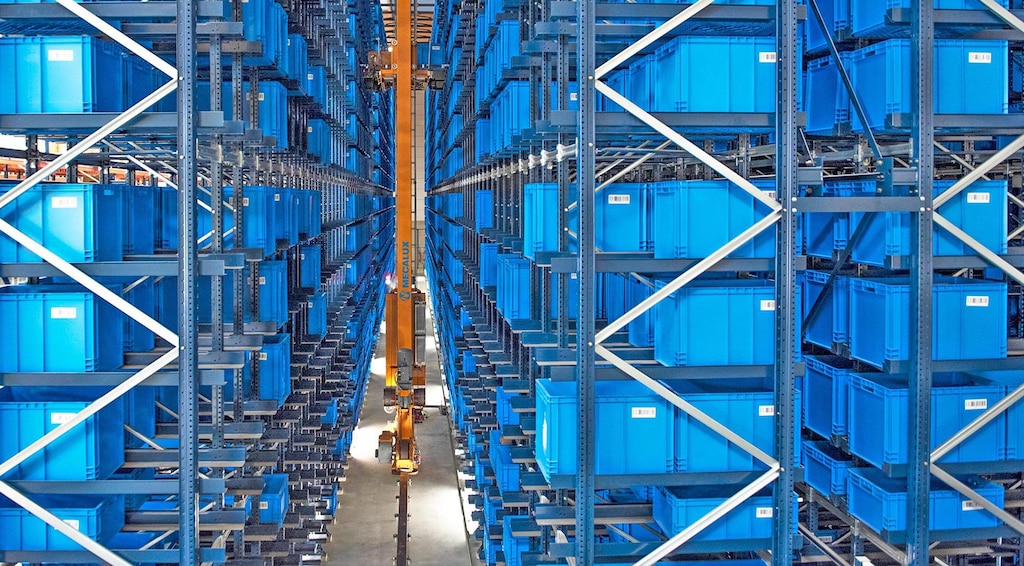
Miniload | Regalbediengerät für Behälter
Automatisiertes Lagersystem für Behälter oder Tablare, das aus Regalen, einem oder mehreren Regalbediengeräten und einer Lagerverwaltungssoftware besteht und die Lagerkapazität sowie die Kommissionierung optimiert.
Produkt
Miniload: das optimale System zur Handhabung von Behältern zur Kommissionierung
Das Regalbediengerät für Behälter (oder auch Miniload) von Mecalux ermöglicht die automatische Lagerung und Kommissionierung von Behältern, Kartons sowie Tablaren und erzielt einen erhöhten Durchsatz in Ihrem automatischen Kleinteilelager. Es nutzt auch in kleineren Lagerhallen den Raum optimal aus und garantiert die sichere Lagerung von wertvollen Gütern.
Unser Miniload ist in verschiedenen Konfigurationen erhältlich, um die Lagerkapazität, Schnelligkeit und Sicherheit Ihrer Lagerungsprozesse zu verbessern. Es ist möglich, zwischen verschiedenen Modellen von Regalbediengeräten und mehreren Optionen zur Gestaltung des Kommissionier- und Handhabungsbereichs zu wählen. Automatisierte Lager mit Regalbediengeräten für Behälter beschleunigen die Vorgänge zur Platzierung und Entnahme der Last und transportieren die Ware direkt zum Kommissionierer.
Vorteile
Die ideale Lösung für Unternehmen mit einem umfangreichen Kommissioniervolumen
Das Miniloadsystem arbeitet nach dem Prinzip „Ware zum Mann“, sodass sich der Kommissionierer nicht von seinem Platz bewegen muss, sondern der Roboter dafür verantwortlich ist, die zur Auftragszusammenstellung benötigten Artikel zum Kommissionierplatz zu bringen. Die verschiedenen Versionen von Miniloads können 120 bis 600 Behälter pro Stunde in kombinierten Zyklen handhaben: Bei einer einzigen Fahrbewegung wird die gleiche Anzahl von Behältern in den Regalen abgesetzt und von dort entnommen.
- Automatisierung der Ein- und Auslagerung der Produkte.
- Beseitigung von Fehlern, die bei der manuellen Lagerverwaltung auftreten können, sowie ständige Inventur.
- Kontinuierlicher Warenfluss und Betriebsbereitschaft an 365 Tagen im Jahr.
- Maximale Ergonomie und Sicherheit, um den Kommissionierern die Ausführung der Arbeitsaufträge so weit wie möglich zu erleichtern.
- Verzehnfacht die Lagerkapazität eines herkömmlichen Lagers.
