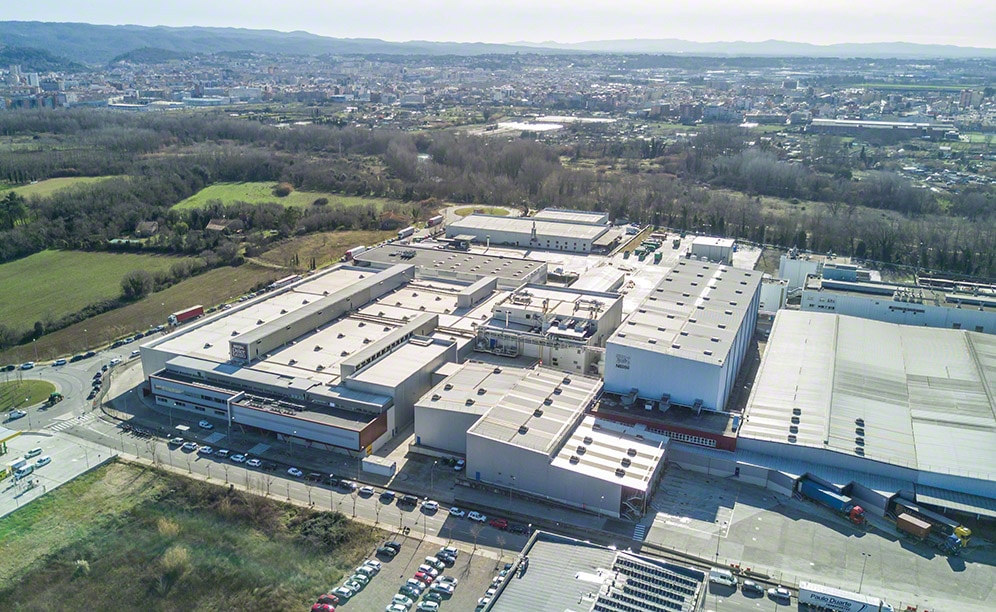
Nestlé "beschleunigt" seine Dolce Gusto Fabrik mit einem automatischen Lagertransportsystem
Ein effizientes Fördersystem von Mecalux im Produktionszentrum von Nestlé in Girona
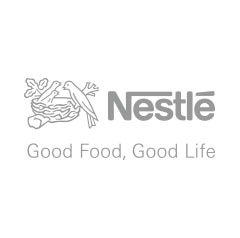
Das Nescafé-Werk in Girona (Spanien) ist eines der konkurrenzfähigsten Produktionszentren von Nestlé auf der ganzen Welt. Es handelt sich um ein sehr ehrgeiziges Projekt, das laufend erweitert wird, um sich an die aktuellen Bedürfnisse des Marktes anzupassen. Seit 1990 arbeitet Mecalux in diesem Zentrum mit Nestlé zusammen. Dabei wurden stets die effizientesten Lösungen entwickelt und implementiert, um die Logistik des Unternehmens immer weiter zu verbessern und die Zukunftsaussichten zu stärken.
Informationen zu Nestlé und Nescafé
Nestlé ist weltweiter Marktführer im Bereich Nahrungsmittel und Getränke und in über 191 Ländern wirtschaftlich präsent. Das Unternehmen vertreibt ca. 2000 Marken, die ein breites Produktsortiment abdecken:Kindernahrung, abgefülltes Wasser, Frühstückscerealien, Kaffee und Tee, Süßwaren, Milchprodukte, Tiernahrung, Schokoladen usw.
Derzeit besitzt Nestlé zehn Produktionszentren in Spanien, die auf fünf Autonome Gemeinschaften verteilt sind. Diese Fabriken zeichnen sich durch ihre hohe Leistungsfähigkeit aus und exportieren 44 % ihrer Produktion ins Ausland.
