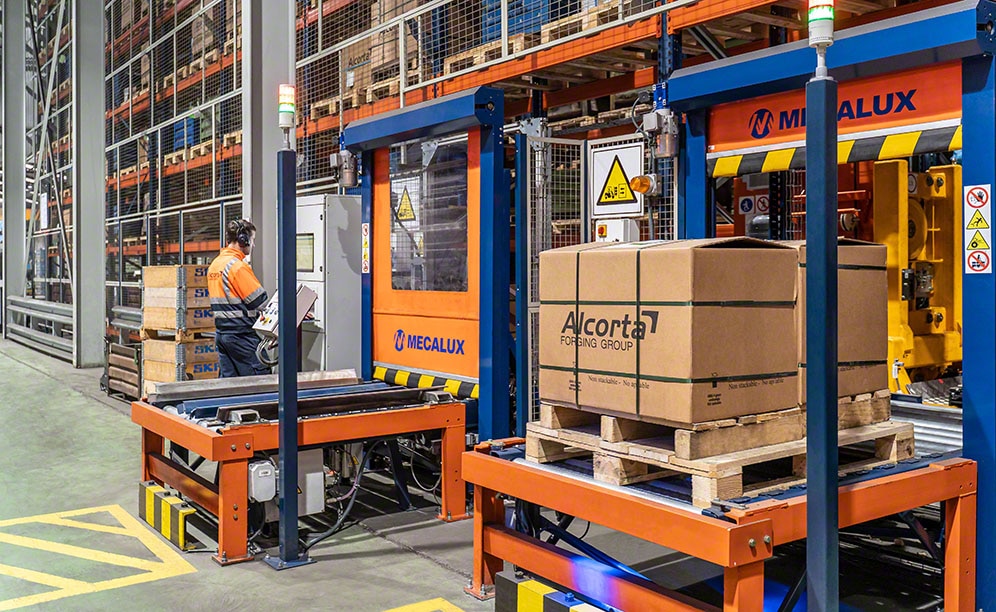
Alcorta Forging Group: Technologie, die das Lager mit der Produktion verbindet
Alcorta Forging Group hat ein automatisiertes Lager mit Autoteilen installiert, das von Easy WMS verwaltet wird
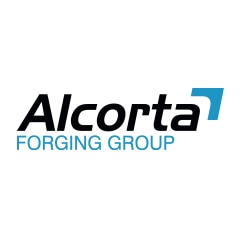
Umgestaltung und Verbesserung sind Teil der DNA des Metallunternehmens Alcorta Forging Group. Ganz in diesem Sinne hat es in seinem Werk in Elgóibar (Baskenland) ein 14 m hohes automatisiertes Lager mit einer Lagerkapazität von 1.115 Paletten in Betrieb genommen. In dem Lager, das vom Lagerverwaltungssystem Easy WMS von Mecalux gesteuert wird, werden täglich 300 Paletten mit ein- und ausgehenden Rohstoffen und Fertigprodukten präzise und sicher bewegt.
Geschmiedete Lösungen
Alcorta Forging Group ist ein über hundertjähriges Unternehmen aus der Metallbranche mit Hauptsitz in Elgóibar (Baskenland), das in Deutschland, Frankreich, der Tschechischen Republik, Südafrika, China und den Vereinigten Staaten vertreten ist.
Es wurde im Jahre 1911 gegründet und stellte zunächst Waffen her. Seit den 1980er Jahren entwirft und entwickelt es Komponenten und Ersatzteile für Unternehmen der Automobilbranche. Das Unternehmen zeichnet sich durch die Qualität seiner Produkte, sein unermüdliches Bemühen um Innovation und sein Engagement für den Umweltschutz aus.
Mit einem Jahresumsatz von über 70 Millionen Euro, von dem 85 % aus dem Export, hauptsächlich nach Frankreich, Deutschland und Südafrika, stammen, hat sich Alcorta Forging Group als eines der spanischen Unternehmen mit dem größten Wirkungsbereich etabliert.
Der Motor des Produktionszentrums
Das Unternehmen besitzt ein Werk in Elgóibar (Baskenland), in dem jährlich ca. 20 Millionen Ersatzteile und Komponenten für führende Automobilunternehmen hergestellt werden.
