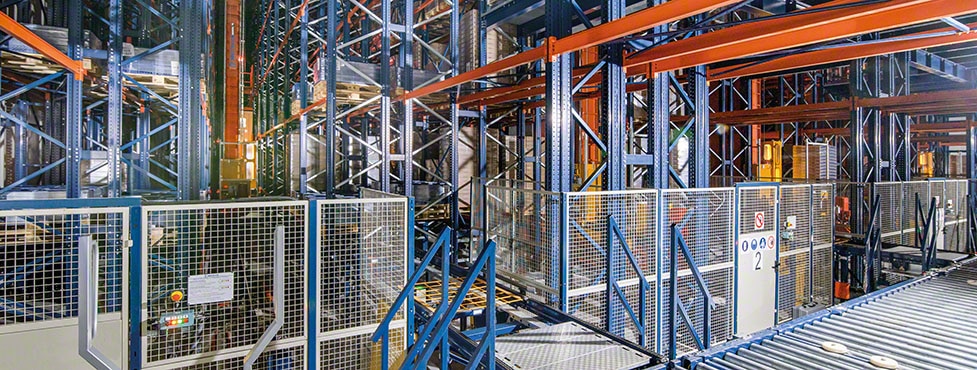
Die Automatisierung im Lager von Lantmännen Unibake, das tägliche Brot
Die Automatisierung der Vorgänge ermöglicht den Versand von ca. 100 Paletten/Stunde an seine Kunden in Polen
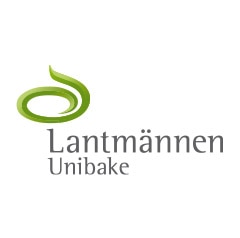
Hinter jedem Laib Brot stecken wichtige logistische Abläufe, die mit maximaler Effizienz durchgeführt werden müssen, um die vom Kunden geforderte Qualität zu erreichen. Lantmännen Unibake, eines der führenden europäischen Bäckereiunternehmen, ist sich dieser Tatsache bewusst und setzt daher auf Technologie, um seine Lieferkette zu verbessern und die Rückverfolgbarkeit der Waren zu gewährleisten. In Nowa Sól (Polen) wurde ein neues Logistikzentrum gebaut, das rund 100 Paletten pro Stunde versenden kann. Das an die Produktion angeschlossene Zentrum verfügt über zwei automatische Lagersysteme, die eine Gesamtlagerkapazität von 15.920 Paletten für gekühlte und gefrorene Produkte bieten.
Tradition und Innovation
Lantmännen Unibake wurde 1880 gegründet und hat seinen Sitz in Kopenhagen, Dänemark. Das Unternehmen ist einer der führenden europäischen Lieferanten von frischen und gefrorenen Teigprodukten für die Herstellung von Bäckerei- und Konditoreiwaren.
Das Unternehmen beliefert Hunderte von Restaurants, Supermärkten, Schnellrestaurants, Tankstellen oder Cateringunternehmen mit dem von den Kunden gewünschten Brot. In den letzten Jahren hat es weltweit expandiert und Produktionsstätten in Belgien, Dänemark, Schweden, Norwegen, Polen, Deutschland, Russland, Finnland, dem Vereinigten Königreich und den Vereinigten Staaten eröffnet.
Derzeit erzielt das Unternehmen einen Jahresumsatz von 1,1 Milliarden Euro, beschäftigt über 6.000 Mitarbeiter und verfügt über 36 Produktionsstätten in 20 Ländern sowie über Verkaufsstellen in weltweit 60 Ländern.
Technologie und Rückverfolgbarkeit
Seit seiner Betriebsaufnahme in Polen in den 1990er Jahren hat das Unternehmen seine Produktionsrate ständig erhöht und in den letzten Jahren die beachtliche Menge von 30.000 Tonnen tiefgefrorenem Brot an Hunderte von Kunden in Polen verkauft.
Um dieser steigenden Nachfrage gerecht zu werden und das Wachstum zu fördern, hat sie in Nowa Sól, einem der am stärksten industrialisierten Gebiete Westpolens, eine neue Produktionsstätte mit einer Fläche von 24.000 m² eröffnet. Dies ist die dritte Produktionsstätte, die Lantmännen Unibake nach Poznań und Nieporęt in Polen gebaut hat und die zweitgrößte in ganz Europa.
„In unserem Logistikzentrum in Nieporęt verwenden wir nichtautomatische Lagersysteme wie Palettenregale, Einfahrregale oder Verschieberegale”, sagt Jerzy Sobieszczuk, Supply Chain Manager bei Lantmännen Unibake in Polen und Ungarn. Zwar, „bewältigten wir einen Fluss von 10 bis 12 Paletten/Stunde, was für unsere Wachstumsaussichten jedoch nicht ausreichend war. Wir mussten uns nach effektiveren Lagersystemen umsehen, weil wir die Zahl der Ein- und Ausgänge erhöhen wollten”, fügt er hinzu.