1968 errichtete Nestlé ein Produktionszentrum in Girona (Spanien), in dem der lösliche Kaffee Nescafé hergestellt wird und seit 2009 ebenfalls die Kaffeekapseln Nescafé Dolce Gusto produziert werden. Dieses Zentrum ist im Laufe der letzten Jahre stark gewachsen und hat sich zur größten Produktionsstätte für löslichen Kaffee des multinationalen Konzerns entwickelt.
Bei Nescafé handelt es sich um die Instantkaffee-Marke von Nestlé. Seine Ursprünge reichen bis ins Jahr 1938 zurück. Seitdem wurde das Sortiment erweitert, indem neue, innovative Rezepte und Geschmacksrichtungen eingeführt wurden, um ein Angebot für jeden Geschmack, jede Gelegenheit und jeden Geldbeutel zu bieten.
Mecalux und Nestlé
Die Zusammenarbeit zwischen den beiden Firmen begann 1990, als Mecalux ein automatisches Hochregallager für Paletten in Silobauweise im Nescafé-Werk in Girona errichtete.
Dieses Lager, das 25 m hoch und 107 m lang ist, besteht aus sieben Gängen mit Regalanlagen einfacher Tiefe auf beiden Seiten, die eine Lagerkapazität von 16.380 Paletten bieten. Dort werden die Fertigprodukte gelagert, die auf den Versand warten.
Einige Jahre später, im Jahre 2006, errichtete Mecalux ein zweites, 21 m hohes Hochregallager in Silobauweise nur wenige Meter vom ersten Lager entfernt. Es besteht aus zwei Gängen mit Regalanlagen einfacher Tiefe, in denen insgesamt 740 Behälter mit Rohstoffen gelagert werden.
Das Lager ist auf die Abmessungen und Eigenschaften der Behälter zugeschnitten, mit denen Nestlé arbeitet:Sie sind 1210 x 1060 x 1810 mm groß und besitzen keine unteren Kufen. Ein- und Ausgänge erfolgen automatisch mithilfe von Fördervorrichtungen, die die Ware direkt bis ans Ende der beiden Lagergänge befördern. Um den Transport auf den Fördervorrichtungen zu erleichtern, werden die Behälter auf Trägerpaletten gesetzt.
Außerdem verfügen die Ebenen der Regale über Träger, auf die die Behälter ohne die Trägerpalette gesetzt werden können.
Nescafé Dolce Gusto
Nestlé begann 2005 mit der Vermarktung der Kaffee- und Teekapseln Nescafé Dolce Gusto. Ursprünglich befand sich die Produktionsstätte in Großbritannien, aber nachdem das Produkt in Spanien sehr viel Anklang fand, entschied sich das Unternehmen, dort eine neue Fabrik zu errichten, um den Markt schneller beliefern zu können.
Das Unternehmen hat 2009 das Produktionszentrum in Girona erweitert und die Fabrik für Nescafé Dolce Gusto neben der bereits vorhandenen Anlage errichtet. In Zusammenarbeit mit Mecalux wurde dieses Zentrum in mehreren Phasen erweitert und jeweils an die neuen Anforderungen von Nestlé angepasst:
Erste Maßnahme
Das Unternehmen bat Mecalux um Rat, weil es die neue Fabrik für Nescafé Dolce Gusto mit dem Lager für Fertigprodukte verbinden wollte. Es benötigte ein rasches Transportsystem, das für einen konstanten Warenfluss zwischen beiden Punkten sorgen sollte. Das Projekt stellte eine große Herausforderung dar, da die beiden voneinander getrennten Hallen durch einen Gang verbunden werden mussten. Mecalux schlug den Bau einer überdachten Hochbrücke vor, die sich 6 m über dem Boden befindet und die beiden Gebäude verbindet, in deren Innerem ein Förderkreislauf verläuft.