Für Alcorta Forging Group steht die Kundenzufriedenheit an erster Stelle, daher ist die Firma ständig darum bemüht, neue Lösungen zu entwerfen und zu entwickeln, die den Anforderungen eines immer anspruchsvolleren Marktes gerecht werden. José Antonio Fernández, Lagerleiter in Elgóibar, hebt hervor, dass das Unternehmen alle Abläufe kontinuierlich umgestaltet und verbessert, um sie noch effizienter zu machen: „Wir befinden uns in einer beispiellosen Wachstumsphase. Um noch mehr Kunden beliefern zu können, bemühen wir uns darum, alle unsere Prozesse zu verbessern und zu automatisieren, einschließlich der Logistik.“
Um dieses Ziel zu erreichen, hat Alcorta Forging Group ein automatisiertes Lager eingeweiht, das in beiden Richtungen mit den Produktionslinien verbunden ist. Es dient zur Lagerung der Rohstoffe, die später in das Werk gesandt werden sollen, und gleichzeitig zur Lagerung und zum Versand der Fertigprodukte.
José Antonio Fernández betont: „Eines der Ziele dieses Projekts besteht darin, eine zuverlässige Nachverfolgung des Bestands zu ermöglichen, von der Ankunft der Rohstoffe bis zum Versand der Aufträge an die Kunden“. Zu diesem Zweck wurde das Lagerverwaltungssystem (LVS) Easy WMS von Mecalux installiert. Diese Software sorgt für die zentralisierte Speicherung aller Informationen über die Produkte und überwacht ihre Bewegungen innerhalb des Lagers, wodurch eine vollständige Nachverfolgbarkeit gewährleistet wird.
In Bezug auf das Design des Lagers fügt Fernandez hinzu: „Wir wollten die Höhe des Gebäudes nutzen, um mehr Lagerkapazität zu erreichen.“ Das Lager ist 13 m hoch, 54 m lang und verfügt über zwei Gänge mit Regalen einfacher Tiefe, die Platz für 1.115 Paletten mit mehr als 300 verschiedenen Artikelarten bieten.
Automatisierte Lösung:
Das Lager besteht aus zwei klar getrennten Arbeitsbereichen:
- Vorderseite der Regale (Anbindung an die Produktion): Hier kommen die Fertigprodukte an und die Rohstoffe werden in die Fabrik gesandt.
- Seite des Lagers (Anbindung an die Be- und Entladerampen): Hier kommen die von den Lieferanten oder anderen Fabriken des Unternehmens gelieferten Rohstoffe an und von hier werden auch die Fertigprodukte an die Kunden versandt.
Täglich gehen im Lager insgesamt 150 Paletten ein, sowohl von den Laderampen als auch aus der Produktion. Alle Paletten müssen eine Kontrollstation durchlaufen, in der überprüft wird, ob ihr Gewicht, ihre Abmessungen und ihre Eigenschaften den im Lager festgelegten und vorgeschriebenen Parametern entsprechen.
An der gleichen Kontrollstation identifiziert Easy WMS jeden Artikel und gibt ihn ins System ein. Anschließend weist es ihm einen Stellplatz zu, der abhängig von der Nachfrage ist und davon, ob es sich um ein Fertigprodukt oder einen Rohstoff handelt. „Mit dieser Arbeitsmethode haben wir die für die Bestandskontrolle verantwortlichen Ressourcen optimiert“, sagt Jose Antonio Fernandez.
Dazu bemerkt der Lagerleiter: „Dadurch haben wir an Flexibilität gewonnen und die Lagerarbeiten sowie die Auftragszusammenstellung beschleunigt“. Außerdem kennt Easy WMS automatisch jederzeit den genauen Stellplatz jedes Artikels.
Easy WMS ist mit dem ERP-System von Alcorta Forging Group verbunden. Beide Systeme kommunizieren ständig in beiden Richtungen miteinander, um das Lager effizienter zu verwalten und alle durchgeführten logistischen Prozesse zu optimieren.
In jedem Gang arbeitet ein Regalbediengerät, das die Paletten mit einer Fahrgeschwindigkeit von 120 m/min vom Lagereingang an den vom LVS zugewiesenen Stellplatz transportiert. Diese automatisierten Geräte beschleunigen die Lagerung, die Auftragszusammenstellung und den Versand der Ware.
Die 150 Paletten, die das Lager täglich verlassen, haben zwei mögliche Zielorte: Einerseits handelt es sich um Rohstoffe, die in die Produktion gehen, und andererseits um Aufträge, die an die Kunden versandt werden. Die Paletten, die vor der Verladung in die LKWs in Gruppen zusammengestellt werden, verlassen das Lager hintereinander, unter Berücksichtigung des Auftrags und des Transportwegs.
Vorteile eines automatisierten Lagers
- Produktivität und Verfügbarkeit. Das Lager kann 24 Stunden am Tag bei voller Leistung betrieben werden.