- Regalbediengeräte für Behälter arbeiten in Gängen, die nur 80 cm breit sind und bis zu 40 m lang und bis zu 20 m hoch sein können.
- Senkung der Personal- und Wartungskosten.
- Erhöhter Durchsatz im Kleinteilelager sowie minimaler Energieverbrauch durch energieeffiziente Technik.
- Das Miniloadsystem kann bei verschiedenen Temperaturen arbeiten, von Gefriertemperaturen bis zu 45 °C.
- Breites Sortiment an Gabeln oder Lastaufnahmemitteln, die sich an verschiedene Arten und Größen von Ladeeinheiten anpassen: Kunststoffbehälter, Kartons oder Metalltablare in verschiedenen Größen.
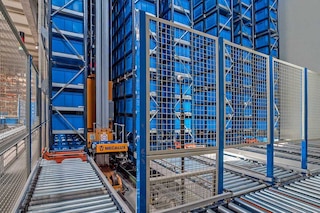
Anwendungen
Geschwindigkeit, Lagerkapazität und Präzision bei der Kommissionierung für alle Branchen
Unsere innovativen Miniloads sind besonders effektiv für Unternehmen mit einer umfangreichen Auftragszusammenstellung und ganz allgemein eine ideale Lösung in folgenden Fällen:
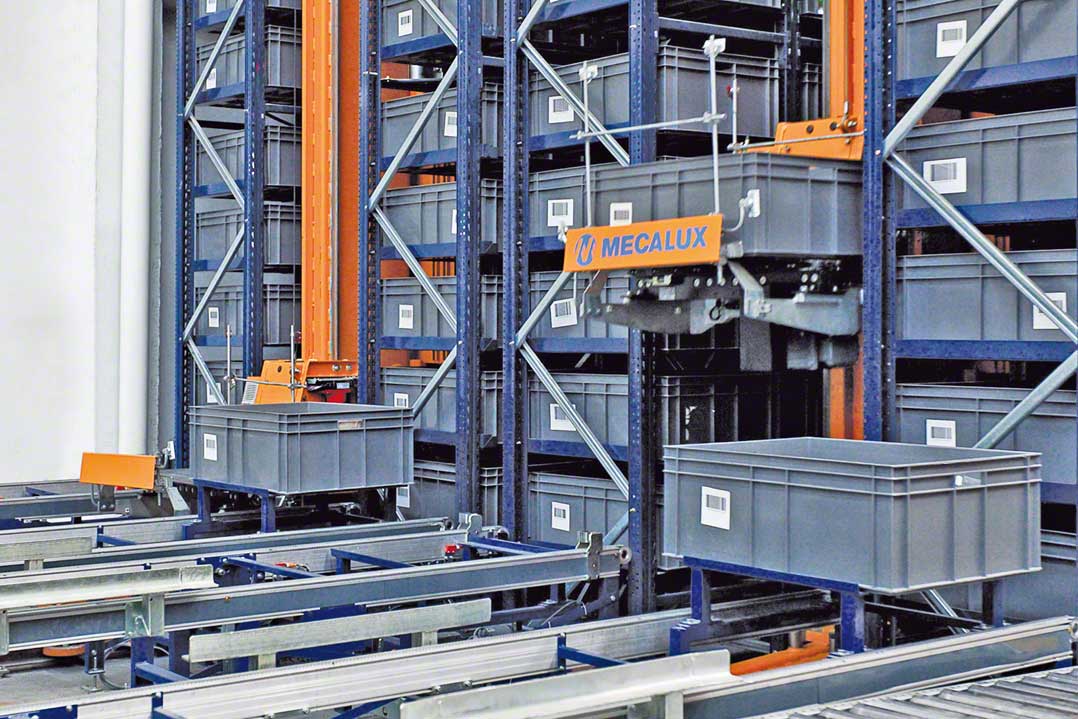
Bereichsweise Kommissionierung
Beispiele für verschiedene Anordnungen von Kommissionier- und Handhabungsbereichen, abhängig von den Anforderungen des Unternehmens
Lager mit einem einzigen Gang
Die einfachste Lösung für derartige Anlagen ist die Montage eines U-förmigen Förderkreislaufs am Regaleingang, an dem der Kommissionierer die Auftragszusammenstellung und das Wiederauffüllen mithilfe verschiedener Geräte (Bildschirm, Barcodeleser, Bestätigungstasten, Abmessungskontrolle usw.) durchführt.