Das Unternehmen erkannte, dass die Automatisierung die beste Möglichkeit war, um wettbewerbsfähig zu bleiben. Aus diesem Grund hat sie das Lager des Werks in Nowa Sól mit zwei Robotersystemen ausgestattet, eines für die Verwaltung gekühlter Produkte und das andere, in selbsttragender Bauweise, für Tiefkühlprodukte (-28 ºC). Das an die Produktion angeschlossene Lager ist mit der neuesten Technologie ausgestattet, um eine kontrollierte und präzise Warenbewegung zu gewährleisten. Regalbediengeräte, Förderer und Aufzüge übernehmen den Transport der Produkte zwischen den verschiedenen erforderlichen Punkten im Lager, wobei sie 24 Stunden am Tag ununterbrochen in Betrieb sind.
Die Rückverfolgbarkeit ist bei der Verwaltung von Lebensmitteln wie denen von Lantmännen Unibake von entscheidender Bedeutung. Die Rückverfolgung der Waren durch alle Produktionsstufen und innerhalb der Lieferkette ist notwendig, um die beste Produktqualität zu gewährleisten.
Ankunft der Waren
Das Logistikzentrum befindet sich direkt neben den Produktionslinien, wobei beide Gebäude durch einen Förderkreislauf miteinander verbunden sind.
Die Förderer transportieren die palettierten Waren in den Lagerbereich und durchqueren dort eine Palettenkontrollstation, wo ihre Eigenschaften überprüft und die Einhaltung bestimmter, festgelegter und erforderlicher Parameter, hauptsächlich ihr Gewicht und ihre Abmessungen, kontrolliert werden. Anschließend entscheidet das Lagerverwaltungssystem (LVS), ob sie im Kühl- oder Tiefkühlbereich gelagert wird, und weist ihr einen Stellplatz zu.
Laut Jerzy Sobieszczuk „ist die Produktionskapazität einer einzelnen Produktionslinie im neuen Werk in Nowa Sól größer als die der gesamten Produktionsstätte in Nieporęt“.
Es wurde ebenfalls ein Eingang für Produkte aus anderen Produktionsstätten von Lantmännen Unibake eingerichtet. Dieser befindet sich direkt neben den Laderampen und ist, wie der Eingang aus der Produktion, mit hydraulischen Tischen und einer Kontrollstation ausgestattet, die die Paletten durchlaufen, bevor sie in den Regalen eingelagert werden.
Ein Lager, zwei automatische Systeme
Die Lagerfläche für Tiefkühlprodukte (-28 ºC) ist als selbsttragende Konstruktion gebaut und nimmt eine Fläche von 2.625 m 2.625 m² ein. Bei dieser Art von Konstruktion tragen die Regale nicht nur die Ladeeinheiten, sondern auch den Rest des Gebäudes, da das Dach und die Seitenwände daran befestigt sind. Diese Bauweise optimiert sowohl die verfügbare Fläche als auch die verfügbare Höhe, um die größtmögliche Lagerkapazität zu erreichen.
Dieser Bereich verfügt über fünf Gänge mit Regalen doppelter Tiefe auf beiden Seiten und bietet Platz für 15.120 Paletten, hauptsächlich mit gefrorenem Brot. Das Unternehmen entschied sich für diese Lösung, da die 40 m hohen Regale mit doppelter Tiefe die Kosten für den Energieverbrauch senken. Je mehr Raum beansprucht wird, desto weniger Volumen muss gekühlt werden.
In jedem Gang bewegt sich ein Regalbediengerät, das mit Teleskopgabeln ausgestattet ist, um die Paletten in der am weitesten entfernten Position zu erreichen, mit einer Geschwindigkeit von 220 m/min.
Direkt vor und innerhalb des Gebäudes gibt es einen weiteren automatischen Lagergang von geringerer Höhe (18,5 m), der bei einer Kühltemperatur (zwischen 4 und 15 ºC) betrieben wird. Er besteht aus einem einzigen Gang mit Regalen doppelter Tiefe, die eine Kapazität von 800 Paletten mit frischen Produkten aufweisen.
Jerzy Sobieszczuk - Supply Chain Manager bei Lantmännen Unibake in Polen und Ungarn
„Wir haben uns nach Prüfung und Bewertung verschiedener Angebote für Mecalux entschieden. Von vornherein wurde uns mitgeteilt, dass einige Monate Testphase erforderlich seien, um die Inbetriebnahme der Anlage sicherzustellen. Im Falle unseres Lagers wurde der Prozess jedoch relativ schnell durchgeführt. Wir haben Anfang Mai 2019 mit den Tests begonnen, und Ende August wurden die letzten Tests durchgeführt. Derzeit sind wir mit dem Betrieb des Lagers sehr zufrieden, da es reibungslos funktioniert und seine geplanten Funktionen einwandfrei erfüllt”.