- Reduzierung der Betriebskosten. Da die Abläufe automatisch erfolgen, ist nur eine begrenzte Anzahl von Personen und Mitteln erforderlich.
- Permanente Bestandsaufnahme. Das Verwaltungssystem identifiziert und überwacht jederzeit die Situation der Ware.
- Raumnutzung. Die Regale optimieren die Fläche, um die größtmögliche Lagerkapazität zu erzielen.
Integration und Automatisierung
Die Automatisierung der Logistik sorgt für eine kontinuierliche Warenbewegung, erhöht die Produktivität, minimiert Fehler und reduziert die Kosten von Alcorta Forging Group. Das neue Lager ist perfekt in die Produktion integriert und versorgt sie mit den nötigen Rohstoffen zur Herstellung von ca. 20 Millionen Teilen und Komponenten jährlich.
Technologie ist das Bindeglied, das Produktion und Lagerung mit höchster Präzision verbindet. Regalbediengeräte und Fördervorrichtungen verkürzen die für die Einlagerung und den Versand der Ware erforderlichen Zeiten. Außerdem gewährleistet das LVS die vollständige Nachverfolgbarkeit der Produkte.
José Antonio Fernández - Lagerleiter von Alcorta Forging Group in Elgóibar
„Das Lager erfüllt seine vorgesehene Funktion: die vollständige Integration in die Abläufe der Produktionsanlage. Durch diese automatisierte Lösung haben wir die Bestandskontrolle und die Auftragszusammenstellung optimiert.“
Vorteile für Alcorta Forging Group
- Vollständige Nachverfolgbarkeit: Dank Easy WMS kennt das Unternehmen den Ursprung und die verschiedenen Phasen, die jedes Produkt im Laufe des Produktionsprozesses durchläuft.
- Integriertes Lager: Das Lager erfüllt die wichtige Funktion, die Produktion mit Rohstoffen zu versorgen und täglich je 150 Paletten mit Fertigprodukten zu empfangen und zu versenden.
- Platzoptimierung: Die 13 m hohen und 54 m langen Regale nutzen den physischen Lagerraum und erzielen auf diese Weise mehr Lagerkapazität.
Lager von Alcorta Forging Group | |
---|---|
Lagerkapazität: | 1.115 Paletten |
Abmessungen der Paletten: | 800 / 1.000 x 1.200 mm |
Höchstgewicht der Paletten: | 1.300 kg |
Regalhöhe: | 13 m |
Regallänge: | 54 m |
Galerie
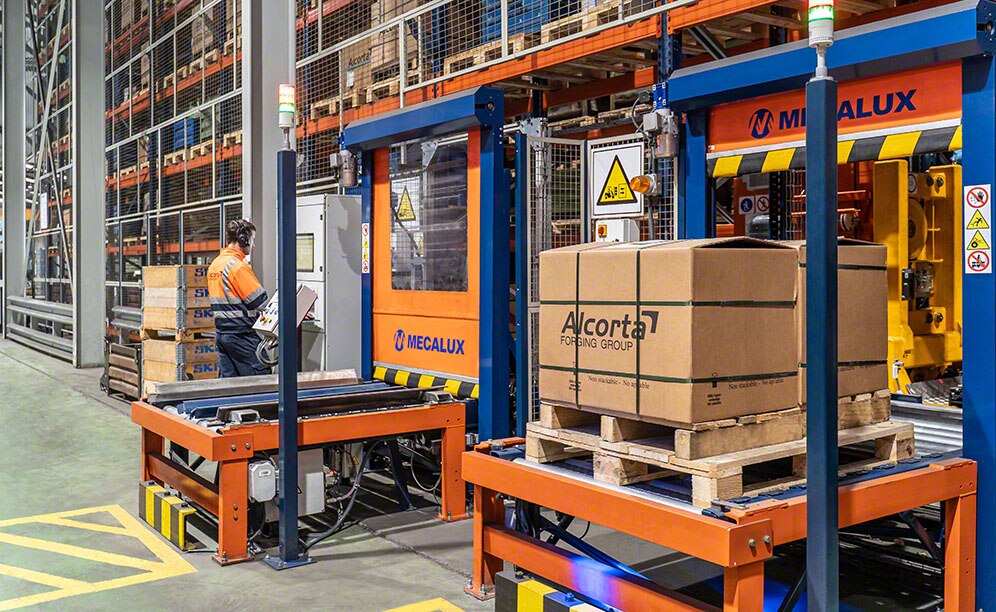
Automatisiertes Lager von Alcorta Forging Group mit Autoteilen
Fragen Sie einen Experten