerhalb des Kommissionierbereichs und verbinden diesen Bereich mit dem Lagerein- und -ausgang und der Konsolidierung.
Die Elektroführung wurde gewählt, weil es sich hierbei um ein flexibles und schnelles Transportsystem handelt, das einen ständigen Warenfluss gewährleistet. Sie kann Kurven nehmen und es besteht die Möglichkeit, Umleitungen und Querverbindungen zu installieren.
An einer Seite des Kreislaufs wurde ein Instandhaltungsbereich eingerichtet, zu dem die Wagen geleitet werden, wenn ein Eingriff notwendig ist. Da der Boden von Hindernissen frei bleibt, erleichtern die Elektroführungen die Reinigungsarbeiten.
WareneingangsbereichDie untere Ebene des angrenzenden Gebäudes ist folgendermaßen aufgeteilt:
- Eingangsförderer
- Einheit mit Palettenunterlegern und Ausgabegeräten für leere Paletten
- Prüfstelle für Paletten und Aufbereitung
- Doppelter Rückführungskreislauf und Verbindung mit den Fördervorrichtungen im Lagerinneren
- Kanäle zur Ladevorbereitung
- Palettenentferner und Stapelgerät für leere Paletten
- Verfahrwagen zur Klassifizierung
- Rampen für Entladung und Versand
Die aus der Produktion stammende Ware kommt im Logistikzentrum an den erhöhten Laderampen an. Die Entladung der Lastwagen erfolgt mit Hubwagen, mit deren Hilfe die Paletten direkt in den Eingangskreislauf eingebracht werden können.
In diesem Lager sind die meisten verwendeten Paletten von unzureichender Qualität und die Produkte sind sehr schwer. Daher wurde eine Einheit mit Palettenunterlegern installiert, die die Ware auf Trägerpaletten setzt.
Anschließend durchläuft die Ware die Prüfstelle, die sicherstellt, dass die in der Einrichtung vorhandenen Kriterien erfüllt werden, und wird ins Lager gebracht.
Ausgänge aus dem LagerDie für den Versand bereitstehenden Paletten verlassen das Lager ebenfalls auf der unteren Ebene. Dort werden sie in den Haupt-Förderkreislauf aufgenommen, der sie in den Versandbereich bringt.
Ein doppelter Verfahrwagen transportiert die Paletten mit der Ladung und klassifiziert sie in zwölf Ladevorbereitungskanälen. Diese bestehen aus Kettenförderern und einem Drehtisch an den Enden, der es ermöglicht, die Paletten von der jeweils praktischeren Seite aufzunehmen, abhängig von ihrer Anordnung im Transportfahrzeug. Mithilfe dieses Systems lassen sich die Paletten eines Auftrags oder einer Versandroute gruppieren und der Vorgang der Beladung der Versandfahrzeuge beschleunigen.
Easy WMS von Mecalux
Im Logistikzentrum von Ceramika Paradyż wurde die Lagerverwaltungssoftware Easy WMS von Mecalux installiert, deren Aufgabe darin besteht, den gesamten internen Betriebsablauf zu steuern.
Da es sich um ein vollautomatisches Lager handelt, wurde außerdem das Steuerungsmodul Galileo installiert, das die korrekte Funktion aller vorhandenen sich bewegenden Vorrichtungen gewährleistet und für die Einhaltung der Sicherheitsmaßnahmen zuständig ist.
Easy WMS von Mecalux kommuniziert ständig in beiden Richtungen mit dem ERP von Ceramika Paradyż, wobei beide Systeme Daten und grundlegende Informationen austauschen, um einen effizienten Betrieb und eine effiziente Verwaltung des Lagers zu erreichen und die höchste Rentabilität der logistischen Prozesse zu erzielen.
Vorteile für Ceramika Paradyż
- Maximale Leistung: Das automatische Lager von Ceramika Paradyż gewährleistet einen kontinuierlichen Warenfluss und ein System zur schnellen Auftragszusammenstellung mit minimaler Beteiligung von Lagerarbeitern, wodurch Risiken vermindert werden.
- Große Lagerkapazität: Das Hochregallager in Silobauweise mit einer Fläche von 3290 m2 und einer Höhe von 25 m verfügt über eine Kapazität für 20.200 Paletten mit einem Höchstgewicht von je 1500 kg.
- Effiziente Lagerverwaltung: Die Abläufe im Lager werden gesteuert und organisiert von Easy WMS von Mecalux und der Steuerungssoftware Galileo, die für die Anweisungen zur Bewegung aller Vorrichtungen, aus denen die Einrichtung besteht, verantwortlich ist.
Automatischen Lager von Ceramika Paradyż Sp. z o. o. | |
---|---|
Lagerkapazität: | 20.256 Paletten |
Palettenabmessungen: | 800 x 1200 mm und 800 x 1250 mm |
Maximalgewicht pro Palette: | 1500 kg |
Länge des Lagers: | 97 m |
Breite des Lagers: | 35 m |
Höhe des Lagers: | 25 m |
Anzahl an Lagergängen: | 8 |
Galerie
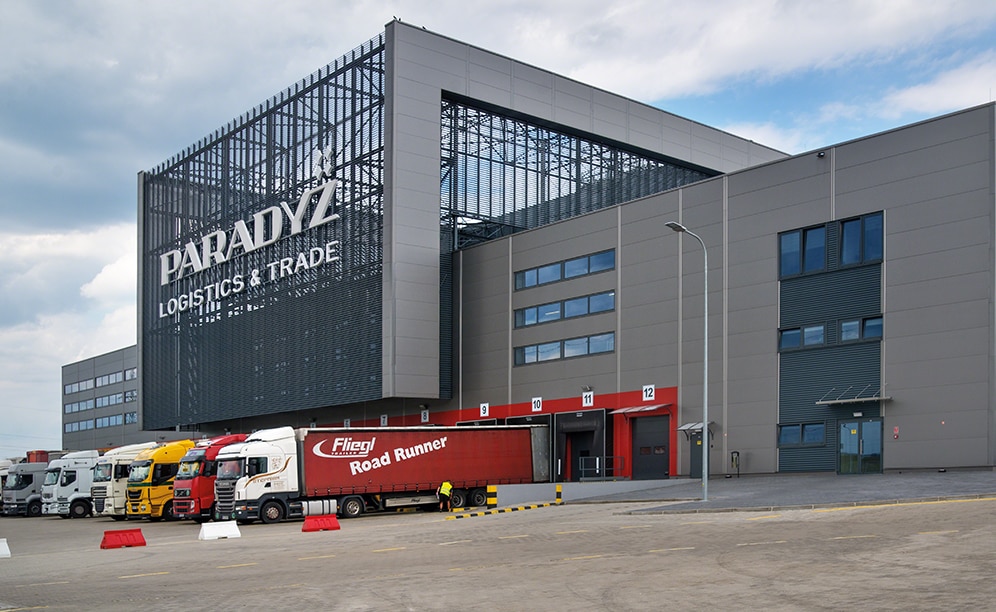
Mecalux hat für Ceramika Paradyż ein automatisches Hochregallager in Silobauweise mit einer Lagerkapazität für über 20.200 Paletten
Fragen Sie einen Experten