Durch diese Lösung wird eine Beeinträchtigung des üblichen Verkehrs vermieden und die Produkte werden gleichzeitig vor Witterung geschützt. Die Rollenförderer bewegen sich mit einer Geschwindigkeit von 20 m/min. Sie funktionieren vollautomatisch und es sind nur minimale menschliche Eingriffe nötig, wodurch mögliche Fehler, die durch manuelle Handhabung entstehen könnten, vermieden werden.
Zweite Maßnahme
2011 installierte Nestlé zwei weitere Hubsysteme, die die beiden Ebenen des Produktionszentrums miteinander verbinden.
Ein Förderkreislauf transportiert die Ware direkt zu den Hubsystemen. Die Fördervorrichtungen befinden sich auf einem höheren Niveau und ruhen auf einer widerstandsfähigen Struktur, die ihre Standfestigkeit gewährleistet.
Auf diese Weise kann die Fläche des Produktionszentrums genutzt und eine Beeinträchtigung der übrigen Abläufe vermieden werden.
Dritte Maßnahme
Angesichts des wachsenden Umsatzes von Nescafé Dolce Gusto musste das Unternehmen 2012 die Anzahl der Palettenbewegungen zwischen dem Produktionszentrum und dem Fertigproduktlager erhöhen.
Zu diesem Zweck lieferte Mecalux ein neues Hubsystem für den Ausgang aus der Produktion, wodurch die ursprüngliche Anzahl der Palettenbewegungen verdoppelt wurde.
Vierte Maßnahme
Nestlé musste das Produktionszentrum mit der Versandhalle verbinden, um die Ware direkt dorthin bringen zu können, ohne sie vorher durch das Lager zu transportieren.
Mecalux installierte einen neuen Ausgang im Förderkreislauf, der das Produktionszentrum verlässt. Die Ware läuft über die Hochbrücke, und vor ihrem Eintritt in das Lager übernimmt ein Hubsystem die entsprechenden Paletten und bringt sie hinunter in den Versandbereich.
Das Unternehmen wollte den Versandbereich automatisieren, um auf diese Weise die Leistung aller dort ablaufenden Vorgänge zu maximieren:
- Palettenstapelbereich. Ein Verfahrwagen verteilt die Paletten auf sechs Fördervorrichtungen, wo sie darauf warten, zum automatischen Palettenunterleger gebracht zu werden, der die Paletten aufeinander stapelt.
- Kanäle zur Ladevorbereitung. Ein anderer Verfahrwagen holt die gestapelten Paletten ab und verteilt sie auf sechs Kanäle zur Ladevorbereitung, die aus Rollenförderern mit einer leichten Neigung bestehen. Dieses System gruppiert Paletten derselben Bestellung oder Route.
- Ladevorbereitung auf dem Boden. Gegenüber den dynamischen Kanälen wurde ein Bereich zur Ladevorbereitung auf dem Boden eingerichtet. Die Paletten werden vor der Beladung des Transportlastwagens vorbereitet. Auf diese Weise wird vermieden, dass dieser auf die aus dem Lager kommenden Waren warten muss.
Fünfte Maßnahme
Neben der Versandhalle befindet sich das Lager für Bigbags (oder große Säcke) für Rohstoffe. Diese Säcke werden auf Paletten gesetzt, um den Transport und die Lagerung in den Regalen zu erleichtern.
Der Eingang in das Lager erfolgt automatisch mithilfe eines Förderkreislaufs. Die Paletten durchlaufen eine Prüfstelle, die ihren Zustand feststellt und prüft, ob ihr Gewicht und ihre Abmessungen den festgelegten Qualitätsanforderungen entsprechen.
Anschließend transportiert ein Hubsystem die Ware bis zur oberen Ebene, auf der sich zwei Blöcke mit Drive-in-Kompakt-Palettenregalanlagen befinden.
Die Regalanlagen bestehen aus einer Reihe von 6,5 m hohen Ladegassen mit jeweils drei Ebenen. Jede Ebene verfügt über besonders widerstandsfähige Auflageschienen aus verzinktem Stahlblech, auf denen die Paletten mit den Säcken gelagert werden.