Lager mit zwei oder mehr Gängen
Anzahl und Form der Kommissionierplätze hängen von der Anzahl der durchzuführenden Vorgänge und dem zur Auftragszusammenstellung genutzten Verfahren ab. Einige der vielen möglichen Formate sind die folgenden:
- Zwei Gänge und zwei voneinander unabhängige Kommissionierplätze: Diese Lösung verbindet zwei Lager mit je einem Gang. Jeder unabhängige Platz erhält die in einem Gang gelagerten Behälter und ermöglicht die Bearbeitung durch einen einzigen Kommissionierer. Das Auffüllen der Produkte erfolgt am Kommissionierplatz selbst.
- Zwei Gänge mit einem Kommissionierplatz: Hierbei ist die Installation eines unidirektionalen Querförderers erforderlich, der die verschiedenen Eingangs- und Ausgangsförderer mit dem Kommissionierplatz verbindet. Das Auffüllen kann direkt am Kommissionierplatz oder mithilfe einer zusätzlichen Fördervorrichtung, die mit einem Produktionszentrum oder einer Auffüllstation verbunden ist, erfolgen.
- Zwei Gänge und zwei Kommissionierplätze: zwei Querförderer, die den Transport der Eingangs- und Ausgangsbehälter ermöglichen. Genau wie bei der vorherigen Lösung kann das Auffüllen direkt am Kommissionierplatz oder mithilfe einer zusätzlichen Fördervorrichtung erfolgen.
- Mehrere Gänge und mehrere Kommissionierplätze: Hierbei sind mindestens zwei Linien mit Querförderern, die die Ein- und Ausgangsförderer des Lagers mit den Kommissionierplätzen verbinden, sowie die Einrichtung einer speziellen Auffüllstation erforderlich.
- Kommissionierung auf einem seitlich angebrachten Durchlaufregal: optimale Lösung, wenn eine große Anzahl bestimmter Artikelarten wiederholt entnommen werden muss. Dabei werden die Durchlaufregale auf den unteren Ebenen an der Seite des Behälterlagers montiert.
- Frontale Massenkommissionierung: Die Konfiguration erfolgt abhängig von der Anzahl der erforderlichen Kommissionierplätze, der Anzahl der Regalbediengeräte, den Linien zur Auftragszusammenstellung und der Anzahl der von den Kommissionierern gleichzeitig zusammenzustellenden Aufträge.
- Kommissionierplätze in angrenzenden Bereichen: Die Plätze befinden sich in angrenzenden Bereichen und der Platz, den sie bei frontaler Anordnung einnehmen würden, wird als Lager genutzt, wodurch sich die Lagerfläche vergrößert.
Komponenten
Sicherheit
Eine leistungsstarke Steuerungssoftware und verschiedene mechanische und elektronische Vorrichtungen sorgen gemeinsam dafür, dass die Bewegungen des Regalbediengeräts für Behälter präzise durchgeführt werden und sicher sind, sowohl für die Lagerarbeiter als auch für die Ware und das System selbst.
- Sicherheit der Lagerarbeiter: Offene Flächen werden durch Metallgitterabsperrungen gesichert, um den Kontakt der Lagerarbeiter mit in Bewegung befindlichen Elementen zu verhindern. Beim Öffnen der Türen zum Gang wird die Bewegung der Geräte sofort gestoppt. Dadurch wird die Sicherheit der Lagerarbeiter gewährleistet, genauso wie durch die ergonomische Position der Kommissionierplätze.
- Sicherheit der Ware: Die Unzugänglichkeit der Ware für unbefugte Personen, die Verringerung des Warenschwunds aus unbekanntem Grund, die Aufrechterhaltung des einwandfreien Zustands der Ware, die Verringerung von Schäden durch falsche Handhabung und die Reduzierung von Zwischenkontrollen tragen zur Sicherheit der Ware bei.
- Sicherheit des Regalbediengeräts: Das Miniload von Mecalux ist mit verschiedenen speziellen Sicherheitselementen ausgestattet, die den perfekten Betrieb des gesamten Systems gewährleisten, z. B. mechanisch-hydraulische Anschläge an den Gangenden, Leistungsschutzschalter und Thermosonde an den Motoren, Intensitätsbegrenzer für die Motoren usw.
Downloads
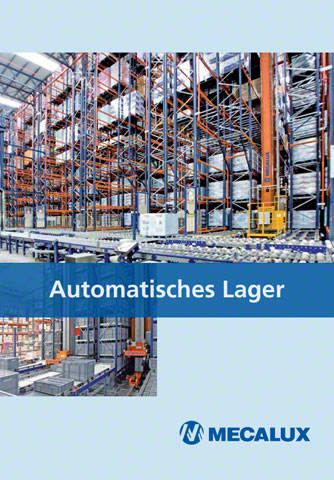
Katalog
DownloadFragen Sie einen Experten