Reihenfolge beim Versand
Der Regaleingang der beiden automatischen Systeme, der aus einem Förderkreislauf besteht, ist auf zwei Ebenen verteilt, auf denen verschiedene Vorgänge ausgeführt werden. Auf der unteren Ebene befinden sich sowohl der Ein- und Ausgang des Kühlbereichs als auch der Ausgang für den Versand aus der Gefrierkammer. Auf der oberen Ebene erfolgt der Eingang der Waren aus der Produktion in die Gefrierkammer.
„Das Werk in Nowa Sól verfügt über einen weitläufigen Versandbereich, in dem wir in jeder Schicht (8 Stunden) zwischen 12 und 18 LKWs beladen, was ungefähr 600 Paletten entspricht. Unser Ziel ist es, diese Zahl in Zukunft zu erhöhen”, erläutert Jerzy Sobieszczuk. Der Bereich besteht aus drei Gruppen von drei Kanälen zur Ladungsvorbereitung und einer Kapazität von elf Paletten pro Kanal. Insgesamt umfasst jede Gruppe von Kanälen bis zu 33 Paletten, was der vollen Kapazität eines Lastwagens entspricht.
Ein Lager für Gegenwart und Zukunft
Lantmännen Unibake hat seine Logistik automatisiert, um die Abläufe bei Lagerung, Zusammenstellung und Versand von Waren aus seinem Werk in Nowa Sól (Polen) zu beschleunigen und zu optimieren. Die Technologie hat ebenfalls dazu beigetragen, eine vollständige Rückverfolgbarkeit der Waren zu erreichen.
Die Automatisierung hat dem Unternehmen zahlreiche Vorteile gebracht, wie z.B. geringere Betriebskosten, Schnelligkeit bei der Warenverwaltung, Produktkontrolle, verbesserte Hygiene in der Anlage usw. Kurz gesagt, eine beträchtliche Steigerung der Produktivität.
Das Lager ist außerdem für das zukünftige Wachstum des Unternehmens vorbereitet. Laut Jerzy Sobieszczuk, Supply Chain Manager bei Lantmännen Unibake in Polen und Ungarn, „wurde das selbsttragende automatische Lager modular konzipiert, d.h. wir können das Lager erweitern, wenn unsere Produktionsrate steigt, indem wir weitere zu den fünf bereits vorhandenen Gängen hinzufügen”.
Vorteile für Lantmännen Unibake
- Vollständige Rückverfolgbarkeit: Durch die Automatisierung ist eine sehr strenge Kontrolle der Waren in der gesamten Lieferkette von Lantmännen Unibake möglich.
- Betrieb ohne Unterbrechungen: Das Lager ist 24 Stunden am Tag in Betrieb und garantiert sowohl den Eingang der Paletten aus der Fabrik und anderen Lagern als auch den Versand von ca. 100 Paletten/Stunde an die Kunden des Unternehmens in Europa.
- Automatische Anbindung an die Produktion: Das Logistikzentrum ist über einen Förderkreislauf direkt mit den Produktionslinien verbunden, wodurch erhebliche Logistikkosten eingespart werden.
- Zwei Temperaturen: Lantmännen Unibake verfügt über einen Lagerbereich für Tiefkühlprodukte und einen weiteren für gekühlte Produkte, um die höchste Qualität Ihrer Lebensmittel zu gewährleisten.
Bereich mit Gefriertemperatur | |
---|---|
Lagerkapazität: | 15.120 Paletten |
Höhe des Lagers: | 40 m |
Abmessungen der Paletten: | 800 / 1.000 x 1.200 mm |
Höchstgewicht der Paletten: | 1.000 kg |
Temperatur: | -28ºC |
Galerie
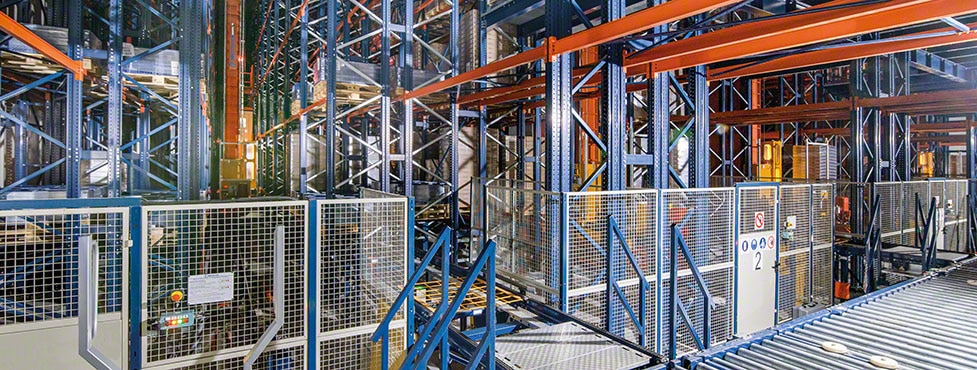
Automatisches selbsttragendes Lager von Lantmannen Unibake in Polen
Fragen Sie einen Experten