Steuerungssoftware
Angesichts des Umfangs dieses Produktionszentrums wird unbedingt ein elektronisches System benötigt, das alle Bewegungen der installierten automatischen Fördermittel kontrolliert und steuert.
Mecalux hat das Steuerungsmodul Galileo installiert, das den Fördervorrichtungen, Verfahrwagen und Hubsystemen die Anweisungen zur Bewegung erteilt und ihre kontinuierliche und kontrollierte Bewegung gewährleistet.
Galileo verfügt über eine sehr intuitive Benutzeroberfläche und ist in der Lage, die elektromechanische Funktionsweise der gesamten automatischen Installation mithilfe eines SCADA-Systems zu simulieren.
Es kommuniziert fortlaufend in beide Richtungen mit der Lagerverwaltungssoftware und mit dem ERP von Nestlé. Aufgrund der Maßnahmen konnte die Firma die Rentabilität aller Prozesse, die in ihrem Produktionszentrum ablaufen, maximieren.
Vorteile für Nestlé:
- Effizientes Fördersystem: Die Fördervorrichtungen sorgen für große Schnelligkeit beim Transport der Waren in die verschiedenen Bereiche des Produktionszentrums und des Lagers.
- Hoher Warenfluss: Durch den automatischen Förderkreislauf und die Hubsysteme ist es möglich, die für Nestlé erforderliche Zahl von Palettenbewegungen zu erreichen.
- Sichere Installation: Die automatischen Elemente sind geschützt und der Zutritt von unbefugtem Personal wird verhindert, um Zwischenfälle zu vermeiden.
Galerie
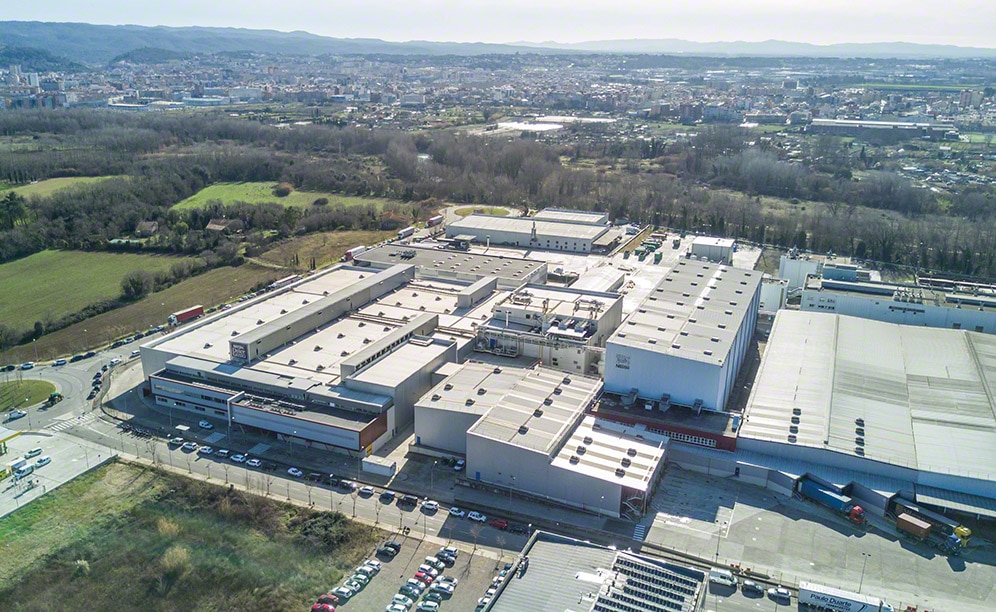
Mecalux ein automatisches Hochregallager für Paletten in Silobauweise im Nescafé-Werk in Girona errichtete
Fragen Sie einen Experten